Determining the chirality of carbon nanotubes (CNTs) during their synthesis is a complex but not impossible task. Chirality, which defines the electronic properties of CNTs, is influenced by the arrangement of carbon atoms in the hexagonal lattice. While controlling chirality during synthesis remains a significant challenge, advancements in synthesis techniques, such as chemical vapor deposition (CVD), and in-situ characterization methods have made it possible to influence and monitor chirality to some extent. Techniques like Raman spectroscopy, electron diffraction, and real-time imaging are being explored to achieve better control and determination of chirality during the synthesis process. However, achieving precise chirality control still requires further research and technological breakthroughs.
Key Points Explained:
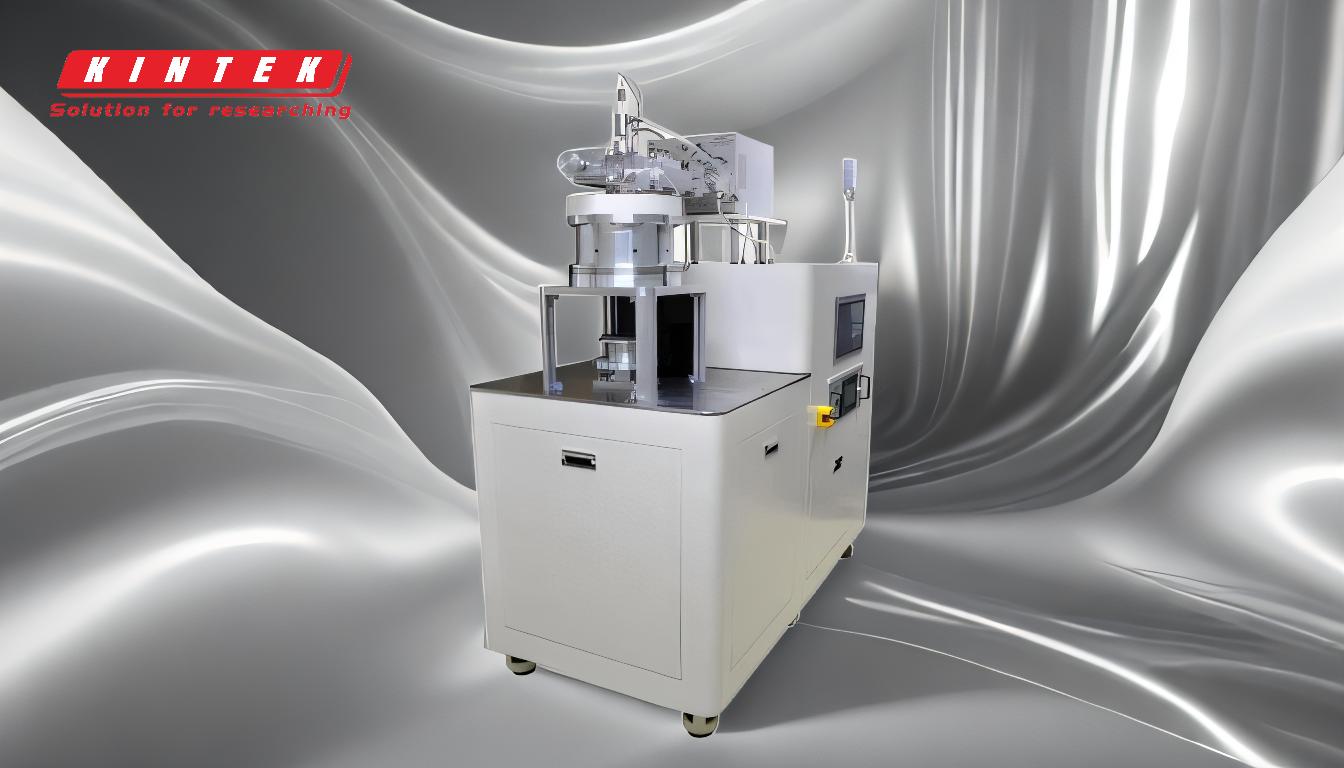
-
Understanding Chirality in CNTs:
- Chirality in CNTs refers to the specific arrangement of carbon atoms in the hexagonal lattice, described by the chiral vector (n, m). This vector determines whether the CNT is metallic, semiconducting, or semi-metallic.
- Chirality is crucial because it directly affects the electronic, thermal, and mechanical properties of CNTs, making it a critical parameter for applications in electronics, photonics, and materials science.
-
Challenges in Controlling Chirality During Synthesis:
- The synthesis of CNTs, particularly using methods like chemical vapor deposition (CVD), often results in a mixture of chiralities due to the stochastic nature of the growth process.
- Factors such as catalyst composition, temperature, pressure, and carbon feedstock influence chirality, but achieving precise control remains difficult.
-
Techniques to Influence Chirality During Synthesis:
- Catalyst Engineering: Tailoring the size, composition, and structure of catalysts can influence the chirality of CNTs. For example, using bimetallic catalysts or nanoparticles with specific crystallographic orientations can promote the growth of CNTs with desired chiralities.
- Growth Conditions: Optimizing parameters like temperature, gas flow rates, and carbon source concentration can help achieve better chirality control. For instance, lower growth temperatures are often associated with narrower chirality distributions.
-
In-Situ Characterization Methods:
- Raman Spectroscopy: This technique can provide real-time information about the chirality of CNTs during synthesis by analyzing the radial breathing mode (RBM) and G-band features.
- Electron Diffraction: High-resolution transmission electron microscopy (HRTEM) combined with electron diffraction can be used to determine the chirality of individual CNTs during growth.
- Real-Time Imaging: Advances in microscopy allow for the observation of CNT growth dynamics, enabling researchers to correlate growth conditions with chirality.
-
Post-Synthesis Characterization:
- While not directly part of the synthesis process, post-synthesis techniques like atomic force microscopy (AFM) and scanning tunneling microscopy (STM) can provide detailed information about the chirality of synthesized CNTs. This data can be used to refine synthesis protocols.
-
Current Limitations and Future Directions:
- Despite progress, achieving precise chirality control during synthesis remains a significant challenge. Most methods still produce a mixture of chiralities, requiring post-synthesis separation or purification.
- Future research may focus on developing more sophisticated catalysts, advanced in-situ monitoring tools, and machine learning algorithms to predict and control chirality during synthesis.
In summary, while determining and controlling the chirality of CNTs during synthesis is challenging, ongoing advancements in synthesis techniques and characterization methods are making it increasingly feasible. Achieving precise chirality control will require further innovation and interdisciplinary collaboration.
Summary Table:
Aspect | Details |
---|---|
Chirality Definition | Arrangement of carbon atoms in the hexagonal lattice, described by (n, m). |
Key Challenges | Stochastic growth process, mixture of chiralities, precise control is hard. |
Influencing Techniques | Catalyst engineering, optimized growth conditions, in-situ characterization. |
Characterization Methods | Raman spectroscopy, electron diffraction, real-time imaging, AFM, STM. |
Future Directions | Advanced catalysts, in-situ monitoring, machine learning for chirality control. |
Discover how to optimize CNT synthesis for precise chirality control—contact our experts today!