Metal foam is indeed an expensive material, primarily due to its complex production processes, the high cost of raw materials, and the limited scale of production. These factors contribute to its high price, making it less accessible for widespread use despite its innovative and versatile properties. Below, we will explore the key reasons behind its high cost and how these factors impact its market availability and applications.
Key Points Explained:
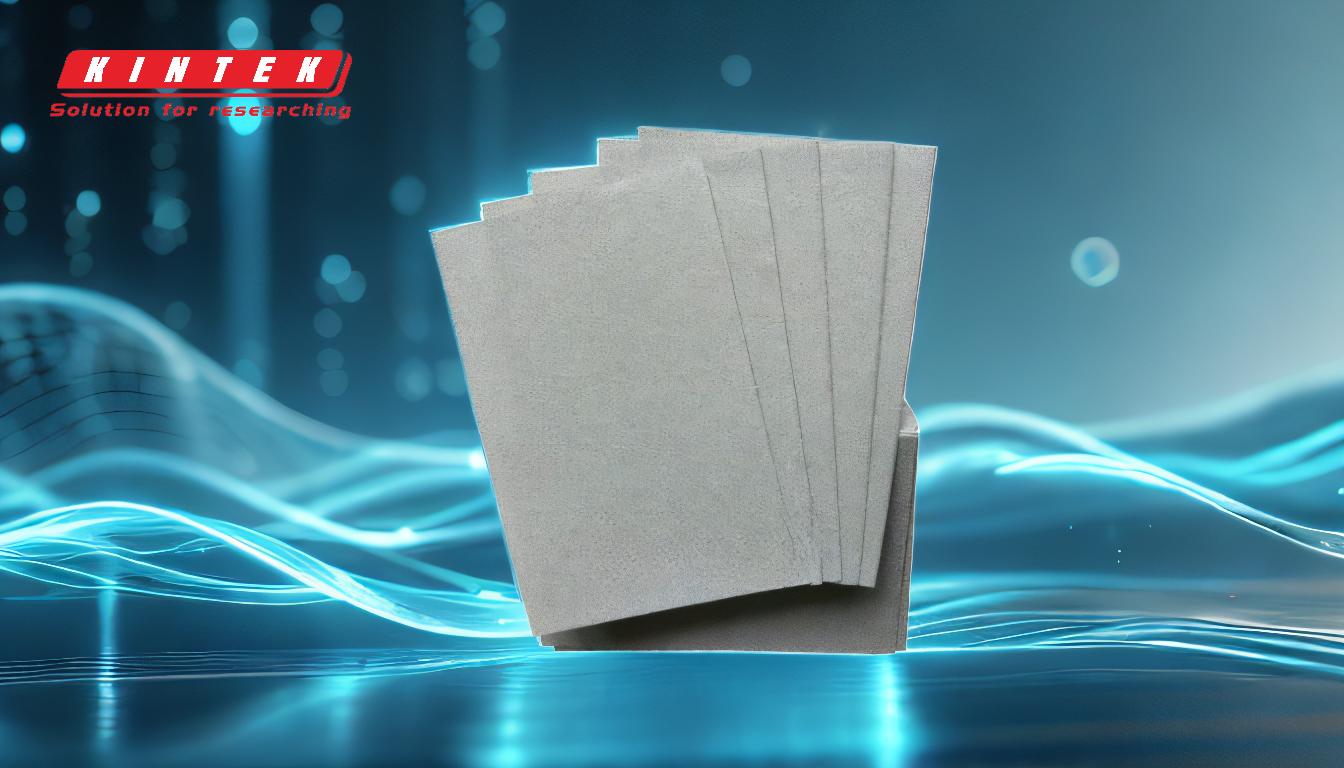
-
Complex Production Processes
- Metal foam manufacturing involves intricate and specialized techniques, such as powder metallurgy, gas injection, or electrodeposition. These processes require advanced equipment, precise control, and skilled labor, all of which drive up production costs.
- The production process often includes multiple steps, such as creating a precursor material, foaming, and post-processing, which add to the overall expense.
-
Expensive Raw Materials
- Metal foams are typically made from high-quality metals like aluminum, nickel, or titanium, which are inherently costly.
- The use of additives or foaming agents to create the porous structure further increases material expenses.
-
Limited Production Scale
- Metal foam is not yet produced on a large industrial scale, which means manufacturers cannot benefit from economies of scale. Smaller production runs result in higher per-unit costs.
- The niche nature of its applications means demand is relatively low, discouraging large-scale investment in production facilities.
-
High Research and Development Costs
- Developing new and improved metal foam formulations and manufacturing methods requires significant R&D investment. These costs are often passed on to the consumer.
- Customization for specific applications (e.g., aerospace or medical) further increases expenses due to the need for tailored solutions.
-
Applications and Market Impact
- Metal foam is primarily used in high-end industries such as aerospace, automotive, and energy, where its lightweight and high-strength properties justify the cost.
- In industries where cost sensitivity is high, the expense of metal foam limits its adoption, despite its potential benefits.
In conclusion, while metal foam offers unique advantages, its high cost remains a significant barrier to broader adoption. Efforts to streamline production, reduce material costs, and scale up manufacturing could help make it more accessible in the future.
Summary Table:
Key Factor | Details |
---|---|
Complex Production | Involves advanced techniques like powder metallurgy, gas injection, etc. |
Expensive Raw Materials | Made from high-quality metals (e.g., aluminum, nickel, titanium). |
Limited Production Scale | Small-scale production increases per-unit costs. |
High R&D Costs | Significant investment in developing formulations and methods. |
Applications | Used in aerospace, automotive, and energy industries due to unique properties. |
Interested in learning more about metal foam and its applications? Contact our experts today to discuss how it can benefit your projects!