Pulsed DC sputtering and DC sputtering are both widely used in physical vapor deposition (PVD) processes, but they serve different purposes and have distinct advantages and limitations. DC sputtering is a straightforward and cost-effective method, ideal for conductive materials like pure metals, offering high deposition rates and scalability for large substrates. However, it struggles with dielectric materials due to charge accumulation and arcing issues. Pulsed DC sputtering addresses these challenges by using a pulsed power source, which prevents charge buildup and reduces arcing, making it more suitable for dielectric and insulating materials. While DC sputtering is simpler and more economical, pulsed DC sputtering provides better control and stability for complex applications, particularly when working with non-conductive targets.
Key Points Explained:
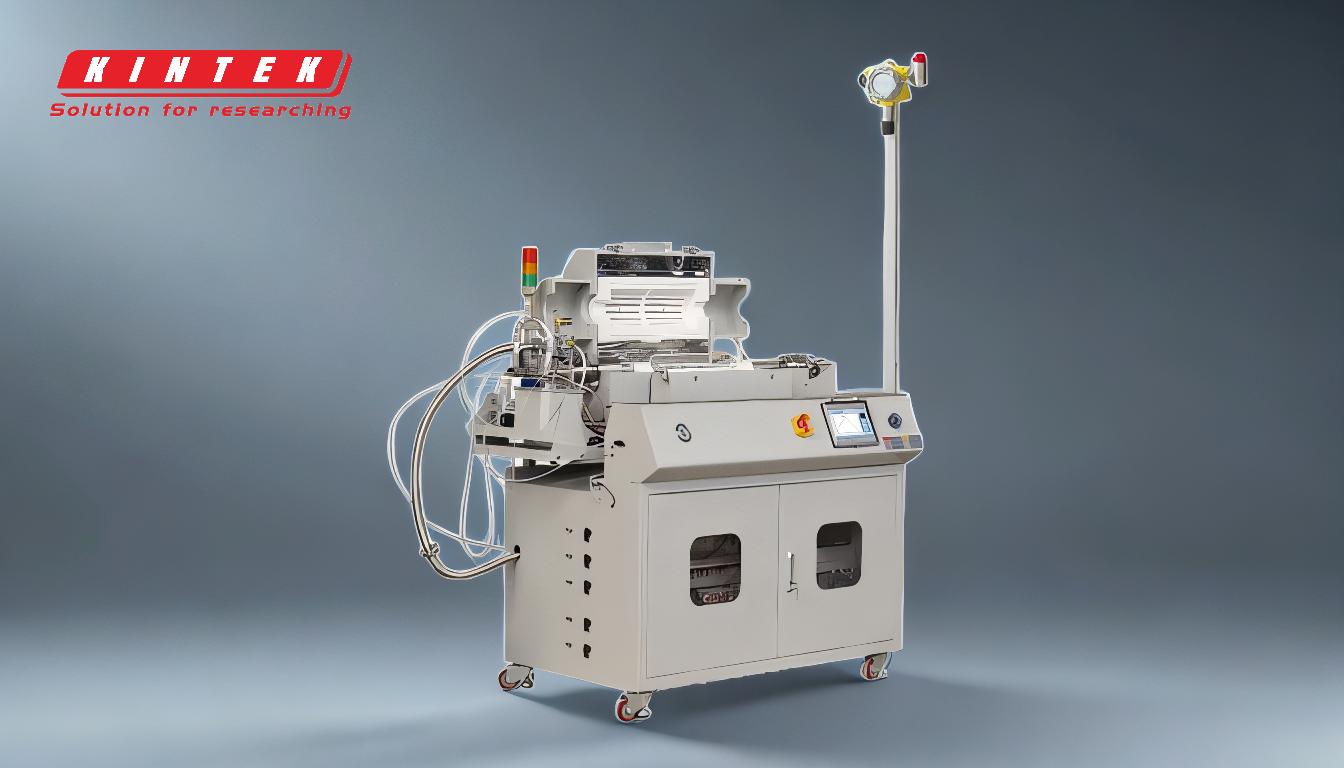
-
DC Sputtering Overview:
- DC sputtering uses a direct current (DC) power source and is primarily suited for conductive materials like pure metals (e.g., Iron, Copper, Nickel).
- It offers high deposition rates, making it efficient for large-scale industrial applications.
- It is cost-effective, easy to control, and scalable for large substrates.
- However, DC sputtering is not suitable for dielectric materials due to charge accumulation and arcing, which can damage the power supply and the target material.
-
Pulsed DC Sputtering Overview:
- Pulsed DC sputtering uses a pulsed power source, which alternates the polarity of the current to prevent charge buildup on the target material.
- This method is particularly effective for dielectric and insulating materials, as it mitigates arcing and improves process stability.
- It allows for better control over the deposition process, making it suitable for applications requiring high-quality, uniform coatings.
-
Comparison of Advantages:
-
DC Sputtering:
- Simplicity and low cost make it ideal for conductive materials and large-scale production.
- High deposition rates ensure efficient processing of large substrates.
-
Pulsed DC Sputtering:
- Prevents charge accumulation and arcing, making it suitable for dielectric materials.
- Offers better process control and stability, especially for complex or sensitive applications.
-
DC Sputtering:
-
Comparison of Limitations:
-
DC Sputtering:
- Ineffective for dielectric materials due to charge buildup and arcing.
- Limited to conductive targets, restricting its versatility.
-
Pulsed DC Sputtering:
- More complex and expensive than DC sputtering due to the need for specialized power supplies.
- May have slightly lower deposition rates compared to DC sputtering for conductive materials.
-
DC Sputtering:
-
Applications:
-
DC Sputtering:
- Widely used in industries requiring metal coatings, such as electronics, optics, and decorative coatings.
-
Pulsed DC Sputtering:
- Preferred for applications involving dielectric or insulating materials, such as semiconductor manufacturing and advanced optics.
-
DC Sputtering:
-
Cost and Scalability:
- DC sputtering is more economical and scalable for large-scale production, especially when working with conductive materials.
- Pulsed DC sputtering, while more expensive, provides added value for applications requiring precise control and the ability to handle non-conductive materials.
In conclusion, the choice between pulsed DC sputtering and DC sputtering depends on the specific requirements of the application. DC sputtering is better for cost-effective, large-scale production of conductive coatings, while pulsed DC sputtering excels in handling dielectric materials and providing greater process control.
Summary Table:
Aspect | DC Sputtering | Pulsed DC Sputtering |
---|---|---|
Best For | Conductive materials (e.g., metals like Iron, Copper, Nickel) | Dielectric and insulating materials |
Advantages | Cost-effective, high deposition rates, scalable for large substrates | Prevents charge buildup, reduces arcing, better process control and stability |
Limitations | Ineffective for dielectric materials, limited to conductive targets | More complex and expensive, slightly lower deposition rates for conductive materials |
Applications | Electronics, optics, decorative coatings | Semiconductor manufacturing, advanced optics |
Cost & Scalability | Economical and scalable for large-scale production | More expensive but offers added value for precise control and non-conductive materials |
Need help choosing the right sputtering method for your application? Contact our experts today!