Physical Vapor Deposition (PVD) and Electrochemical Deposition (ECD) are two distinct thin-film deposition technologies used in various industries, including semiconductor manufacturing, optics, and decorative coatings. While they share some overlapping applications, they are not direct competitors but rather complementary technologies. PVD involves the physical transfer of material from a target to a substrate in a vacuum environment, while ECD relies on electrochemical reactions to deposit material onto a substrate. The choice between PVD and ECD depends on factors such as material properties, application requirements, and cost considerations. In many cases, they are used in combination to achieve desired results, leveraging the strengths of each method.
Key Points Explained:
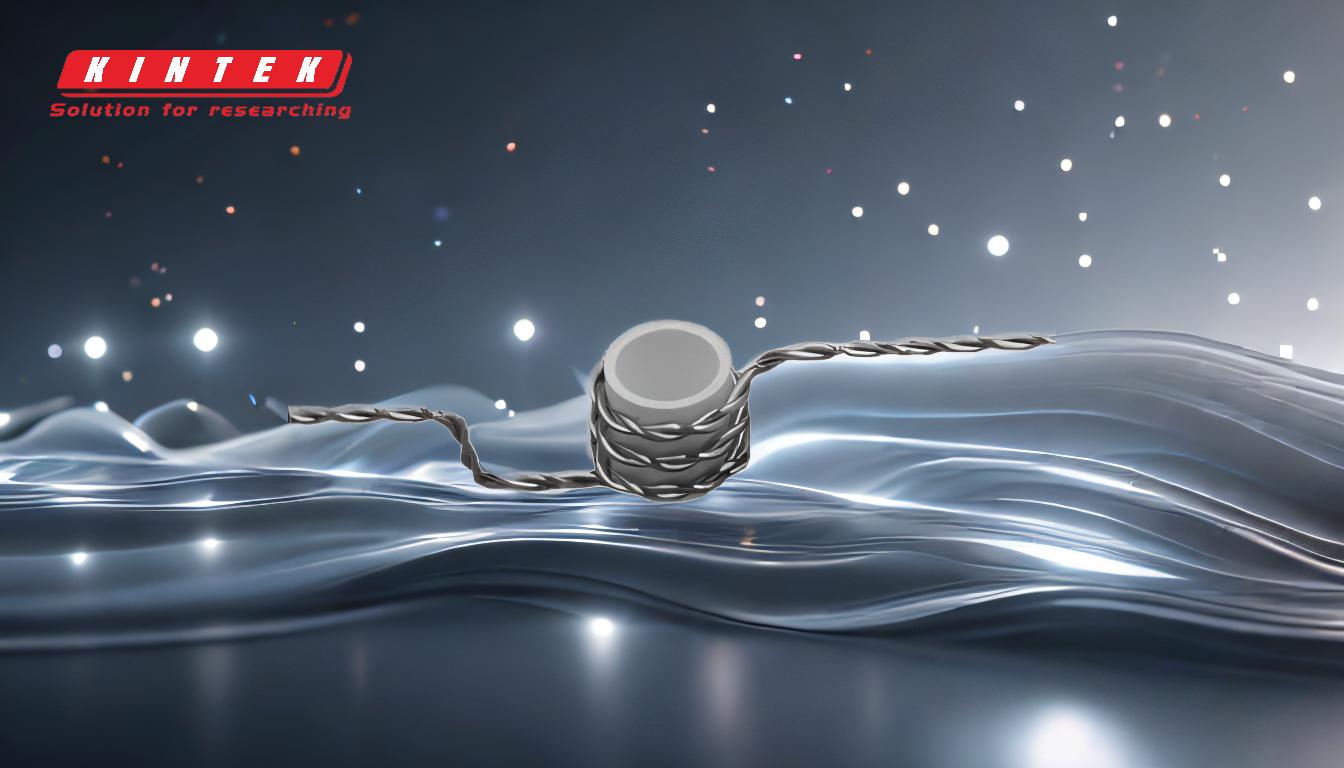
-
Fundamental Differences Between PVD and ECD:
- PVD: This process involves the physical transfer of material from a target to a substrate in a vacuum environment. Techniques include sputtering, evaporation, and ion plating. PVD is known for producing high-purity, dense, and adherent coatings.
- ECD: This process uses electrochemical reactions to deposit material onto a substrate. It involves the use of an electrolyte and an electrochemical electrode to facilitate the deposition. ECD is often used for its ability to deposit metals and alloys with precise control over thickness and composition.
-
Application Areas:
- PVD: Commonly used in applications requiring high-performance coatings, such as wear-resistant coatings, decorative finishes, and optical coatings. It is also widely used in the semiconductor industry for depositing thin films on wafers.
- ECD: Primarily used in applications where precise control over material properties is required, such as in the production of printed circuit boards (PCBs), microelectromechanical systems (MEMS), and metal plating for corrosion protection.
-
Complementary Nature:
- Material Compatibility: PVD is better suited for depositing materials that are difficult to electroplate, such as refractory metals and ceramics. ECD, on the other hand, excels in depositing metals and alloys with high conductivity and ductility.
- Process Integration: In some cases, PVD and ECD are used sequentially to achieve desired properties. For example, a PVD layer might be used as a seed layer for subsequent ECD deposition, or an ECD layer might be used to fill vias and trenches in semiconductor devices.
-
Cost and Scalability:
- PVD: Generally more expensive due to the need for vacuum equipment and high-energy processes. However, it offers superior control over film properties and is scalable for high-volume production.
- ECD: Typically more cost-effective, especially for large-scale production. It is also easier to scale for high-throughput applications, making it a preferred choice for industries like electronics and automotive.
-
Environmental and Safety Considerations:
- PVD: Involves the use of hazardous materials and requires stringent safety measures. However, it produces minimal waste and is considered environmentally friendly compared to some other deposition methods.
- ECD: Involves the use of chemical baths and can generate hazardous waste. Proper waste management and safety protocols are essential to minimize environmental impact.
-
Future Trends:
- Hybrid Processes: There is a growing trend towards combining PVD and ECD in hybrid processes to leverage the strengths of both methods. For example, PVD can be used to deposit a thin seed layer, followed by ECD to achieve the desired thickness and properties.
- Advanced Materials: Both PVD and ECD are being adapted to deposit advanced materials, such as 2D materials and nanocomposites, for next-generation applications in electronics, energy storage, and biomedical devices.
In conclusion, PVD and ECD are not direct competitors but rather complementary technologies that can be used in combination to achieve specific material properties and application requirements. The choice between them depends on factors such as material compatibility, cost, scalability, and environmental considerations. As technology advances, we can expect to see more hybrid processes that integrate the strengths of both PVD and ECD to meet the demands of emerging applications.
Summary Table:
Aspect | PVD | ECD |
---|---|---|
Process | Physical transfer in a vacuum environment | Electrochemical reactions using an electrolyte |
Applications | High-performance coatings, semiconductors, optics | PCBs, MEMS, corrosion protection |
Material Suitability | Refractory metals, ceramics | Metals, alloys with high conductivity |
Cost | Higher due to vacuum equipment and high-energy processes | More cost-effective, especially for large-scale production |
Environmental Impact | Minimal waste, environmentally friendly | Requires proper waste management due to chemical baths |
Future Trends | Hybrid processes, advanced materials (e.g., 2D materials, nanocomposites) | Hybrid processes, advanced materials for next-gen applications |
Ready to optimize your thin-film deposition process? Contact our experts today to learn how PVD and ECD can work together for your needs!