PVD (Physical Vapor Deposition) coating is generally considered superior to traditional electroplating in terms of durability, wear resistance, environmental safety, and longevity. PVD coatings are harder, more resistant to wear and tear, and do not require a clear top coat, making them less prone to tarnishing, fading, and corrosion. They are also environmentally friendly, as they do not release harmful chemicals. While PVD is more expensive, its advantages make it the preferred choice for applications requiring high durability and resistance to harsh conditions, such as in aerospace, medical, and marine industries.
Key Points Explained:
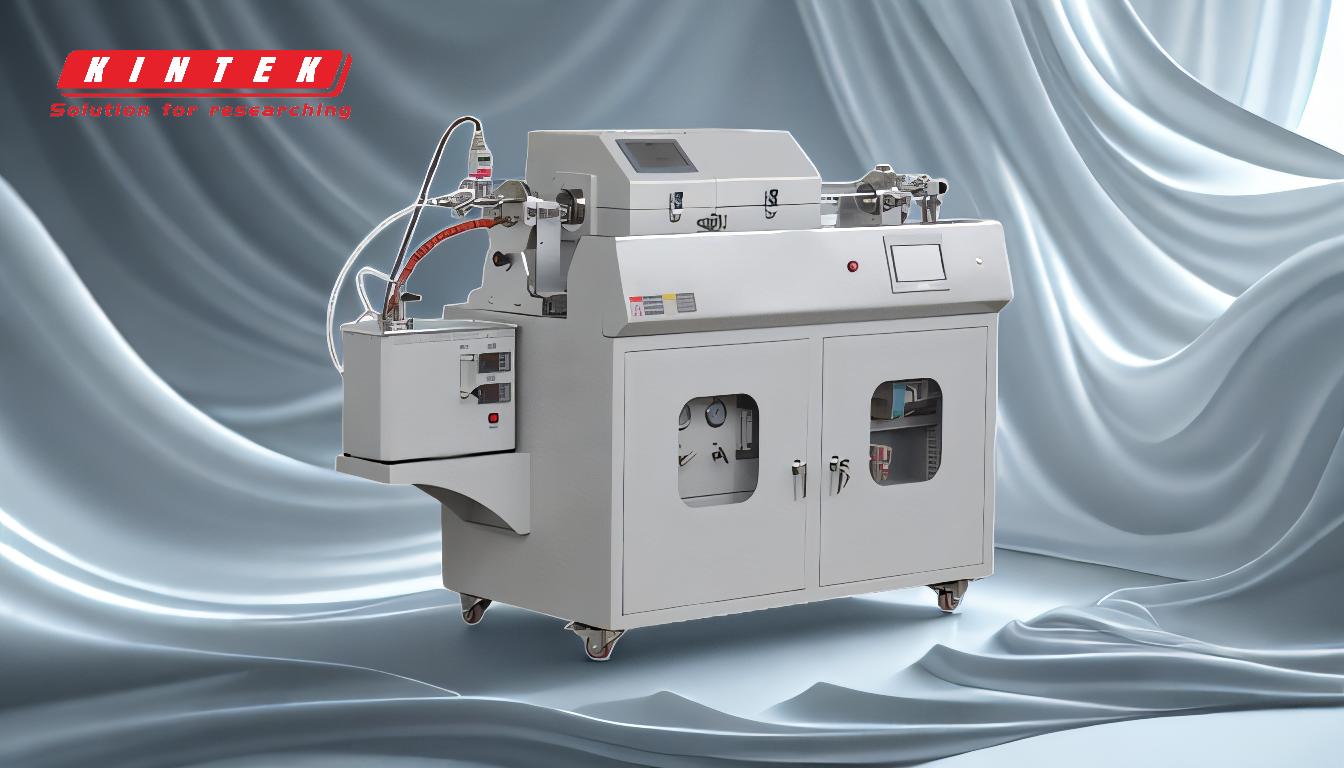
-
Durability and Longevity:
- PVD: PVD-coated products are highly durable and can last significantly longer than electroplated ones. For example, PVD-coated jewelry can last 3 years or more with everyday wear, compared to electroplated jewelry, which typically lasts about 1 year.
- Electroplating: Electroplated finishes often require a clear coat that degrades over time, leading to tarnishing, fading, and corrosion. This makes them less durable in the long run.
-
Wear and Tear Resistance:
- PVD: PVD coatings are harder and more resistant to abrasion, impact, and wear. This makes them ideal for applications where the material is subjected to frequent use or harsh conditions, such as cutting tools and marine environments.
- Electroplating: Electroplated coatings are generally softer and less resistant to wear and tear, making them less suitable for high-stress applications.
-
Environmental Safety:
- PVD: PVD is an environmentally friendly process that does not release harmful chemicals into the atmosphere. This makes it a safer choice for both manufacturers and end-users.
- Electroplating: Traditional electroplating processes often involve the use of hazardous chemicals, which can be harmful to the environment and human health.
-
Resistance to Corrosion and Tarnishing:
- PVD: PVD coatings are highly resistant to corrosion, tarnishing, and discoloration. They also maintain their properties under UV radiation, making them suitable for outdoor and marine applications.
- Electroplating: Electroplated finishes are more prone to tarnishing and corrosion, especially when the protective clear coat degrades over time.
-
Temperature Resistance:
- PVD: PVD films can withstand high temperatures, making them suitable for applications that involve exposure to heat.
- Electroplating: Electroplated coatings may not perform as well under high-temperature conditions, limiting their use in certain applications.
-
Cost and Application Suitability:
- PVD: While PVD is generally more expensive than electroplating, its superior properties make it the optimal choice for specific applications where durability, wear resistance, and environmental safety are critical.
- Electroplating: Electroplating is often chosen for its lower cost and suitability for less demanding applications, but it may not provide the same level of performance as PVD in more rigorous environments.
In summary, PVD coating offers significant advantages over traditional electroplating in terms of durability, wear resistance, environmental safety, and longevity. While it may be more expensive, its benefits make it the preferred choice for high-performance applications in industries such as aerospace, medical, and marine.
Summary Table:
Feature | PVD Coating | Electroplating |
---|---|---|
Durability & Longevity | Lasts 3+ years (e.g., jewelry) | Lasts ~1 year, prone to degradation |
Wear Resistance | Harder, resists abrasion and impact | Softer, less resistant to wear |
Environmental Safety | No harmful chemicals released | Uses hazardous chemicals |
Corrosion Resistance | Highly resistant to tarnishing | Prone to tarnishing and corrosion |
Temperature Resistance | Withstands high temperatures | Limited performance under heat |
Cost | Higher cost, better for high-demand | Lower cost, suitable for less-demand |
Upgrade your materials with PVD coating—contact our experts today for a tailored solution!