PVD (Physical Vapor Deposition) coating is widely regarded as an eco-friendly process due to its minimal environmental impact. Unlike traditional coating methods such as electroplating or painting, PVD operates in a vacuum environment, eliminating the release of harmful chemicals or pollutants into the atmosphere. The process uses environmentally safe materials like Chromium Nitride (CrN) and Titanium Nitride, which are non-toxic and durable. Additionally, PVD coatings produce no waste, do not alter the recyclability of materials like stainless steel, and reduce the need for frequent replacements, further contributing to sustainability. Its application in industries such as medical implants highlights its purity and environmental safety.
Key Points Explained:
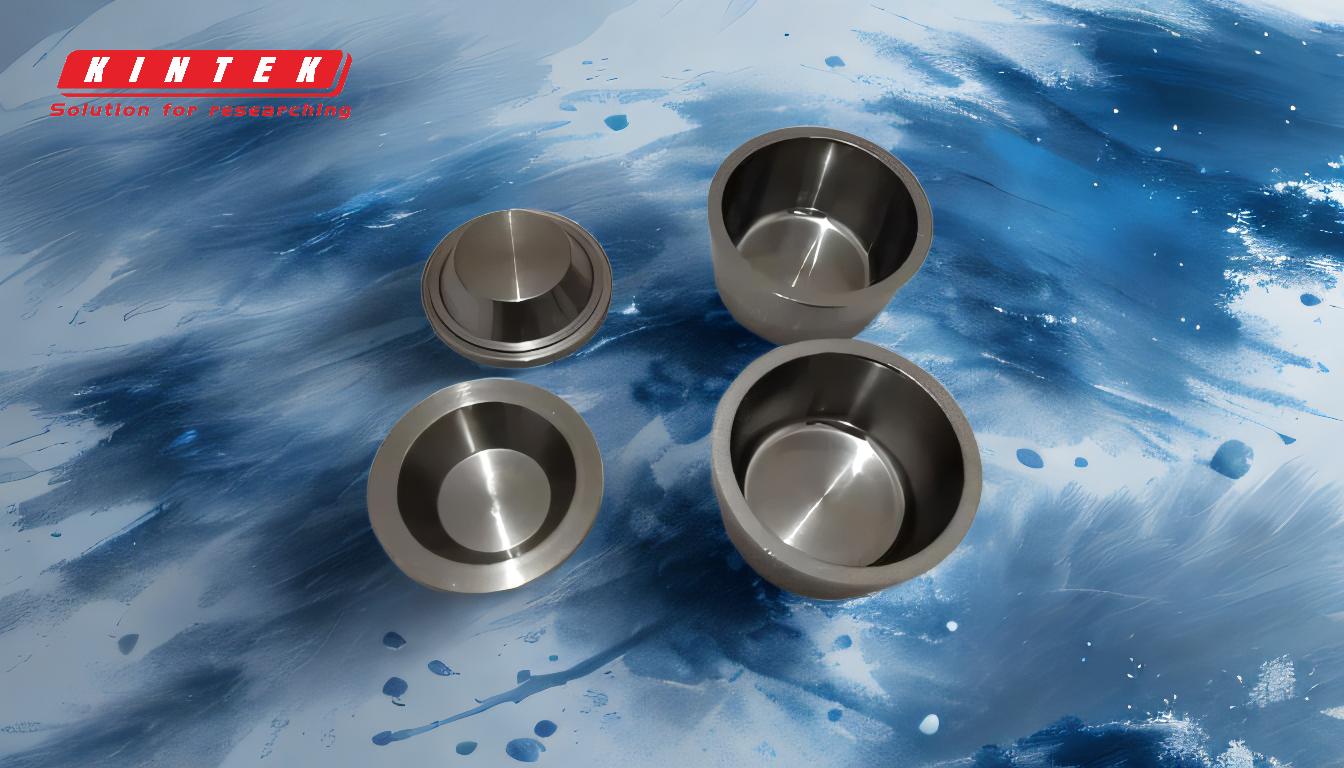
-
Vacuum-Based Process Minimizes Harmful Emissions:
- PVD coating is performed in a vacuum environment, which prevents the release of harmful chemicals or pollutants into the atmosphere. This contrasts with traditional "wet" processes like electroplating, which often involve toxic substances and generate hazardous waste.
- The vacuum-based nature of PVD ensures that the process is clean and free from environmental contamination, making it a preferred choice for industries prioritizing eco-friendliness.
-
Use of Environmentally Safe Materials:
- PVD coatings utilize materials such as Chromium Nitride (CrN) and Titanium Nitride, which are non-toxic and environmentally safe. These materials are durable and provide long-lasting protection, reducing the need for frequent recoating or replacements.
- The absence of harmful chemicals in the coating materials further enhances the eco-friendliness of the process.
-
No Waste Generation:
- Unlike other coating methods, PVD does not produce waste or gases during the process. This makes it a zero-waste technology, aligning with sustainable manufacturing practices.
- The lack of waste generation also simplifies disposal and reduces the environmental footprint of the coating process.
-
Preservation of Recyclability:
- PVD coatings do not alter the recyclable value of materials like stainless steel. This means that coated products can still be recycled at the end of their lifecycle without losing their intrinsic value.
- The ability to maintain recyclability contributes to a circular economy, reducing the demand for new raw materials and minimizing environmental impact.
-
Durable and Long-Lasting Coatings:
- PVD coatings are known for their durability and resistance to wear and corrosion. This longevity reduces the need for frequent replacements or repairs, which in turn decreases resource consumption and waste generation over time.
- The long-lasting nature of PVD coatings makes them a sustainable choice for industries seeking to minimize their environmental footprint.
-
Preferred in Medical and Surgical Applications:
- PVD is widely used in the medical and surgical implant industry due to its ability to produce extremely pure, clean, and durable coatings. This application highlights the process's safety and environmental compatibility.
- The use of PVD in such critical industries underscores its eco-friendliness and reliability.
-
Reduction of Toxic Substances:
- Compared to traditional coating methods, PVD significantly reduces the use of toxic substances. This reduction in hazardous materials makes the process safer for both the environment and workers.
- The elimination of toxic substances aligns with global efforts to adopt cleaner and greener manufacturing technologies.
In conclusion, PVD coating stands out as an eco-friendly solution due to its vacuum-based process, use of safe materials, zero waste generation, preservation of recyclability, and long-lasting durability. Its application in industries like medical implants further validates its environmental safety and sustainability. For purchasers of equipment and consumables, PVD coatings offer a reliable and environmentally responsible choice that aligns with modern sustainability goals.
Summary Table:
Key Benefits of PVD Coating | Details |
---|---|
Vacuum-Based Process | Eliminates harmful emissions, ensuring a clean and eco-friendly process. |
Environmentally Safe Materials | Uses non-toxic materials like Chromium Nitride (CrN) and Titanium Nitride. |
Zero Waste Generation | Produces no waste or gases, aligning with sustainable manufacturing. |
Preserves Recyclability | Does not alter the recyclable value of materials like stainless steel. |
Durable and Long-Lasting | Reduces the need for frequent replacements, minimizing resource consumption. |
Medical and Surgical Applications | Ensures purity and safety for critical industries like medical implants. |
Reduction of Toxic Substances | Eliminates hazardous materials, making it safer for the environment. |
Ready to adopt eco-friendly PVD coatings for your business? Contact us today to learn more!