Chemical Vapor Deposition (CVD) is a versatile and widely used technique for depositing thin films of materials, particularly in the semiconductor industry. While vacuum conditions are often associated with CVD, they are not an absolute requirement. The necessity of vacuum depends on the specific type of CVD process and the desired outcomes. For instance, Low Pressure Chemical Vapor Deposition (LPCVD) operates under reduced pressure to enhance film uniformity and purity, while other forms of CVD, such as Atmospheric Pressure Chemical Vapor Deposition (APCVD), can function at normal atmospheric pressure. The choice of pressure conditions is influenced by factors such as the type of material being deposited, the desired film properties, and the specific application.
Key Points Explained:
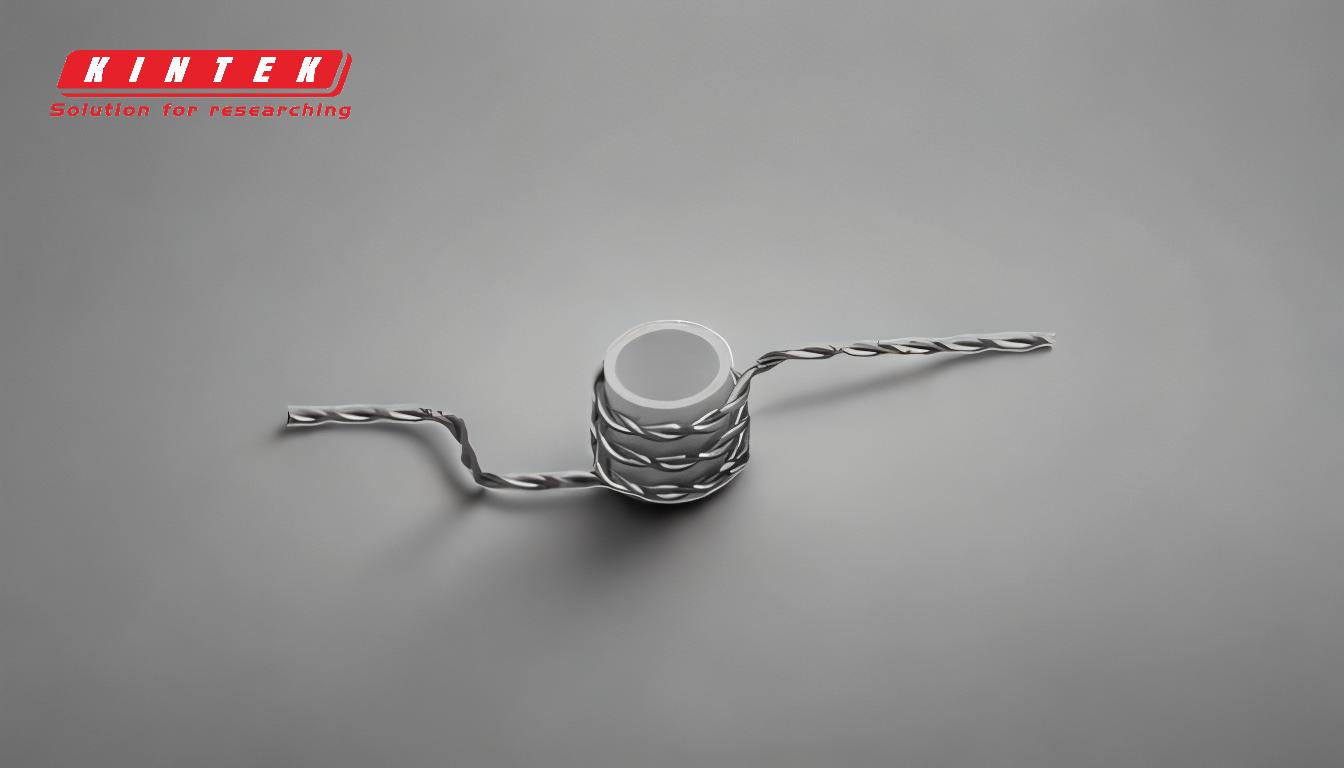
-
Vacuum in CVD: Not Always Necessary
- LPCVD (Low Pressure Chemical Vapor Deposition): This process operates at pressures below approximately 133 Pa. The reduced pressure increases the gas diffusion coefficient and mean free path, which improves film uniformity, resistivity uniformity, and trench coverage. It also allows for faster transmission of gas substances and quick removal of impurities and by-products. LPCVD is widely used in the semiconductor industry for thin film deposition and does not require carrier gas, which reduces particle pollution.
- APCVD (Atmospheric Pressure Chemical Vapor Deposition): This process operates at normal atmospheric pressure. It is simpler and less expensive than LPCVD but may not offer the same level of film uniformity and purity. APCVD is suitable for applications where high precision is not as critical.
-
Advantages of Vacuum in CVD
- Enhanced Film Quality: Vacuum conditions, as in LPCVD, can lead to higher purity films with better density, smaller residual stress, and improved crystallization. This is crucial for applications in the semiconductor industry where film quality directly impacts device performance.
- Improved Control: Vacuum environments allow for better control over the deposition process, including the timing of deposition, which can be managed by manufacturing businesses to achieve precise film thickness and properties.
-
Challenges and Considerations
- High Temperatures: CVD processes often require high temperatures (850-1100°C), which can be mitigated using plasma or laser-assisted techniques. However, some substrates cannot withstand these high temperatures, limiting the applicability of certain CVD processes.
- Toxic Chemicals: The use of toxic chemicals in CVD necessitates safe handling and disposal methods to protect workers and the environment. This adds to the complexity and cost of the process.
-
Types of CVD and Their Pressure Requirements
- Aerosol-Assisted CVD: This method uses an aerosol to make the precursor easier to handle and transport. It can operate at various pressures depending on the specific application.
- Direct Liquid Injection CVD: Involves injecting a liquid precursor into a heated chamber, where it vaporizes. This method can also operate at different pressures, including atmospheric pressure.
- Plasma-Based CVD: Uses plasma instead of heat to facilitate the deposition process. Plasma-based CVD can operate under a range of pressures, from vacuum to atmospheric, depending on the specific technique and application.
-
Applications and Material Considerations
- Semiconductor Industry: CVD is extensively used in the semiconductor industry for depositing thin films of materials such as silicon, silicon dioxide, and silicon nitride. The choice of CVD process (e.g., LPCVD, APCVD) depends on the specific requirements of the semiconductor device being manufactured.
- Other Applications: CVD is also used in other industries for applications such as creating electrical circuits, optical coatings, and protective coatings. The flexibility of CVD, due to its reliance on chemical interactions, makes it suitable for a wide range of materials and applications.
In summary, while vacuum conditions are beneficial and often used in CVD processes like LPCVD to achieve high-quality films, they are not an absolute requirement. The choice of pressure conditions in CVD depends on the specific process, material, and application requirements. Understanding these factors is crucial for selecting the appropriate CVD technique to meet the desired outcomes.
Summary Table:
Aspect | Details |
---|---|
Vacuum in CVD | Not always required; depends on the process (e.g., LPCVD vs. APCVD). |
LPCVD | Operates under reduced pressure (~133 Pa); improves film uniformity/purity. |
APCVD | Operates at atmospheric pressure; simpler and less expensive. |
Advantages of Vacuum | Enhances film quality, purity, and process control. |
Challenges | High temperatures and toxic chemicals require careful handling. |
Applications | Used in semiconductors, electrical circuits, optical coatings, and more. |
Need help selecting the right CVD process for your application? Contact our experts today!