Vacuum casting and centrifugal casting are two distinct methods used in manufacturing, each with its own advantages and limitations. Vacuum casting is particularly valued for its ability to produce high-quality, clean castings with minimal impurities, making it ideal for industries like aerospace and nuclear where material integrity is critical. Centrifugal casting, on the other hand, is known for its efficiency in producing cylindrical components with excellent mechanical properties. The choice between the two methods depends on the specific requirements of the application, including material properties, component geometry, and production volume.
Key Points Explained:
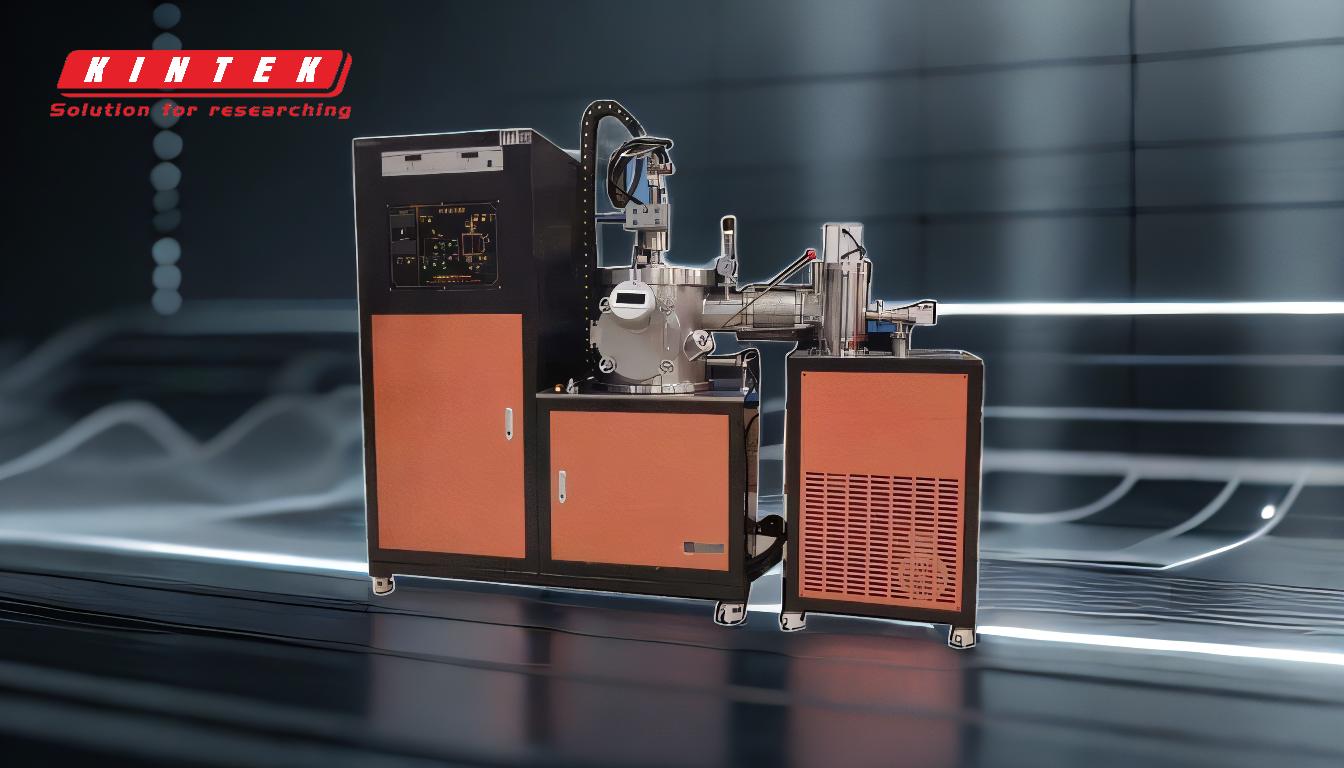
-
Material Cleanliness and Quality:
- Vacuum Casting: This method is renowned for producing castings with high levels of cleanliness. The vacuum environment prevents oxidation and contamination, resulting in superior material properties. This is particularly important in industries like aerospace and nuclear, where even minor impurities can compromise the integrity of the components.
- Centrifugal Casting: While centrifugal casting can also produce high-quality castings, it may not achieve the same level of cleanliness as vacuum casting. The process relies on centrifugal force to distribute the molten metal, which can sometimes lead to inclusions or impurities being trapped in the casting.
-
Application Suitability:
- Vacuum Casting: Ideal for applications requiring high-purity materials and complex geometries. It is commonly used in the aerospace, nuclear, and medical industries where material integrity is paramount.
- Centrifugal Casting: Best suited for producing cylindrical or symmetrical components such as pipes, tubes, and rings. It is widely used in the automotive, marine, and industrial sectors.
-
Mechanical Properties:
- Vacuum Casting: The controlled environment of vacuum casting allows for precise control over the cooling rate, which can enhance the mechanical properties of the castings. This results in components with superior strength, ductility, and fatigue resistance.
- Centrifugal Casting: The centrifugal force used in this method helps to produce castings with a dense, fine-grained structure, which can improve mechanical properties like tensile strength and wear resistance. However, the mechanical properties may not be as uniform as those achieved with vacuum casting.
-
Production Volume and Cost:
- Vacuum Casting: Generally more expensive due to the need for specialized equipment and controlled environments. It is typically used for low to medium production volumes where the cost is justified by the need for high-quality castings.
- Centrifugal Casting: More cost-effective for high-volume production runs, especially for components with simple geometries. The process is relatively simple and does not require the same level of environmental control as vacuum casting.
-
Complexity and Flexibility:
- Vacuum Casting: Offers greater flexibility in terms of the complexity of the components that can be produced. It can handle intricate designs and thin-walled sections with ease.
- Centrifugal Casting: Limited to simpler, symmetrical shapes. While it is excellent for producing uniform, cylindrical components, it may not be suitable for more complex geometries.
In conclusion, the choice between vacuum casting and centrifugal casting depends on the specific requirements of the application. Vacuum casting is superior for high-purity, complex components, while centrifugal casting is more cost-effective for high-volume, simple geometries. Each method has its own strengths and limitations, and the decision should be based on a thorough evaluation of the material properties, component design, and production needs.
Summary Table:
Aspect | Vacuum Casting | Centrifugal Casting |
---|---|---|
Material Cleanliness | High cleanliness, minimal impurities, ideal for aerospace and nuclear industries. | Good quality, but may have inclusions due to centrifugal force. |
Application Suitability | Best for high-purity, complex geometries (aerospace, medical). | Ideal for cylindrical components (pipes, tubes, rings). |
Mechanical Properties | Superior strength, ductility, and fatigue resistance. | Dense, fine-grained structure; good tensile strength and wear resistance. |
Production Volume & Cost | Expensive, suited for low to medium volumes. | Cost-effective for high-volume production. |
Complexity & Flexibility | Handles intricate designs and thin-walled sections. | Limited to simpler, symmetrical shapes. |
Need help choosing the right casting method for your project? Contact our experts today for personalized advice!