Vacuum hardening is generally considered superior to normal hardening due to its ability to enhance the mechanical properties of metal components while minimizing surface contamination and distortion. This process operates in a controlled environment, preventing oxidation and ensuring higher purity and surface fineness. It also offers better temperature uniformity, consistent results, and reduced energy consumption. These advantages make vacuum hardening particularly suitable for applications requiring precision, durability, and high-quality finishes.
Key Points Explained:
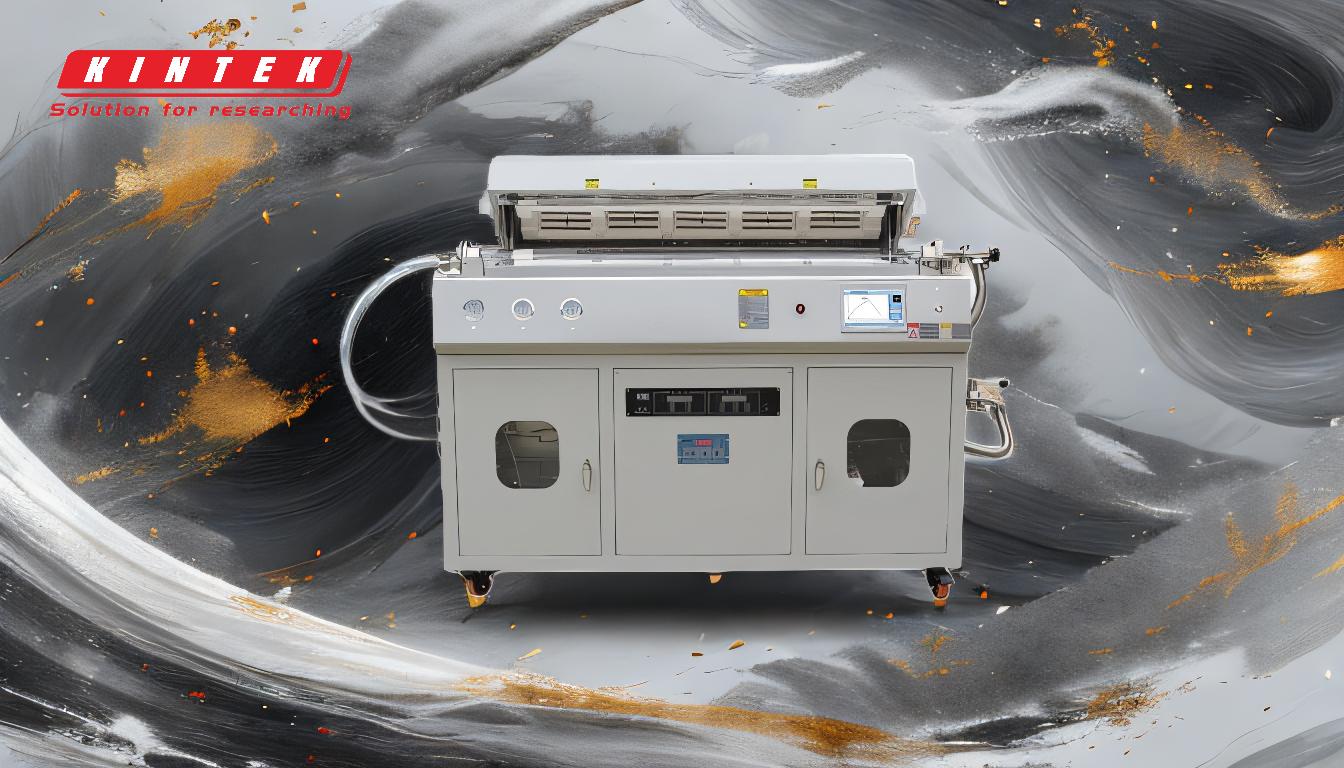
-
Enhanced Mechanical Properties:
- Vacuum hardening significantly improves the strength, toughness, and wear resistance of metal components. The controlled environment ensures that the material achieves optimal hardness without compromising its structural integrity. This is particularly beneficial for components subjected to high stress or demanding operational conditions.
-
Minimized Surface Contamination:
- Unlike normal hardening, which often exposes materials to atmospheric gases, vacuum hardening takes place in a vacuum environment. This eliminates oxidation and contamination, resulting in a cleaner and more refined surface finish. The absence of oxidation also prevents scaling and decarburization, which are common issues in traditional hardening methods.
-
Reduced Distortion:
- The uniform heating and cooling processes in a vacuum hardening furnace minimize thermal stress and distortion. This ensures that the final product retains its dimensional accuracy and geometric precision, which is critical for high-tolerance applications.
-
Better Temperature Uniformity:
- Vacuum hardening provides superior temperature control, ensuring even heat distribution throughout the component. This uniformity is crucial for achieving consistent mechanical properties across the entire part, reducing the risk of weak spots or uneven hardness.
-
Energy Efficiency:
- The vacuum environment reduces heat loss and improves thermal efficiency, leading to lower energy consumption compared to normal hardening processes. This makes vacuum hardening a more sustainable and cost-effective option in the long run.
-
Consistent and Repeatable Results:
- The precise control over process parameters in vacuum hardening ensures consistent outcomes. This repeatability is essential for industries requiring high-quality standards, such as aerospace, automotive, and medical device manufacturing.
-
Applications and Suitability:
- Vacuum hardening is particularly advantageous for high-performance alloys, tool steels, and components requiring exceptional surface finish and durability. It is widely used in industries where precision, reliability, and longevity are paramount.
In summary, vacuum hardening outperforms normal hardening in terms of quality, precision, and efficiency. Its ability to deliver superior mechanical properties, minimize contamination, and reduce distortion makes it the preferred choice for high-end applications. The use of a vacuum hardening furnace ensures that the process is both effective and sustainable, aligning with modern manufacturing demands.
Summary Table:
Aspect | Vacuum Hardening | Normal Hardening |
---|---|---|
Mechanical Properties | Enhanced strength, toughness, and wear resistance | Limited improvement in mechanical properties |
Surface Contamination | Minimal oxidation and contamination | High risk of oxidation and scaling |
Distortion | Reduced thermal stress and distortion | Higher risk of distortion |
Temperature Uniformity | Superior heat distribution and control | Less uniform heating |
Energy Efficiency | Lower energy consumption | Higher energy usage |
Consistency | Repeatable and consistent results | Variable outcomes |
Applications | Ideal for high-performance alloys and precision | Suitable for less demanding applications |
Upgrade your hardening process with vacuum technology—contact us today to learn more!