Magnetron sputtering is a physical vapor deposition (PVD) technique used to deposit thin films onto substrates. It operates on the principle of bombarding a target material with high-energy ions in a vacuum chamber, causing atoms from the target surface to be ejected (sputtered) and deposited onto a substrate. A magnetic field is applied to control the movement of electrons and ions, enhancing the efficiency of the process by increasing ionization and sustaining a stable plasma. This method is widely used for creating high-quality coatings due to its ability to produce dense, uniform films with precise control over thickness and composition.
Key Points Explained:
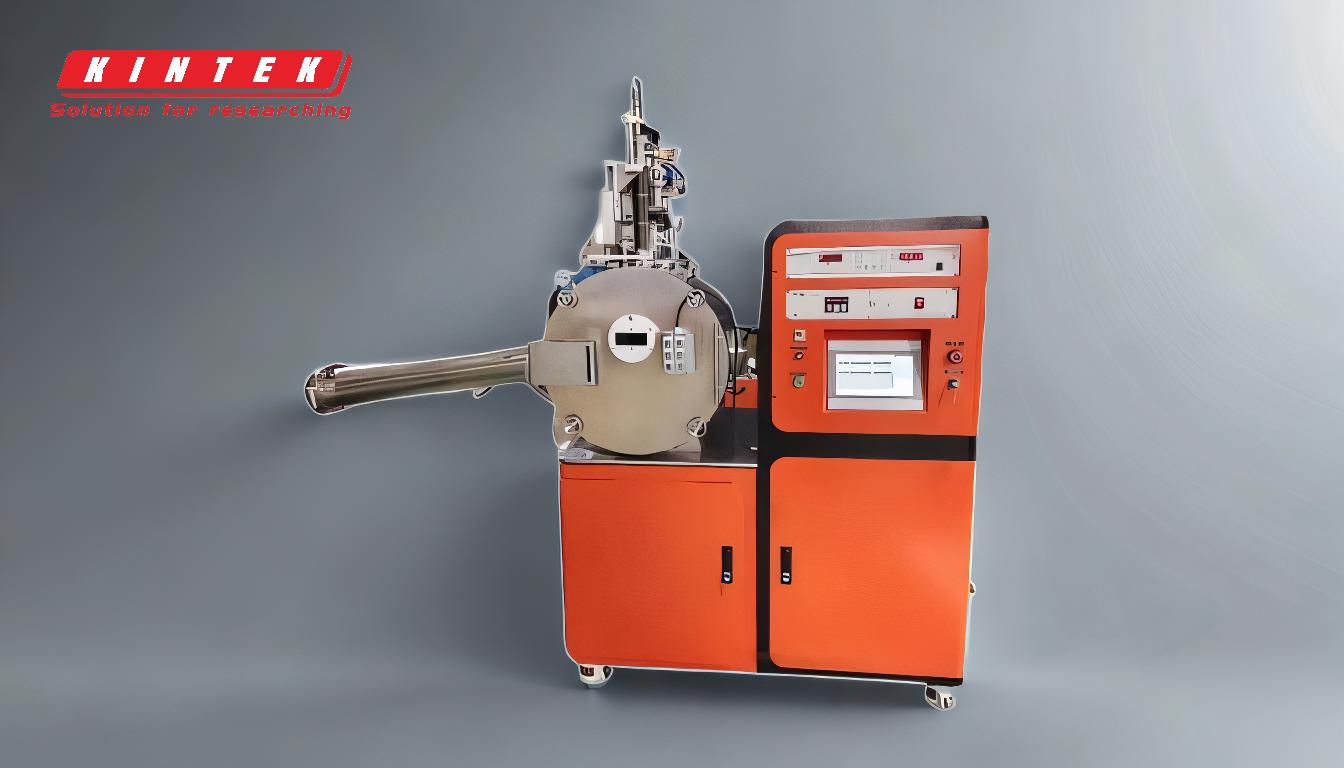
-
Basic Principle of Sputtering:
- Sputtering occurs when high-energy ions collide with the surface of a target material, transferring energy to the target atoms.
- If the energy transferred is sufficient, target atoms are ejected from the surface and travel through the vacuum chamber.
- These ejected atoms then deposit onto a substrate, forming a thin film.
-
Role of the Magnetic Field:
- A magnetic field is applied near the target surface to confine electrons in a cycloidal (spiral) motion.
- This confinement increases the residence time of electrons in the plasma, enhancing their likelihood of colliding with gas atoms (typically argon).
- These collisions ionize the gas atoms, creating a higher density of positive ions available for sputtering.
-
Generation of Plasma:
- The process begins by applying a negative voltage to the target material, which attracts positive ions from the plasma.
- The bombardment of these ions on the target surface generates a stable plasma with high ion density.
- The plasma is sustained by the continuous ionization of gas atoms due to electron collisions.
-
Energy Transfer and Sputtering Efficiency:
- The kinetic energy of the ions is transferred to the target atoms upon impact.
- If the energy exceeds the binding energy of the target atoms, they are ejected from the surface.
- The magnetic field enhances the efficiency of this process by increasing the ionization rate and ensuring a steady supply of ions.
-
Advantages of Magnetron Sputtering:
- High-quality, dense, and uniform coatings can be achieved due to the controlled and sustained plasma environment.
- The process allows for precise control over film thickness and composition, making it suitable for applications requiring high precision.
- It is versatile and can be used with a wide range of target materials, including metals, alloys, and ceramics.
-
Applications:
- Magnetron sputtering is widely used in industries such as semiconductors, optics, and decorative coatings.
- It is particularly valued for producing thin films in microelectronics, solar cells, and wear-resistant coatings.
By combining the principles of ion bombardment, magnetic field confinement, and plasma generation, magnetron sputtering provides a highly efficient and controllable method for depositing thin films. This makes it a cornerstone technology in modern materials science and engineering.
Summary Table:
Key Aspect | Description |
---|---|
Basic Principle | High-energy ions bombard a target, ejecting atoms that deposit onto a substrate. |
Magnetic Field Role | Confines electrons, increasing ionization and sustaining a stable plasma. |
Plasma Generation | Negative voltage attracts ions, creating high-density plasma for sputtering. |
Advantages | Dense, uniform coatings with precise control over thickness and composition. |
Applications | Semiconductors, optics, solar cells, and wear-resistant coatings. |
Discover how magnetron sputtering can enhance your projects—contact our experts today!