Pyrolysis is a thermal decomposition process that requires specialized apparatus to efficiently convert materials into useful products like biochar, syngas, and bio-oil. The core component of any pyrolysis setup is the pyrolysis reactor, which is designed to operate under high temperatures and controlled environments to ensure optimal thermal decomposition. The reactor is often complemented by auxiliary systems such as feeding mechanisms, gas recycling units, and de-dusting systems to ensure seamless operation and compliance with environmental standards. Various types of reactors, such as fluidized bed reactors, auger reactors, and Heinz retort reactors, are used depending on the specific application and material being processed. The choice of materials for constructing these reactors, such as Q245R, Q345R boiler plates, or stainless steel, ensures durability and resistance to high temperatures and corrosive environments.
Key Points Explained:
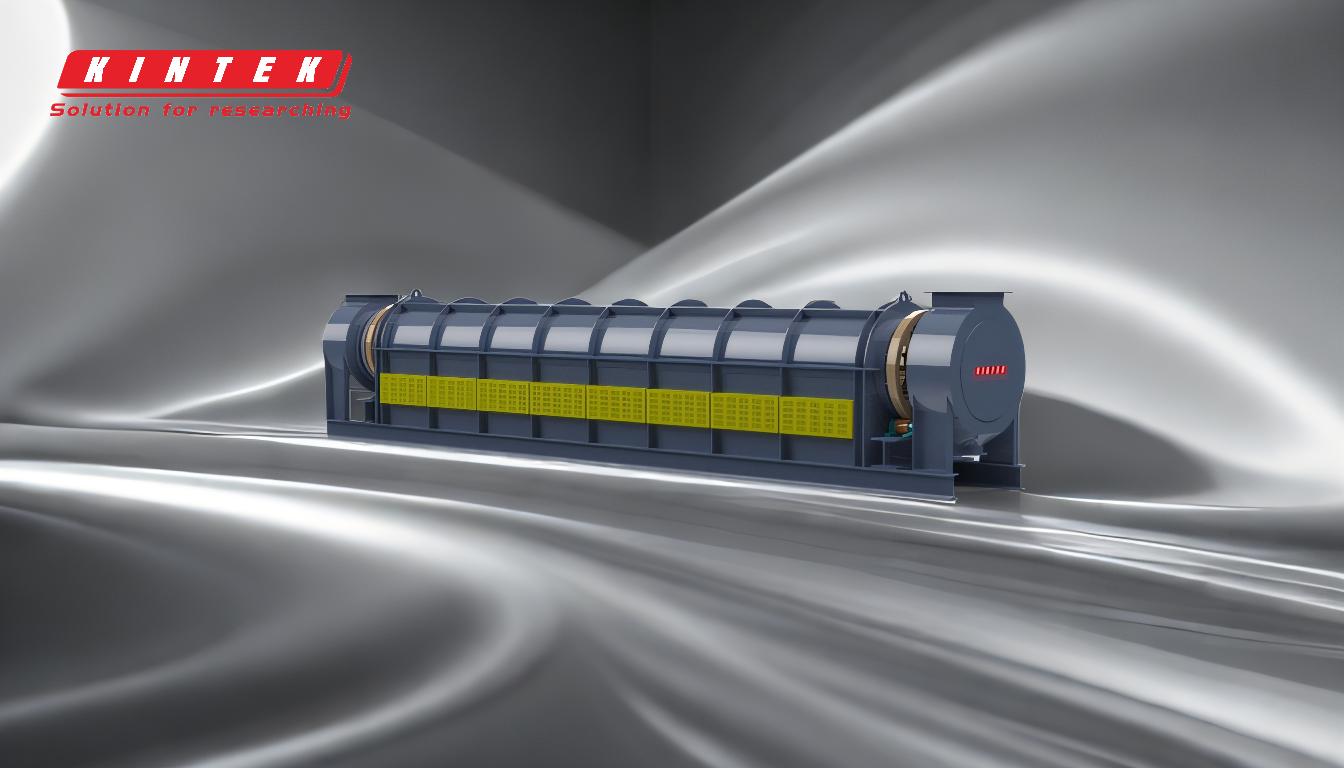
-
Pyrolysis Reactor as the Core Apparatus:
- The pyrolysis reactor is the central component where thermal decomposition occurs. It is designed to withstand high temperatures and often operates under low-oxygen or oxygen-free conditions to prevent combustion.
- Different reactor designs, such as fluidized bed reactors, auger reactors, and Heinz retort reactors, are used depending on the application. For example, a fluidized bed reactor separates waste flows into zones with varying oxygen concentrations, while an auger reactor uses a screw mechanism to move materials through the reactor.
-
Types of Pyrolysis Reactors:
- Fluidized Bed Reactor: This reactor uses a sand mass in the "bed section" for drying, pyrolysis, and gasification under low oxygen conditions. The "free section" introduces additional air for further combustion, ensuring a gas retention period of at least 2 seconds at 825°C or higher.
- Auger Reactor: This reactor employs a screw mechanism driven by a variable-speed motor to transport materials through the hot zone. It relies on mechanical force and pressure for heat transfer, making it distinct from fluidized or circulatory reactors.
- Heinz Retort Reactor: This is a simple airtight vessel that uses external heat to thermally decompose materials. Heat transfer occurs through the vessel walls, making it one of the most straightforward reactor designs.
-
Materials Used in Reactor Construction:
- Pyrolysis reactors are typically constructed from durable materials like Q245R and Q345R boiler plates or 304 and 306 stainless steel. These materials are chosen for their ability to withstand high temperatures and resist corrosion, ensuring long-term operational efficiency.
-
Auxiliary Systems in a Pyrolysis Setup:
- Feeding System: Automatically delivers raw materials to the reactor in a fully sealed manner, ensuring consistent feedstock supply.
- Discharging System: Transports byproducts like carbon black into a cooling tank, often equipped with water-cooling pipes.
- Syn-gas Recycling System: Captures and recycles combustible gases produced during pyrolysis, which can be reused to heat the reactor, improving energy efficiency.
- De-dusting System: Purifies emission gases to meet stringent environmental standards, such as EU emission regulations.
-
Components of a Pyrolysis Reactor System:
- The reactor system typically includes four main parts:
- Driving Device: Powers the reactor's mechanical components.
- Base: Provides structural support for the reactor.
- Main Furnace: Houses the pyrolysis process.
- Casing: Encases the reactor, ensuring safety and thermal insulation.
- The reactor system typically includes four main parts:
-
Applications and Benefits:
- Pyrolysis reactors are used in various industries, including waste management, energy production, and chemical manufacturing. They enable the conversion of waste materials into valuable products, reducing environmental impact and promoting sustainability.
By understanding the key components and types of pyrolysis reactors, as well as the materials and auxiliary systems involved, purchasers can make informed decisions when selecting equipment for their specific needs. The choice of reactor design and materials will significantly impact the efficiency, durability, and environmental compliance of the pyrolysis process.
Summary Table:
Component | Description |
---|---|
Pyrolysis Reactor | Core apparatus for thermal decomposition under high temperatures. |
Types of Reactors | Fluidized bed, auger, and Heinz retort reactors for specific applications. |
Materials | Q245R, Q345R boiler plates, or stainless steel for durability and heat resistance. |
Auxiliary Systems | Feeding, discharging, syn-gas recycling, and de-dusting systems for efficiency. |
Applications | Waste management, energy production, and chemical manufacturing. |
Ready to optimize your pyrolysis process? Contact our experts today to find the perfect reactor setup for your needs!