Powder sintering is a critical process in powder metallurgy and ceramics manufacturing, where powdered materials are heated to high temperatures below their melting point to bond particles and create dense, high-strength components. This process involves several methods, each with unique characteristics and applications. Common sintering methods include Conventional Sintering, Spark Plasma Sintering (SPS), Microwave Sintering, Hot Isostatic Pressing (HIP), and Hot Press Sintering. These methods differ in their heating mechanisms, pressure application, and environmental conditions, such as vacuum or hydrogen protection. The choice of sintering method depends on the material properties, desired density, and mechanical performance of the final product.
Key Points Explained:
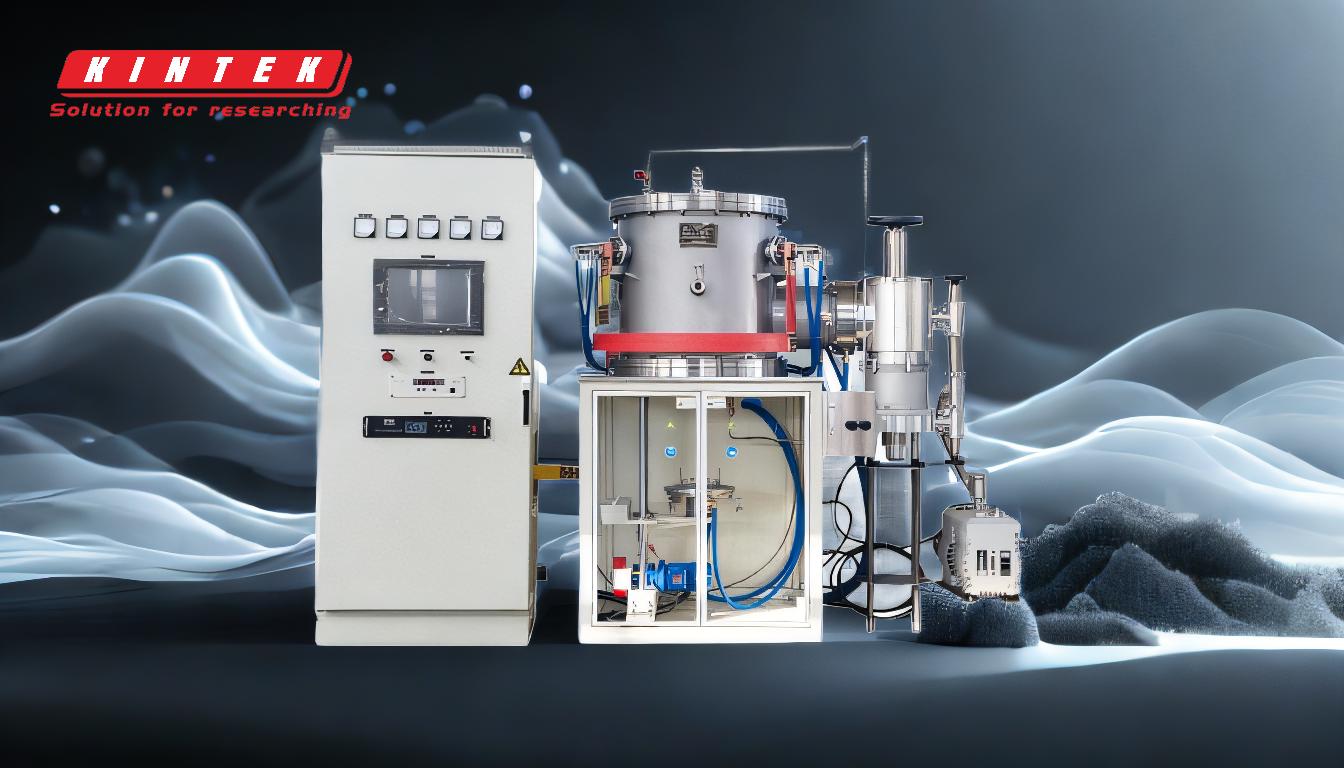
-
Conventional Sintering
- This is the most widely used sintering method, where powdered materials are heated in a furnace at temperatures below their melting point.
- The process relies on thermal energy to promote particle bonding through diffusion, reducing surface energy and closing pores.
- It is suitable for a broad range of materials, including metals and ceramics, and is cost-effective for large-scale production.
- However, it may require longer processing times and result in lower density compared to advanced sintering methods.
-
Spark Plasma Sintering (SPS)
- SPS is an advanced sintering technique that uses pulsed electric currents to generate rapid heating and sintering of powders.
- The method applies both heat and pressure simultaneously, enabling faster densification and lower sintering temperatures.
- SPS is ideal for producing high-density materials with fine microstructures and enhanced mechanical properties.
- It is particularly useful for advanced materials like ceramics, composites, and nanomaterials.
-
Microwave Sintering
- Microwave sintering utilizes electromagnetic waves to heat the powdered material directly, resulting in uniform and rapid heating.
- This method is energy-efficient and reduces processing time compared to conventional sintering.
- It is suitable for materials with high dielectric loss, such as certain ceramics and polymers.
- Microwave sintering can achieve high-density products with minimal grain growth, preserving fine microstructures.
-
Hot Isostatic Pressing (HIP)
- HIP involves applying high temperature and uniform pressure using inert gases (e.g., argon) to sinter powdered materials.
- The process eliminates internal voids and defects, producing fully dense components with superior mechanical properties.
- HIP is commonly used for critical applications in aerospace, medical implants, and high-performance alloys.
- It is particularly effective for materials that are difficult to densify using conventional methods.
-
Hot Press Sintering
- In this method, heat and uniaxial pressure are applied simultaneously to the powder compact, enhancing densification and reducing sintering time.
- Hot press sintering is suitable for materials requiring high density and controlled microstructures, such as ceramics and hard metals.
- The process is often conducted in a vacuum or protective atmosphere to prevent oxidation.
- It is widely used in the production of cutting tools, wear-resistant components, and advanced ceramics.
-
Environmental Conditions in Sintering
- Sintering can be performed under different environmental conditions, such as vacuum, hydrogen protection, or inert gas atmospheres.
- Vacuum sintering prevents oxidation and contamination, making it ideal for reactive materials like titanium and refractory metals.
- Hydrogen protection is used for materials prone to oxidation, such as stainless steels and certain ceramics.
- The choice of environment depends on the material's chemical reactivity and the desired properties of the final product.
-
Post-Sintering Treatments
- After sintering, additional treatments may be applied to improve the properties of the sintered part.
- Common post-treatments include heat treatment, surface finishing, and machining.
- Heat treatment enhances mechanical properties like hardness and toughness, while surface finishing improves wear resistance and aesthetics.
- These treatments ensure the final product meets specific performance requirements.
-
Material Considerations in Sintering
- The choice of sintering method depends on the material properties, such as melting point, reactivity, and particle size.
- Metal powders, such as copper-base and iron-base materials, are commonly sintered using conventional or advanced methods.
- Ceramic powders require precise control of sintering conditions to achieve high density and avoid cracking.
- Advanced materials, like composites and nanomaterials, often benefit from rapid sintering techniques like SPS or microwave sintering.
-
Applications of Sintering Methods
- Conventional sintering is widely used in automotive, electronics, and consumer goods industries for producing cost-effective components.
- SPS and HIP are preferred for high-performance applications in aerospace, medical devices, and energy sectors.
- Microwave sintering is gaining popularity for its energy efficiency and ability to process advanced ceramics.
- Hot press sintering is commonly used in the production of cutting tools, wear-resistant parts, and structural ceramics.
By understanding the various sintering methods and their applications, manufacturers can select the most appropriate technique to achieve the desired material properties and performance characteristics. Each method offers unique advantages, making powder sintering a versatile and essential process in modern manufacturing.
Summary Table:
Sintering Method | Key Features | Applications |
---|---|---|
Conventional Sintering | Cost-effective, thermal energy-based, suitable for metals and ceramics | Automotive, electronics, consumer goods |
Spark Plasma Sintering (SPS) | Rapid heating, high density, fine microstructures | Advanced ceramics, composites, nanomaterials |
Microwave Sintering | Energy-efficient, uniform heating, minimal grain growth | High dielectric loss materials, advanced ceramics |
Hot Isostatic Pressing (HIP) | High temperature, uniform pressure, fully dense components | Aerospace, medical implants, high-performance alloys |
Hot Press Sintering | Simultaneous heat and pressure, high density, controlled microstructures | Cutting tools, wear-resistant components, advanced ceramics |
Need help selecting the right sintering method for your materials? Contact our experts today!