Powder metallurgy (PM) is a versatile manufacturing process with numerous advantages, such as energy efficiency, cost-effectiveness, and the ability to produce complex shapes with minimal material waste. However, it also has several disadvantages that can limit its application in certain scenarios. These include size limitations, challenges in producing highly complex shapes, and lower strength and ductility compared to traditional casting or forging methods. Additionally, porosity in sintered parts can reduce their mechanical properties, and the process may not be suitable for all material combinations or end-use requirements.
Key Points Explained:
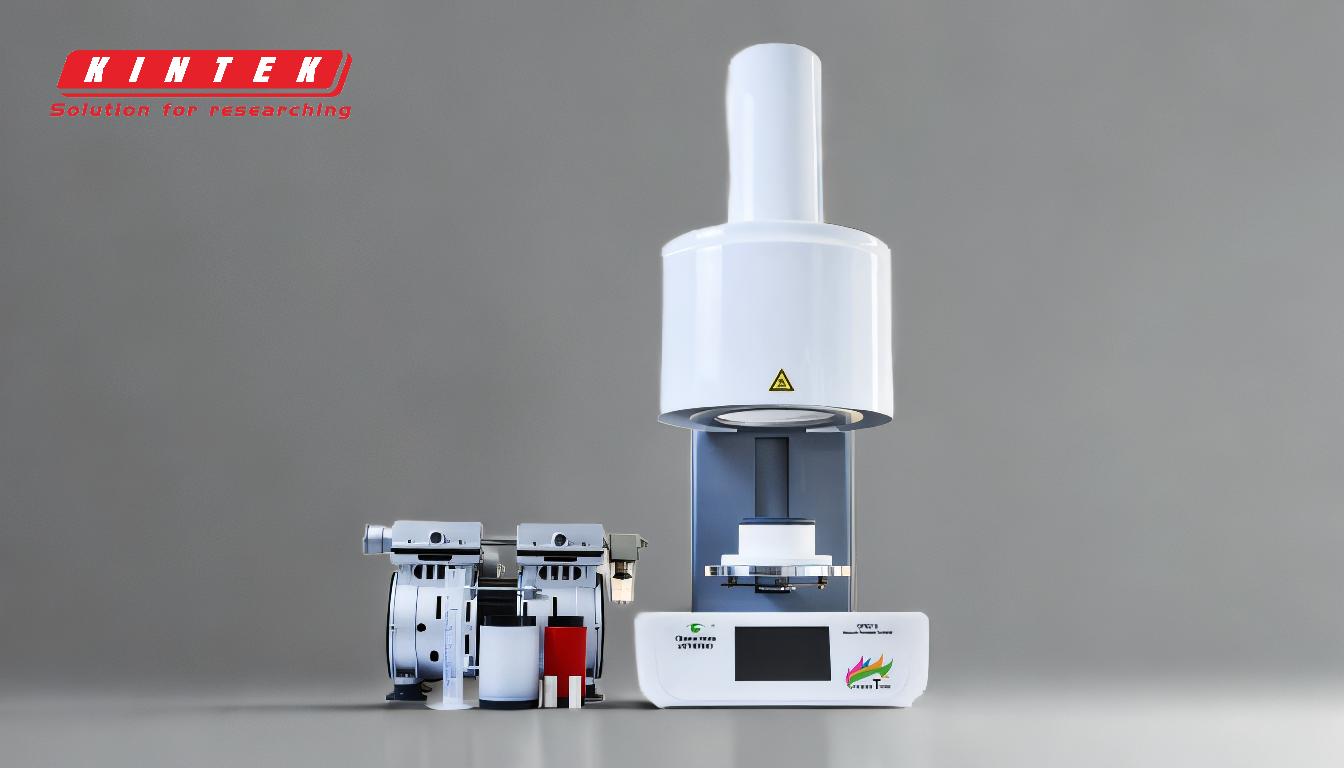
-
Size Limitations:
- Powder metallurgy is constrained by the size of the presses used in the process. The largest presses in the industry are typically around 1,500 tons, which limits the practical size of parts to approximately 40-50 square inches of planar area. This makes PM unsuitable for very large components, which may require alternative manufacturing methods like casting or forging.
-
Challenges with Complex Shapes:
- While PM can produce intricate shapes, highly complex geometries can be difficult to achieve. Skilled manufacturers can overcome some of these challenges, but the process may still struggle with parts requiring extremely fine details or unconventional geometries. This limitation can restrict the design flexibility of PM components.
-
Lower Strength and Ductility:
- Parts produced through powder metallurgy generally have lower strength and ductility compared to those made by casting or forging. This is due to the inherent porosity in sintered parts, which can compromise their mechanical properties. For applications requiring high strength or toughness, PM may not be the optimal choice.
-
Porosity and Incomplete Parts:
- The sintering process often results in porous structures, which can weaken the final product. Additionally, the pressing phase may not fully replicate the desired complexity of the end-use part, leading to incomplete or less robust components. This porosity can also affect the part's performance in high-stress environments.
-
Material Limitations:
- While PM allows for the blending of different metals and nonmetals, not all material combinations are feasible or yield the desired properties. Some materials may not compact or sinter effectively, limiting the range of applications for PM. This can be a significant drawback when specific material properties are required for a component.
-
Cost and Production Challenges:
- Although PM is generally cost-effective, the initial setup costs for molds, dies, and equipment can be high. Additionally, producing parts with very tight tolerances or unique material combinations may require specialized equipment and expertise, increasing production complexity and costs.
-
Environmental Considerations:
- While PM is considered eco-friendly due to its low material waste (97% of the material becomes part of the final product), the process may still involve energy-intensive steps like sintering. This can offset some of the environmental benefits, especially if the energy used is not from renewable sources.
In summary, while powder metallurgy offers significant advantages in terms of cost, efficiency, and material versatility, its disadvantages—such as size limitations, lower mechanical properties, and challenges with complex shapes—must be carefully considered when selecting a manufacturing process. These limitations make PM more suitable for specific applications rather than a one-size-fits-all solution.
Summary Table:
Disadvantage | Description |
---|---|
Size Limitations | Limited by press size; parts typically ≤ 40-50 sq in, making PM unsuitable for large components. |
Challenges with Complex Shapes | Difficult to achieve highly intricate geometries; restricts design flexibility. |
Lower Strength and Ductility | Parts have reduced mechanical properties compared to casting or forging. |
Porosity and Incomplete Parts | Sintering results in porous structures, weakening the final product. |
Material Limitations | Not all material combinations are feasible, limiting application versatility. |
Cost and Production Challenges | High initial setup costs and complexity for tight tolerances or unique materials. |
Environmental Considerations | Energy-intensive sintering may offset eco-friendly benefits. |
Need help deciding if powder metallurgy is right for your project? Contact our experts today for tailored advice!