Brazing is a widely used joining process that involves melting a filler metal to bond two or more materials together without melting the base materials. The four primary methods of brazing are torch brazing, furnace brazing, induction brazing, and resistance brazing. Each method has unique characteristics, applications, and advantages, making them suitable for different industrial needs. Torch brazing is versatile and portable, furnace brazing is ideal for high-volume production, induction brazing offers precision and speed, and resistance brazing is excellent for localized heating. Understanding these methods helps in selecting the right technique for specific applications.
Key Points Explained:
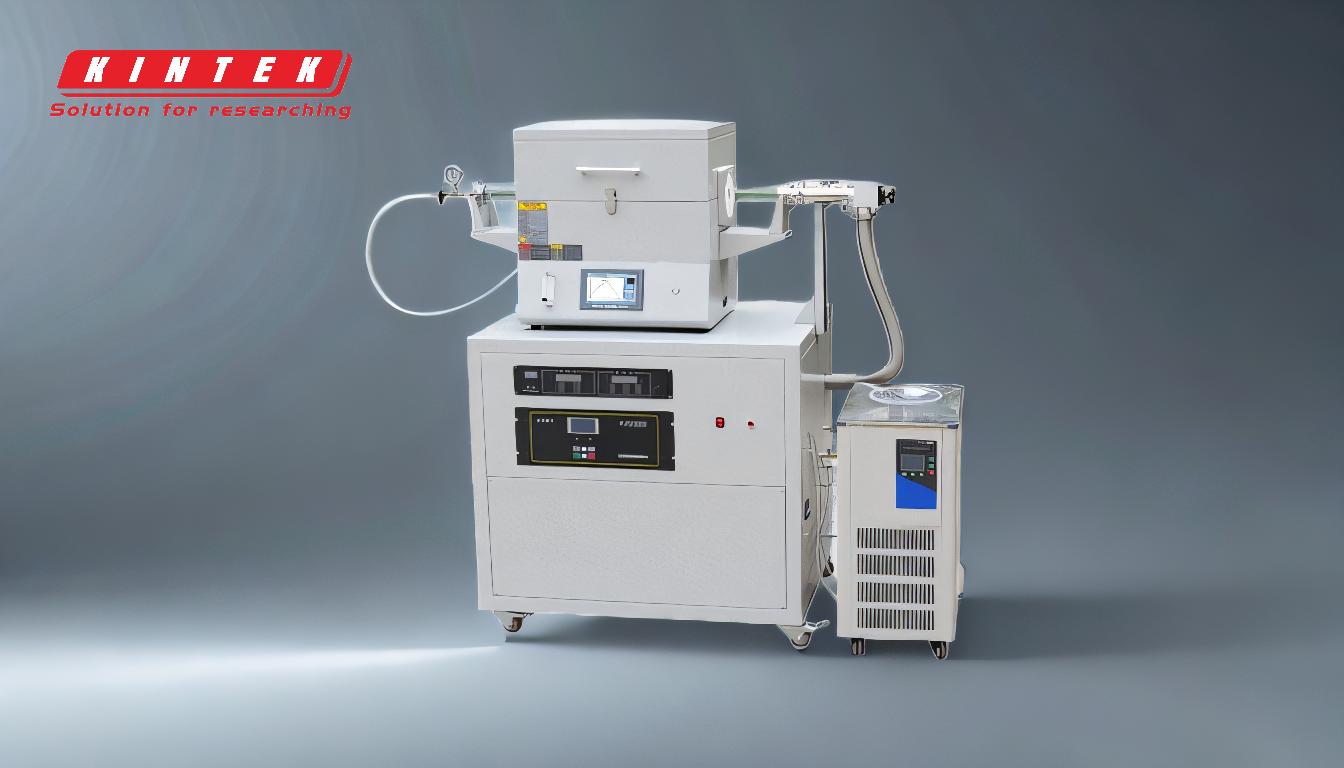
-
Torch Brazing
- Torch brazing uses a gas flame to heat the filler metal and base materials until the filler melts and flows into the joint.
- It is highly versatile and portable, making it suitable for on-site repairs and small-scale production.
- Commonly used gases include acetylene, propane, and natural gas, often mixed with oxygen or air.
- This method requires skilled operators to control the heat and ensure proper joint formation.
-
Furnace Brazing
- Furnace brazing involves placing the assembly in a furnace where controlled heating and cooling cycles are applied.
- It is ideal for high-volume production and complex assemblies due to its ability to uniformly heat multiple joints simultaneously.
- Furnaces can operate in various atmospheres, including inert gases, hydrogen, or vacuum, to prevent oxidation.
- This method is commonly used in industries like aerospace, automotive, and electronics.
-
Induction Brazing
- Induction brazing uses electromagnetic induction to generate heat directly in the workpiece, allowing for precise and localized heating.
- It is fast, energy-efficient, and suitable for high-precision applications.
- This method is often used for joining small or delicate components, such as in the medical or jewelry industries.
- Induction brazing requires specialized equipment and is typically automated for consistent results.
-
Resistance Brazing
- Resistance brazing relies on electrical resistance to generate heat at the joint interface.
- It is highly efficient for localized heating and is often used for joining electrical components or small parts.
- The process requires electrodes to apply pressure and current, ensuring a strong bond.
- Resistance brazing is commonly used in the electronics and appliance manufacturing industries.
Each brazing method has its own set of advantages and limitations, making it essential to choose the right technique based on the materials, joint design, production volume, and application requirements.
Summary Table:
Method | Key Characteristics | Applications |
---|---|---|
Torch Brazing | Portable, versatile, requires skilled operators | On-site repairs, small-scale production |
Furnace Brazing | Uniform heating, high-volume production | Aerospace, automotive, electronics |
Induction Brazing | Precise, fast, energy-efficient | Medical, jewelry, high-precision parts |
Resistance Brazing | Localized heating, efficient for small parts | Electronics, appliance manufacturing |
Need help selecting the right brazing method for your project? Contact our experts today for personalized advice!