Sintering is a critical process in materials science and manufacturing, involving the transformation of powdered materials into a solid, cohesive structure through controlled heating and consolidation. The process is governed by six primary mechanisms that drive particle bonding and densification. These mechanisms include surface diffusion, grain boundary diffusion, lattice diffusion, vapor transport, plastic flow, and evaporation-condensation. Each mechanism plays a unique role in the sintering process, contributing to the final properties of the sintered product. Understanding these mechanisms is essential for optimizing sintering conditions in a sintering furnace to achieve desired material characteristics such as density, strength, and microstructure.
Key Points Explained:
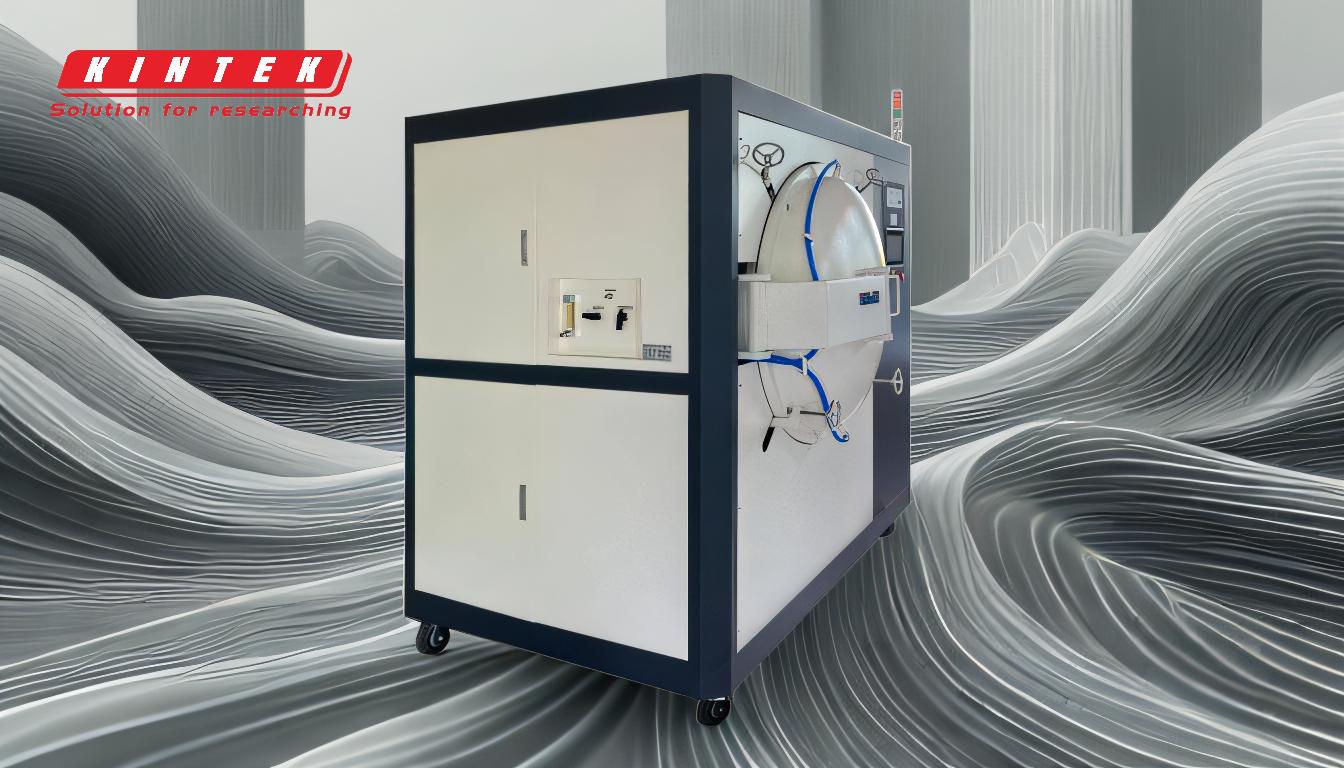
-
Surface Diffusion:
- Surface diffusion involves the movement of atoms along the surface of particles. This mechanism is particularly active at lower temperatures and contributes to the initial stages of sintering by forming necks between particles.
- It helps in reducing surface energy by smoothing out surface irregularities, leading to the initial bonding of particles.
-
Grain Boundary Diffusion:
- Grain boundary diffusion occurs when atoms move along the boundaries between particles. This mechanism is more significant at higher temperatures and plays a crucial role in densification.
- It facilitates the movement of material from the grain boundaries to the necks between particles, promoting further densification and strengthening of the material.
-
Lattice Diffusion:
- Lattice diffusion, also known as volume diffusion, involves the movement of atoms through the interior of the particles. This mechanism is dominant at high temperatures and is essential for the final stages of sintering.
- It contributes to the elimination of pores and the overall densification of the material, leading to a more homogeneous and dense structure.
-
Vapor Transport:
- Vapor transport involves the evaporation of material from the surface of particles and its subsequent condensation on other surfaces. This mechanism is more relevant in systems with high vapor pressures.
- It aids in the redistribution of material, helping to smooth out surface irregularities and promote particle bonding.
-
Plastic Flow:
- Plastic flow refers to the deformation of particles under stress, typically at high temperatures. This mechanism is important in the early stages of sintering when particles are still relatively soft.
- It helps in the rearrangement of particles, leading to better packing and initial densification.
-
Evaporation-Condensation:
- Evaporation-condensation involves the transfer of material from areas of high curvature (e.g., sharp edges) to areas of low curvature (e.g., necks between particles) through the vapor phase.
- This mechanism is particularly important in systems where the material has a significant vapor pressure at the sintering temperature, contributing to the smoothing of particle surfaces and the formation of strong bonds.
Understanding these six mechanisms is crucial for optimizing the sintering process in a sintering furnace. By controlling factors such as temperature, pressure, and atmosphere, manufacturers can influence the dominant mechanisms to achieve the desired material properties. For instance, higher temperatures may enhance lattice and grain boundary diffusion, leading to greater densification, while controlling the atmosphere can prevent unwanted reactions and ensure the stability of the sintered product.
Summary Table:
Mechanism | Description | Key Role in Sintering |
---|---|---|
Surface Diffusion | Movement of atoms along particle surfaces; active at lower temperatures. | Forms necks between particles, reduces surface energy. |
Grain Boundary Diffusion | Atom movement along particle boundaries; significant at higher temperatures. | Promotes densification and strengthens material. |
Lattice Diffusion | Atom movement through particle interiors; dominant at high temperatures. | Eliminates pores, enhances densification. |
Vapor Transport | Evaporation and condensation of material; relevant in high vapor systems. | Redistributes material, smooths surfaces. |
Plastic Flow | Particle deformation under stress; important in early sintering stages. | Rearranges particles, improves packing. |
Evaporation-Condensation | Material transfer via vapor phase; important in high vapor pressure systems. | Smooths surfaces, forms strong bonds. |
Optimize your sintering process with expert insights—contact us today!