Injection molding machines are widely used in manufacturing due to their ability to produce high volumes of parts with consistent quality. However, like any technology, they come with both advantages and disadvantages. The advantages include high production efficiency, repeatability, and the ability to create complex shapes with tight tolerances. On the other hand, the disadvantages include high initial costs, long setup times, and limitations in material selection. Understanding these pros and cons is essential for making informed decisions when considering injection molding for manufacturing processes.
Key Points Explained:
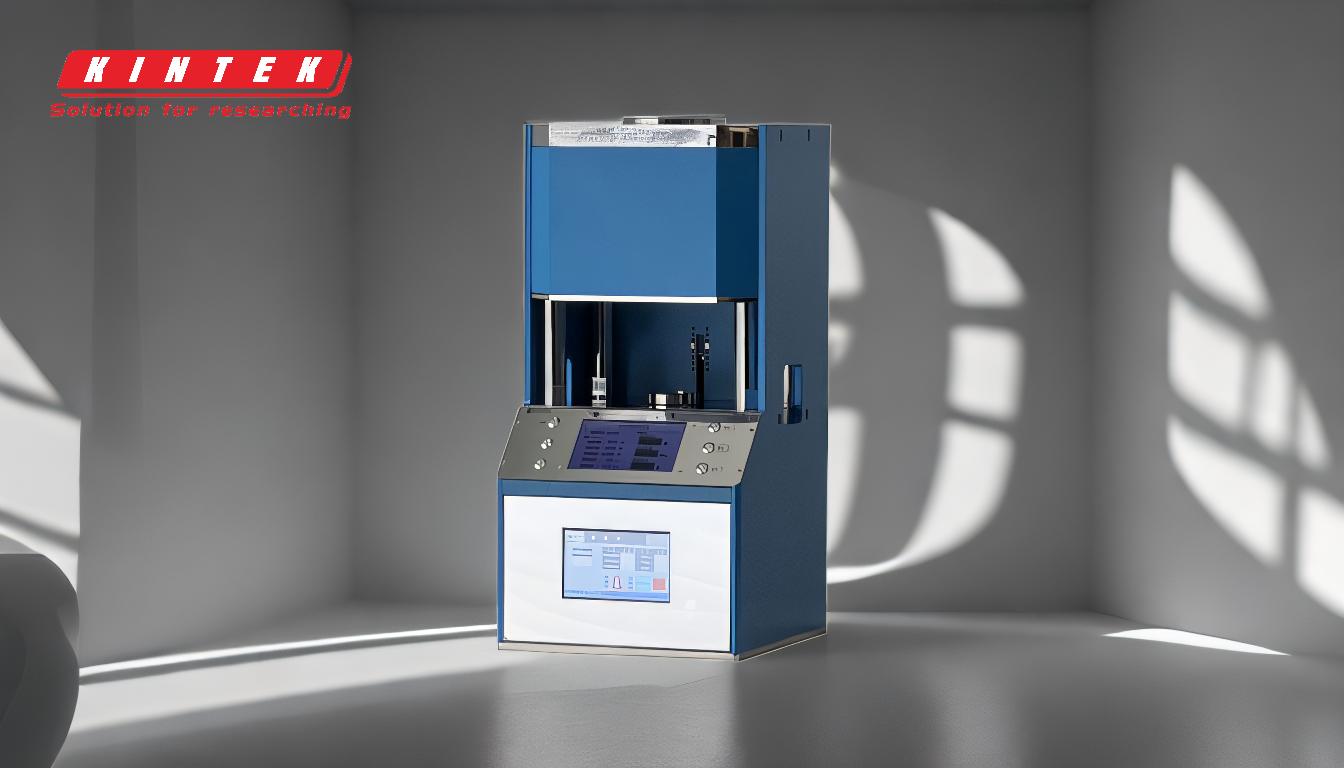
-
High Production Efficiency:
- Injection molding machines are capable of producing large quantities of parts in a short amount of time. This makes them ideal for mass production, where consistency and speed are critical.
- The process is automated, reducing the need for manual labor and minimizing human error. This automation also allows for continuous operation, further enhancing productivity.
-
Repeatability and Consistency:
- One of the standout features of injection molding is its ability to produce parts with high repeatability. Once the mold is set up and the machine is calibrated, each part produced will be nearly identical to the last.
- This consistency is crucial for industries where precision is paramount, such as automotive, medical, and electronics manufacturing.
-
Complex Geometry and Tight Tolerances:
- Injection molding allows for the creation of parts with complex geometries that would be difficult or impossible to achieve with other manufacturing methods.
- The process can achieve tight tolerances, ensuring that parts fit together perfectly in assemblies. This is particularly important in industries like aerospace and medical devices, where precision is critical.
-
High Initial Costs:
- The initial investment in an injection molding machine can be substantial. This includes not only the cost of the machine itself but also the molds, which can be expensive to design and manufacture.
- For small-scale production or prototyping, the high upfront costs may not be justified, making other manufacturing methods more attractive.
-
Long Setup Times:
- Setting up an injection molding machine for a new part can be time-consuming. This includes designing and manufacturing the mold, calibrating the machine, and running test cycles to ensure everything is working correctly.
- For companies that need to produce a variety of parts in small quantities, the long setup times can be a significant drawback.
-
Material Limitations:
- While injection molding can work with a wide range of materials, including plastics, metals, and ceramics, there are still limitations. Some materials may not be suitable for injection molding due to their properties, such as low melting points or poor flow characteristics.
- Additionally, the material selection can impact the cost and feasibility of the process, as some materials are more expensive or difficult to work with than others.
-
Energy Consumption:
- Injection molding machines can be energy-intensive, particularly when producing large volumes of parts. The process requires heating the material to its melting point, maintaining high pressure during injection, and cooling the part rapidly.
- This high energy consumption can lead to increased operational costs, especially in regions where energy prices are high.
-
Environmental Impact:
- The production of plastic parts through injection molding can have environmental implications, particularly if non-biodegradable materials are used. The process can generate waste, and the disposal of used molds and excess material can be problematic.
- However, advancements in recycling and the use of biodegradable materials are helping to mitigate some of these environmental concerns.
In conclusion, injection molding machines offer significant advantages in terms of production efficiency, repeatability, and the ability to create complex parts. However, the high initial costs, long setup times, and material limitations are important factors to consider. By weighing these pros and cons, manufacturers can make informed decisions about whether injection molding is the right choice for their specific needs.
Summary Table:
Aspect | Advantages | Disadvantages |
---|---|---|
Production Efficiency | High-speed, automated process ideal for mass production. | High initial costs and long setup times. |
Repeatability | Consistent, high-quality parts with minimal variation. | Material limitations may restrict options. |
Complex Geometry | Capable of creating intricate shapes with tight tolerances. | Energy-intensive process, leading to higher operational costs. |
Environmental Impact | Recyclable and biodegradable materials can mitigate waste. | Non-biodegradable materials may pose environmental challenges. |
Need help deciding if injection molding is right for your manufacturing needs? Contact our experts today for personalized advice!