Brazing is a metal-joining process that offers several advantages, such as the ability to join complex parts, reduce thermal distortion, and maintain close tolerances without melting the base metals. It is cost-effective, suitable for high-volume production, and can join dissimilar metals and nonmetals. However, it also has some limitations, such as the need for precise control of temperature and filler material, potential for weaker joints in high-stress applications, and the requirement for clean surfaces to ensure proper bonding. Below, we explore the key advantages and disadvantages of brazing in detail.
Key Points Explained:
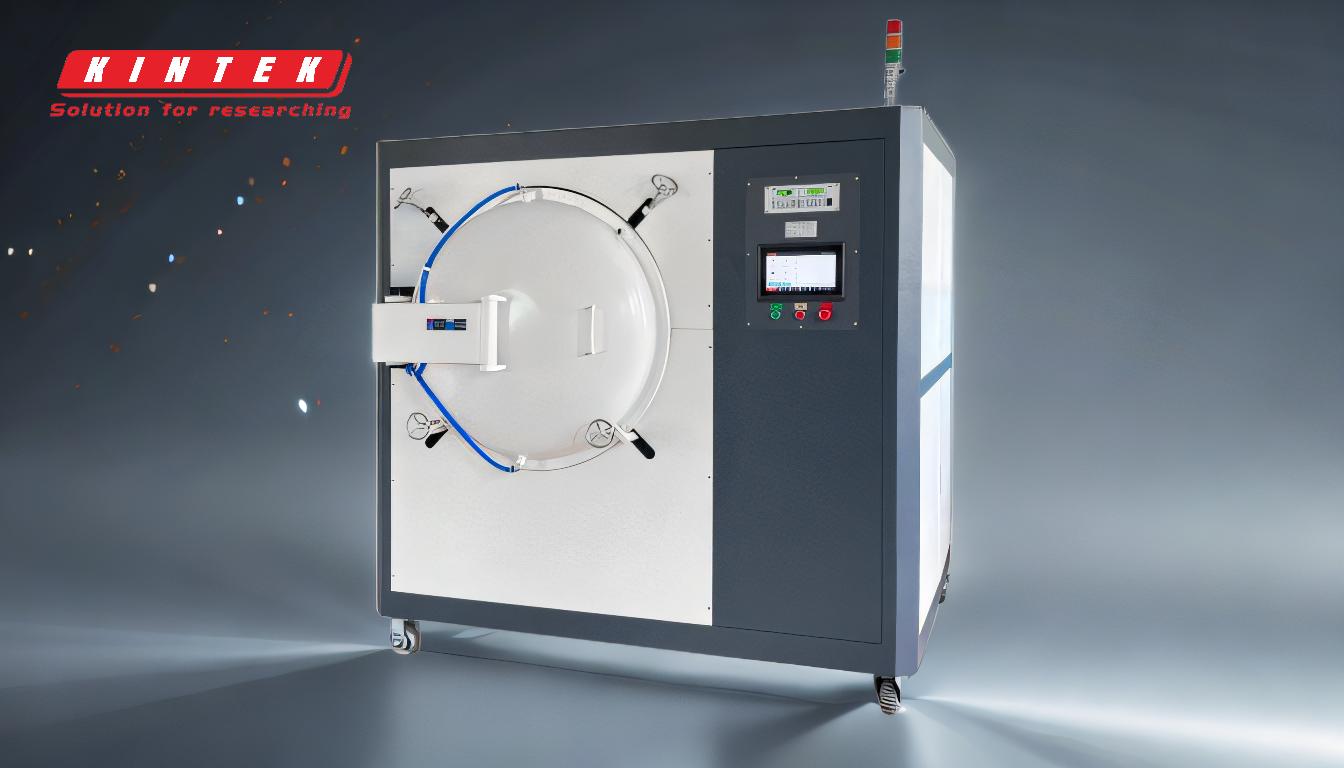
-
Advantages of Brazing:
-
No Melting of Base Metals:
- Brazing does not melt the base metals, which preserves their structural integrity and allows for close tolerances. This is particularly beneficial for delicate or precision components.
-
Joining Complex and Dissimilar Materials:
- Brazing can join complex parts, including dissimilar metals and nonmetals, which is often challenging with other joining methods like welding. This makes it versatile for a wide range of applications.
-
Reduced Thermal Distortion:
- Since the base metals are not melted, brazing generates less heat compared to welding, reducing the risk of thermal distortion. This is especially important for thin or heat-sensitive materials.
-
Cost-Effectiveness and High-Volume Production:
- Brazing is a cost-effective method for high-volume mass production. It allows for the simultaneous joining of multiple parts, increasing efficiency and reducing production time.
-
Strong and Durable Joints:
- The filler metal used in brazing solidifies to create strong and durable joints. This makes brazing suitable for applications requiring reliable and long-lasting connections.
-
No Melting of Base Metals:
-
Disadvantages of Brazing:
-
Precision in Temperature Control:
- Brazing requires precise control of temperature to ensure proper bonding. If the temperature is too low, the filler metal may not flow properly; if it is too high, it can damage the base metals.
-
Potential for Weaker Joints in High-Stress Applications:
- While brazed joints are strong, they may not be suitable for high-stress applications where welding or other methods might provide stronger bonds. The filler metal can be a weak point under extreme stress.
-
Surface Preparation Requirements:
- Brazing requires clean and properly prepared surfaces to ensure effective bonding. Any contamination, such as oil, grease, or oxide layers, can compromise the quality of the joint.
-
Limited to Certain Materials:
- Not all materials are suitable for brazing. Some metals and nonmetals may not bond well with common filler metals, limiting the applicability of brazing in certain scenarios.
-
Potential for Corrosion:
- Depending on the filler metal used, brazed joints may be susceptible to corrosion, especially in harsh environments. Proper selection of filler materials and protective coatings can mitigate this issue.
-
Precision in Temperature Control:
In summary, brazing is a versatile and effective method for joining metals, offering numerous advantages such as the ability to join complex parts, reduce thermal distortion, and maintain close tolerances. However, it also has some limitations, including the need for precise temperature control, potential for weaker joints in high-stress applications, and strict surface preparation requirements. Understanding these pros and cons is essential for selecting the appropriate joining method for specific applications.
Summary Table:
Aspect | Advantages | Disadvantages |
---|---|---|
No Melting of Base Metals | Preserves structural integrity and allows close tolerances. | Requires precise temperature control to avoid damage. |
Joining Complex Materials | Can join dissimilar metals and nonmetals, offering versatility. | Limited to certain materials; not all bond well with filler metals. |
Reduced Thermal Distortion | Generates less heat, reducing distortion in thin or heat-sensitive materials. | Potential for weaker joints in high-stress applications. |
Cost-Effectiveness | Suitable for high-volume production, reducing costs and time. | Requires clean and properly prepared surfaces for effective bonding. |
Joint Strength | Creates strong, durable joints for reliable connections. | Potential for corrosion depending on filler metal and environment. |
Looking to optimize your metal-joining process? Contact us today to learn more about brazing solutions tailored to your needs!