Chemical vapor deposition (CVD) is a widely used method for creating high-quality thin films and coatings. It offers numerous advantages, such as high versatility, precise control over material properties, and the ability to deposit ultra-thin layers on various substrates. However, it also has some disadvantages, including high operating temperatures, limitations in coating large surfaces, and the need for specialized equipment. Below, we explore the key advantages and disadvantages of the CVD method in detail.
Key Points Explained:
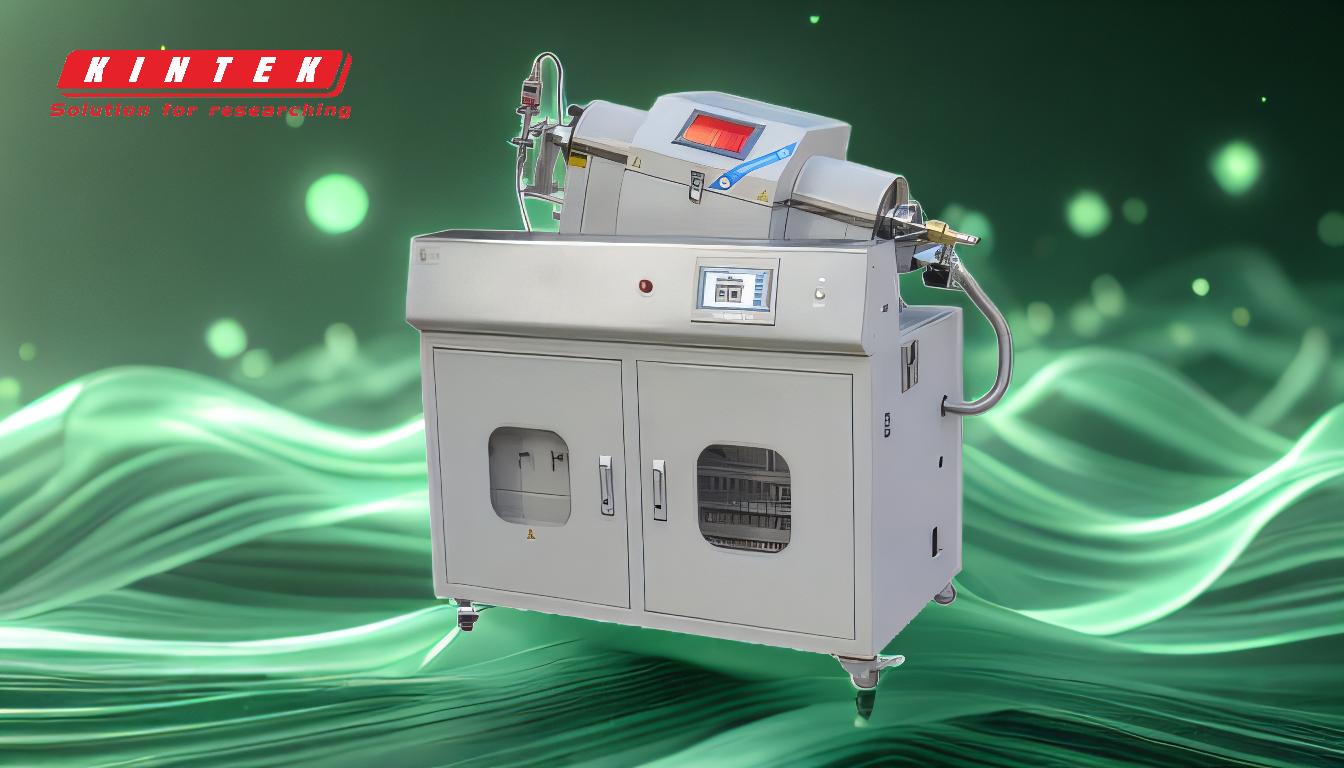
-
Advantages of Chemical Vapor Deposition:
-
High Versatility and Material Compatibility:
- CVD can be used to deposit a wide range of materials, including ceramics, metals, and glass. This makes it suitable for diverse applications, from electronics to aerospace.
- The process allows for the synthesis of both pure and complex materials, enabling tailored properties such as corrosion resistance, abrasion resistance, or high purity.
-
Precision and Control:
- CVD provides full control over deposition parameters like temperature, pressure, gas flow rate, and gas concentration. This allows for precise adjustment of the chemical and physical properties of the deposited films.
- It is ideal for creating ultra-thin layers, which are essential in applications like electrical circuits and semiconductor manufacturing.
-
High-Quality Coatings:
- The films produced by CVD are typically high-purity, dense, and uniform, with low residual stress and good crystallinity.
- The method offers excellent wrap-around properties, making it suitable for coating complex and precision surfaces.
-
Durability and Performance:
- CVD coatings are highly durable and can withstand high-stress environments, extreme temperatures, and temperature variations.
- Compared to other deposition methods, CVD provides smoother surfaces, better thickness control, and improved electrical and thermal conductivity.
-
Environmental Benefits:
- CVD often results in a reduced CO2 footprint compared to alternative technologies like pitch coating.
-
High Versatility and Material Compatibility:
-
Disadvantages of Chemical Vapor Deposition:
-
High Operating Temperatures:
- CVD typically requires high temperatures, which can be problematic for temperature-sensitive materials or substrates.
-
Limitations in Coating Large Surfaces:
- The size of the vacuum chamber used in CVD is limited, making it challenging to coat large or bulky components.
-
Complex Setup and Process Requirements:
- CVD cannot be performed on-site and often requires specialized coating centers. This adds logistical challenges and costs.
- All parts must be broken down into individual components for coating, which can be time-consuming and labor-intensive.
-
All-or-Nothing Process:
- CVD is difficult to use for partial coatings. The process either coats the entire surface or nothing at all, limiting its flexibility in certain applications.
-
Equipment and Maintenance Costs:
- While the equipment is relatively simple to operate, it can be expensive to purchase and maintain, especially for high-temperature and vacuum-based systems.
-
High Operating Temperatures:
In summary, chemical vapor deposition is a highly versatile and precise method for creating high-quality coatings and thin films. Its ability to deposit a wide range of materials and control film properties makes it invaluable in industries like electronics, aerospace, and manufacturing. However, its high operating temperatures, limitations in coating large surfaces, and logistical challenges are notable drawbacks. Understanding these advantages and disadvantages is crucial for selecting the right deposition method for specific applications. For more details, you can explore chemical vapor deposition.
Summary Table:
Aspect | Advantages | Disadvantages |
---|---|---|
Versatility | Deposits ceramics, metals, glass; suitable for electronics, aerospace, etc. | High operating temperatures may limit use with temperature-sensitive materials. |
Precision & Control | Full control over deposition parameters; ideal for ultra-thin layers. | Limited to coating small or medium-sized components due to chamber size. |
Coating Quality | High-purity, dense, uniform films with excellent wrap-around properties. | Requires specialized equipment and cannot be performed on-site. |
Durability | Withstands high stress, extreme temperatures, and temperature variations. | All-or-nothing process; partial coatings are not feasible. |
Environmental Impact | Reduced CO2 footprint compared to alternatives like pitch coating. | High equipment and maintenance costs. |
Need help choosing the right deposition method for your project? Contact our experts today for personalized guidance!