Chemical vapor deposition (CVD) is a highly versatile and efficient technique used to deposit thin films and coatings on various substrates. Its advantages include the ability to produce high-purity materials, excellent control over film properties, and the capacity to coat complex geometries uniformly. CVD is also cost-effective, environmentally friendly, and scalable for industrial applications. These benefits make it a preferred choice in industries such as semiconductors, aerospace, and energy.
Key Points Explained:
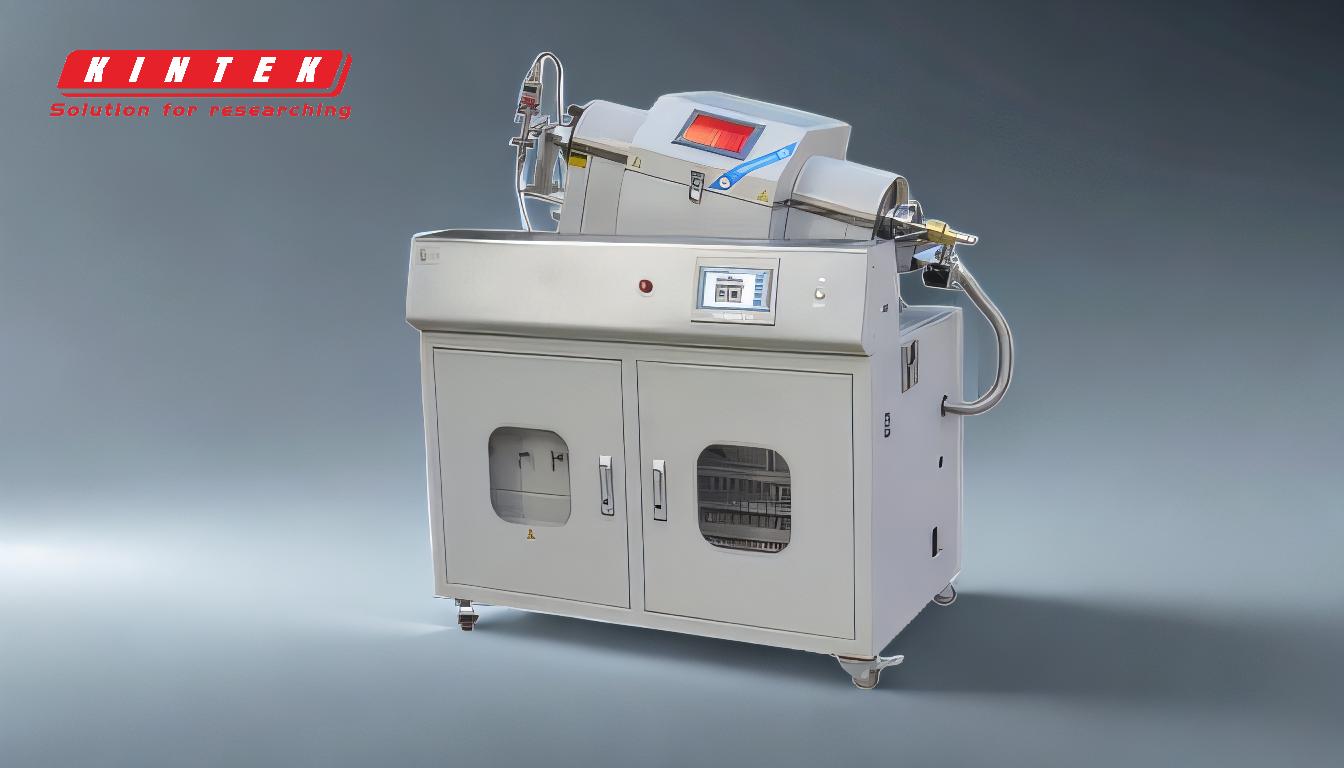
-
Versatility in Material Deposition:
- CVD can deposit a wide range of materials, including ceramics, metals, and glass. This versatility allows it to be used in diverse applications, from creating corrosion-resistant coatings to producing high-purity semiconductors.
- The process can be tailored to optimize specific properties such as abrasion resistance, thermal conductivity, or electrical conductivity, depending on the desired application.
-
High Purity and Dense Films:
- One of the standout advantages of chemical vapor deposition is its ability to produce films with exceptional purity and density. This is crucial for applications in electronics and optics, where impurities can significantly affect performance.
- The process allows for the synthesis of both single-crystalline and polycrystalline films, as well as amorphous materials, ensuring high-quality outputs.
-
Uniform Coating on Complex Geometries:
- CVD is a non-line-of-sight process, meaning it can uniformly coat components with intricate shapes and complex surfaces. This makes it ideal for applications in aerospace and precision engineering, where even coating is essential.
- The "wrap-around" property ensures that even hard-to-reach areas are adequately coated, enhancing the durability and performance of the coated parts.
-
Control Over Film Properties:
- By adjusting parameters such as temperature, pressure, gas flow rate, and gas concentration, the chemical and physical properties of the deposited films can be precisely controlled. This level of customization is invaluable for tailoring materials to specific industrial needs.
- For example, CVD can produce smoother surfaces, better thickness control, and improved adhesion compared to other deposition methods like pitch coating.
-
Cost-Effectiveness and Scalability:
- CVD equipment is relatively simple to operate and maintain, making it a cost-effective solution for both small-scale and large-scale production.
- The process is scalable, allowing for high manufacturing yields and consistent quality across batches, which is essential for industrial applications.
-
Environmental Benefits:
- Compared to other deposition technologies, CVD has a reduced CO2 footprint, making it a more environmentally friendly option.
- The ability to produce durable coatings that withstand extreme temperatures and harsh environments also contributes to longer product lifespans, reducing waste.
-
High Deposition Rates and Adhesion:
- CVD offers high deposition rates, ensuring efficient production without compromising on the quality of the coatings.
- The process provides commendable adhesion, ensuring that the coatings remain intact even under high-stress conditions.
In summary, chemical vapor deposition stands out as a highly adaptable, efficient, and environmentally friendly method for producing high-quality thin films and coatings. Its ability to uniformly coat complex geometries, control film properties, and scale for industrial use makes it a preferred choice across various industries.
Summary Table:
Advantage | Description |
---|---|
Versatility in Material Deposition | Deposits ceramics, metals, and glass for diverse applications. |
High Purity and Dense Films | Produces films with exceptional purity and density for electronics and optics. |
Uniform Coating on Complex Geometries | Non-line-of-sight process ensures even coating on intricate shapes. |
Control Over Film Properties | Adjustable parameters for precise customization of film properties. |
Cost-Effectiveness and Scalability | Simple operation, low maintenance, and scalable for industrial production. |
Environmental Benefits | Reduced CO2 footprint and durable coatings for longer product lifespans. |
High Deposition Rates and Adhesion | Efficient production with strong adhesion under high-stress conditions. |
Unlock the potential of chemical vapor deposition for your applications—contact our experts today!