Cold isostatic pressing (CIP) is a highly advantageous manufacturing process, particularly for producing complex shapes and achieving uniform material properties. Unlike traditional uniaxial pressing, CIP applies uniform pressure in all directions, ensuring consistent density and strength throughout the material. This eliminates the need for lubricants, reduces geometric constraints, and allows for efficient use of expensive or difficult-to-compact materials like superalloys, titanium, and stainless steel. Additionally, CIP enhances mechanical properties, improves corrosion resistance, and prepares materials for sintering, making it a versatile and cost-effective solution for industries requiring high-performance components. Its applications span powder metallurgy, refractory metal production, and advanced material engineering.
Key Points Explained:
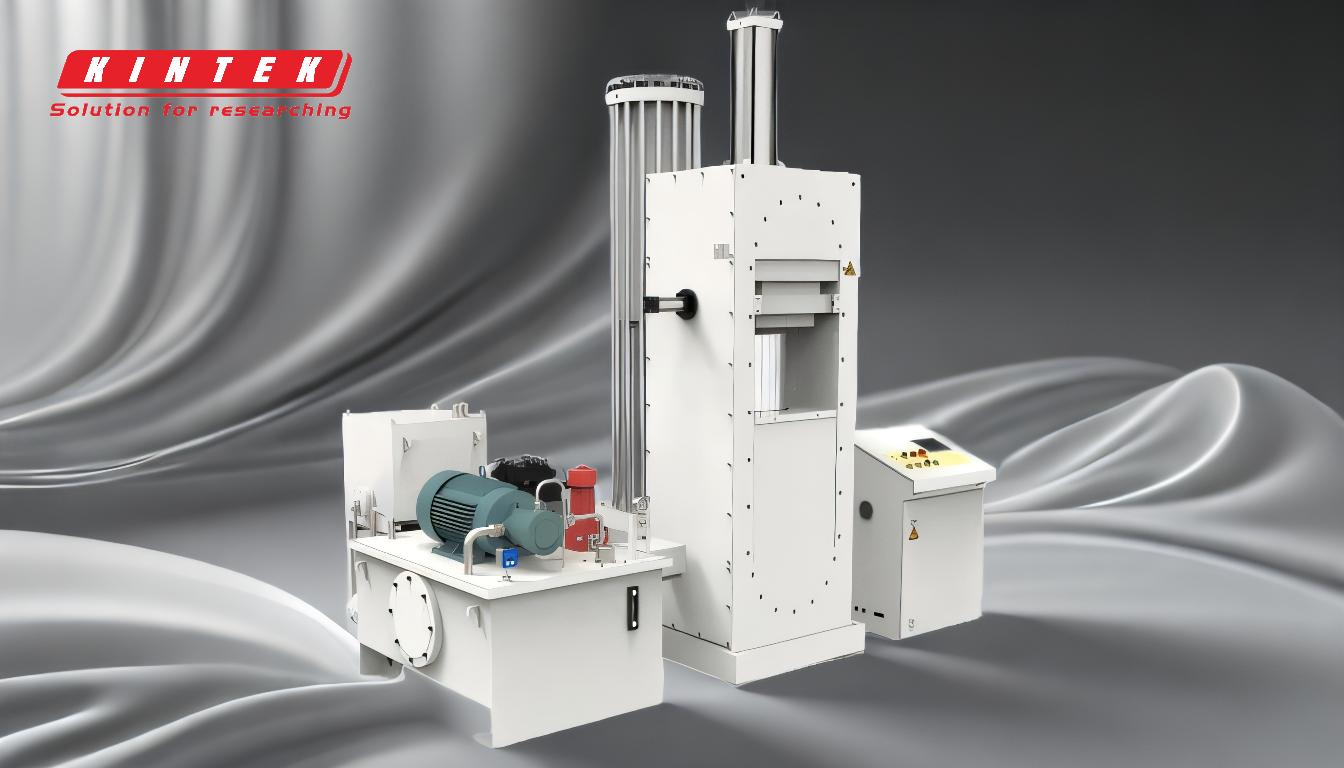
-
Uniform Pressure Application in All Directions
- CIP applies equal pressure from all sides, ensuring uniform density and strength throughout the material. This eliminates weak points or inconsistencies that often arise in uniaxial pressing methods.
- This uniformity is particularly beneficial for complex shapes, as it allows for precise engineering without compromising structural integrity.
-
No Need for Lubricants
- Unlike traditional pressing methods, CIP does not require lubricants, which can contaminate the material or complicate the manufacturing process.
- This reduces production costs and simplifies post-processing steps, such as cleaning or sintering.
-
High and Uniform Density
- CIP achieves high-density compacts, which are crucial for materials requiring superior mechanical properties, such as strength, toughness, and wear resistance.
- The uniform density also ensures isotropic properties, meaning the material behaves consistently in all directions.
-
Removal of Geometric Constraints
- Traditional uniaxial pressing is limited by geometric constraints, making it difficult to produce complex or intricate shapes.
- CIP overcomes these limitations by using elastomeric molds, enabling the production of components with intricate designs and tight tolerances.
-
Efficient Material Utilization
- CIP is ideal for processing expensive or difficult-to-compact materials, such as superalloys, titanium, and stainless steel.
- The process minimizes material waste, making it a cost-effective solution for high-value applications.
-
Improved Mechanical Properties
- The uniform pressure and density achieved through CIP result in enhanced mechanical properties, including better ductility, toughness, and fatigue resistance.
- These improvements are critical for components subjected to high stress or demanding operating conditions.
-
Versatility in Applications
- CIP is widely used in powder metallurgy, refractory metal production, and the preparation of materials for sintering.
- Its ability to handle a wide range of materials and shapes makes it a versatile choice for industries such as aerospace, automotive, and medical devices.
-
Corrosion Resistance
- The high density and uniform microstructure achieved through CIP contribute to improved corrosion resistance, extending the service life of components in harsh environments.
-
Preparation for Sintering
- CIP compacts are ideal for sintering, as their uniform density and microstructure ensure consistent shrinkage and dimensional stability during the sintering process.
- This reduces the risk of defects and improves the overall quality of the final product.
-
Economic Benefits
- By improving product performance, reducing waste, and enabling the use of advanced materials, CIP enhances economic efficiency in manufacturing.
- Its expanding application fields and technological maturity further contribute to its cost-effectiveness and widespread adoption.
In summary, cold isostatic pressing offers a unique combination of technical and economic advantages, making it a preferred choice for industries requiring high-performance materials and complex geometries. Its ability to deliver uniform density, superior mechanical properties, and efficient material utilization ensures its continued relevance in advanced manufacturing.
Summary Table:
Advantage | Description |
---|---|
Uniform Pressure Application | Ensures consistent density and strength in all directions, ideal for complex shapes. |
No Need for Lubricants | Eliminates contamination and reduces production costs. |
High and Uniform Density | Achieves superior mechanical properties and isotropic behavior. |
Removal of Geometric Constraints | Enables production of intricate designs with tight tolerances. |
Efficient Material Utilization | Minimizes waste, ideal for expensive or difficult-to-compact materials. |
Improved Mechanical Properties | Enhances ductility, toughness, and fatigue resistance. |
Versatility in Applications | Used in powder metallurgy, refractory metals, and advanced material engineering. |
Corrosion Resistance | Extends service life in harsh environments. |
Preparation for Sintering | Ensures consistent shrinkage and dimensional stability. |
Economic Benefits | Reduces waste, improves performance, and lowers costs. |
Ready to leverage the advantages of cold isostatic pressing for your next project? Contact us today to learn more!