Electric induction furnaces offer numerous advantages, making them a preferred choice in industrial and metallurgical applications. They are highly energy-efficient, environmentally friendly, and provide precise temperature control, which is crucial for maintaining the integrity of alloys. Their compact design, fast heating capabilities, and minimal waste generation further enhance their appeal. Additionally, induction furnaces improve working conditions by reducing pollution and ensuring uniform temperature distribution, which leads to better-quality outputs. These features make them ideal for continuous smelting and cost-effective operations.
Key Points Explained:
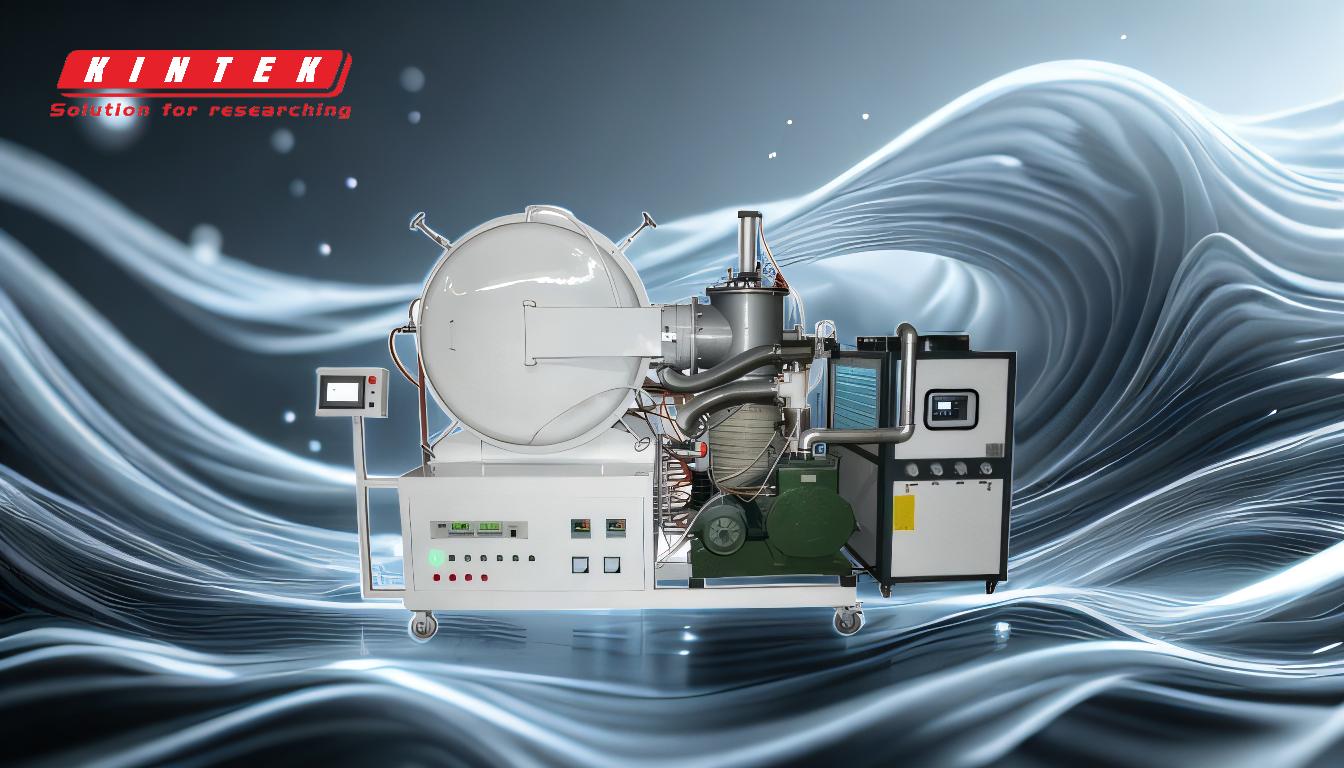
-
Energy Efficiency and Low Power Consumption:
- Induction furnaces are designed to be highly energy-efficient, converting electrical energy directly into heat within the metal charge. This reduces energy losses and lowers operational costs.
- The absence of an arc or combustion process minimizes energy wastage, making it a sustainable option for melting metals.
-
Environmental Friendliness and Reduced Pollution:
- Unlike traditional furnaces, induction furnaces do not rely on fossil fuels or produce harmful emissions, significantly reducing their carbon footprint.
- The enclosed design and lack of combustion prevent contamination from external sources, ensuring a cleaner melting process.
-
Precise Temperature Control:
- Induction furnaces allow for easy regulation of melting heat, which is critical for preserving valuable alloying elements and achieving consistent results.
- Advanced temperature control systems ensure uniform heating, reducing the risk of defects in the final product.
-
Compact and Lightweight Design:
- The small size and lightweight nature of induction furnaces make them easy to install and integrate into existing production lines.
- This compact design also reduces the space required for furnace operations, optimizing factory layouts.
-
Fast Heating and High Production Efficiency:
- Induction furnaces heat metals rapidly, significantly reducing melting times and increasing throughput.
- The high production efficiency translates to faster turnaround times and improved overall productivity.
-
Minimal Oxidation and Decarburization:
- The controlled environment of an induction furnace minimizes oxidation and decarburization, preserving the quality of the metal and reducing material waste.
- This feature is particularly beneficial for high-value alloys and precision applications.
-
Improved Working Conditions:
- Induction furnaces generate less heat and noise compared to traditional furnaces, creating a safer and more comfortable working environment.
- The absence of pollutants and fumes enhances worker health and safety.
-
Uniform Temperature Distribution and Magnetic Stirring:
- The magnetic stirring effect in induction furnaces ensures uniform composition and temperature throughout the molten metal, leading to higher-quality outputs.
- This uniformity reduces the need for additional processing steps, saving time and resources.
-
24-Hour Continuous Smelting Capability:
- Induction furnaces are capable of operating continuously, making them ideal for high-volume production environments.
- Their simple operation and low maintenance requirements further enhance their suitability for continuous use.
-
Cost Savings:
- The combination of low power consumption, reduced material waste, and high production efficiency results in significant cost savings over time.
- Additionally, the environmental benefits of induction furnaces can lead to lower regulatory compliance costs.
In summary, electric induction furnaces are a superior choice for modern metallurgical processes due to their energy efficiency, environmental benefits, precise control, and cost-effectiveness. Their ability to deliver high-quality outputs while improving working conditions makes them indispensable in industrial settings.
Summary Table:
Advantage | Description |
---|---|
Energy Efficiency | Converts electrical energy directly into heat, reducing energy losses. |
Environmental Friendliness | No fossil fuels or harmful emissions, reducing carbon footprint. |
Precise Temperature Control | Ensures uniform heating and preserves alloy integrity. |
Compact and Lightweight Design | Easy to install and integrates seamlessly into production lines. |
Fast Heating | Reduces melting times and increases throughput. |
Minimal Oxidation | Preserves metal quality and reduces waste. |
Improved Working Conditions | Less heat, noise, and pollutants for a safer environment. |
Uniform Temperature Distribution | Magnetic stirring ensures consistent composition and quality. |
24-Hour Continuous Smelting | Ideal for high-volume production with low maintenance. |
Cost Savings | Low power consumption and reduced waste lead to significant savings. |
Ready to enhance your metallurgical processes? Contact us today to learn more about electric induction furnaces!