Ion beam sputtering (IBS) is a highly advanced thin-film deposition technique that offers numerous advantages over traditional methods like evaporation or magnetron sputtering. It is particularly valued for its ability to produce high-quality, uniform films with superior adhesion, density, and purity. The process involves using a highly collimated ion beam to sputter target materials, which results in precise control over film properties such as stoichiometry, thickness, and composition. Key benefits include optimal energy bonding, versatility in target material selection, and the ability to achieve dense, defect-free films with excellent uniformity. These advantages make IBS ideal for applications requiring high precision and reliability, such as optical coatings, semiconductor devices, and advanced material research.
Key Points Explained:
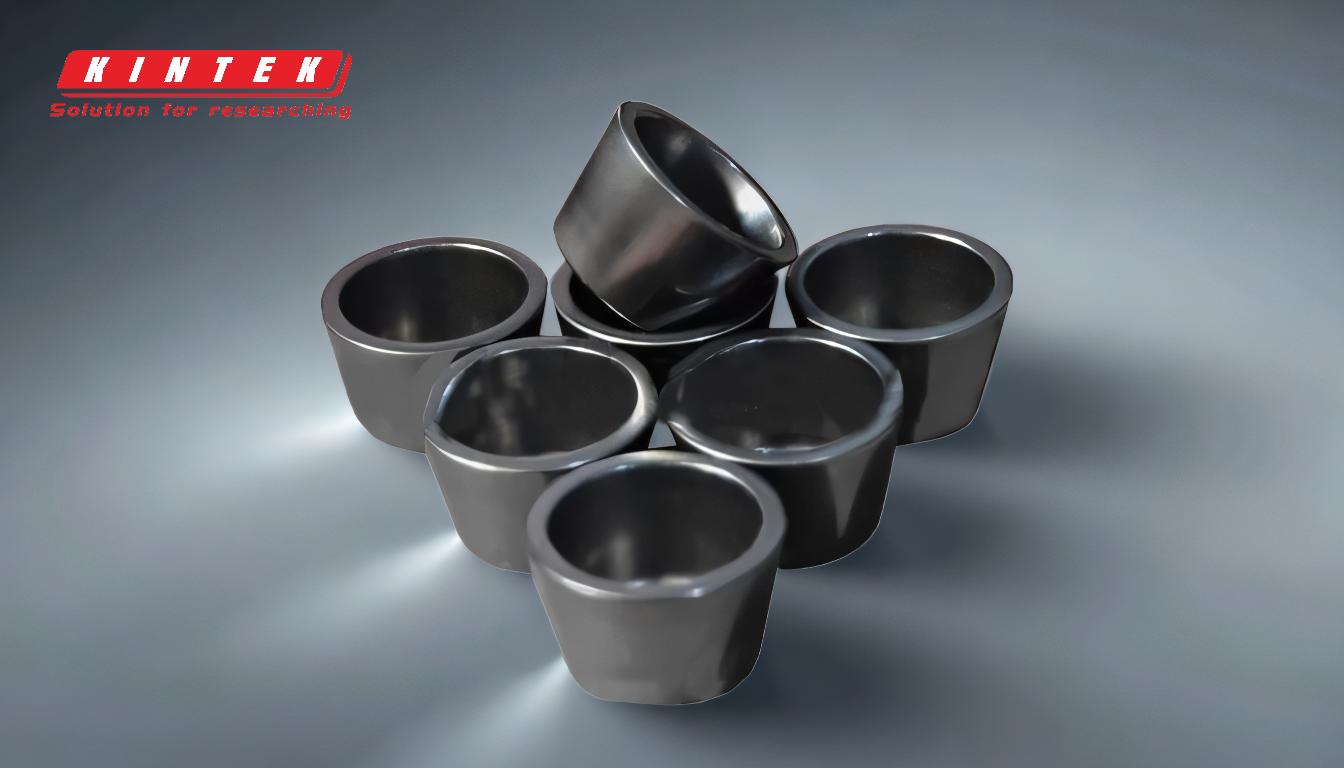
-
Superior Film Quality and Uniformity
- Ion beam sputtering produces films with exceptional density, smoothness, and uniformity. This is due to the highly collimated ion beam, which ensures that sputtered atoms are deposited evenly across the substrate.
- The process minimizes defects such as pinholes, resulting in films with high purity and fewer imperfections. This is critical for applications like optical coatings, where even minor defects can degrade performance.
- The uniformity of the film thickness is highly reproducible, making IBS suitable for applications requiring precise control over film properties.
-
Optimal Energy Bonding and Adhesion
- The energy of sputtered atoms in IBS is approximately 100 times higher than in traditional vacuum coating methods. This high energy enhances the bonding between the film and the substrate, leading to superior adhesion.
- The strong bond reduces the risk of delamination and improves the durability of the coating, which is essential for applications exposed to harsh environments or mechanical stress.
- The formation of a diffusion layer at the interface further strengthens the adhesion, ensuring long-term stability of the deposited film.
-
Versatility in Target Material Selection
- IBS can sputter a wide range of materials, including metals, semiconductors, insulators, compounds, and alloys. This versatility is particularly advantageous for materials with high melting points or low vapor pressure, which are challenging to deposit using other methods.
- The ability to use solids of any shape as target materials expands the range of possible applications, from simple metal coatings to complex multi-layer structures.
- The process also allows for greater flexibility in achieving specific film compositions, making it ideal for customizing material properties to meet specific requirements.
-
Precision Control Over Film Properties
- IBS provides independent control over film stoichiometry and thickness, enabling the deposition of films with tailored properties. This is achieved by adjusting parameters such as ion beam energy, target current, and deposition time.
- The highly collimated ion beam ensures that the ions possess equal energy, resulting in consistent film properties across the entire substrate.
- This level of control is particularly beneficial for applications in optics, electronics, and nanotechnology, where precise film characteristics are critical.
-
Environmental and Operational Advantages
- IBS is an environmentally friendly process, as it does not involve the use of harmful chemicals or produce significant waste. The ability to deposit small quantities of materials further reduces environmental impact.
- The process can be performed in a single vacuum chamber, allowing for substrate cleaning and coating deposition in one step. This reduces processing time and improves efficiency.
- The reproducibility of the sputtering technique ensures consistent results, which is essential for high-volume production and industrial applications.
-
Comparison with Other Deposition Methods
- Compared to evaporation, IBS offers better film quality and uniformity but at a higher cost and complexity. Evaporation is more suitable for large batch processing due to its higher deposition rates.
- Magnetron sputtering is often preferred for high-volume production of thin films with short deposition times, but it may not match the precision and film quality achievable with IBS.
- IBS stands out for its ability to produce dense, defect-free films with superior adhesion, making it the preferred choice for high-precision applications.
In summary, ion beam sputtering is a highly versatile and precise deposition technique that offers significant advantages in terms of film quality, adhesion, and control. Its ability to handle a wide range of materials and produce uniform, defect-free films makes it indispensable for advanced applications in optics, electronics, and materials science. While it may be more costly and complex than other methods, its superior performance justifies its use in critical applications where precision and reliability are paramount.
Summary Table:
Advantages of Ion Beam Sputtering (IBS) | Key Details |
---|---|
Superior Film Quality & Uniformity | Exceptional density, smoothness, and uniformity; minimal defects like pinholes. |
Optimal Energy Bonding & Adhesion | High-energy bonding enhances adhesion, reduces delamination, and improves durability. |
Versatility in Target Material Selection | Works with metals, semiconductors, insulators, compounds, and alloys. |
Precision Control Over Film Properties | Tailored stoichiometry, thickness, and composition for specific applications. |
Environmental & Operational Advantages | Eco-friendly, single-chamber processing, and high reproducibility. |
Comparison with Other Methods | Superior to evaporation and magnetron sputtering in precision and film quality. |
Unlock the potential of ion beam sputtering for your precision applications—contact our experts today!