Microwave sintering is a modern sintering technique that leverages the dielectric properties of materials to achieve efficient and uniform heating. This method offers numerous advantages over traditional sintering techniques, including faster heating rates, uniform temperature distribution, energy efficiency, and improved mechanical properties of the sintered materials. It is particularly beneficial for high-performance ceramics and materials that require precise control over microstructure and density. Below, the key advantages of microwave sintering are explained in detail.
Key Points Explained:
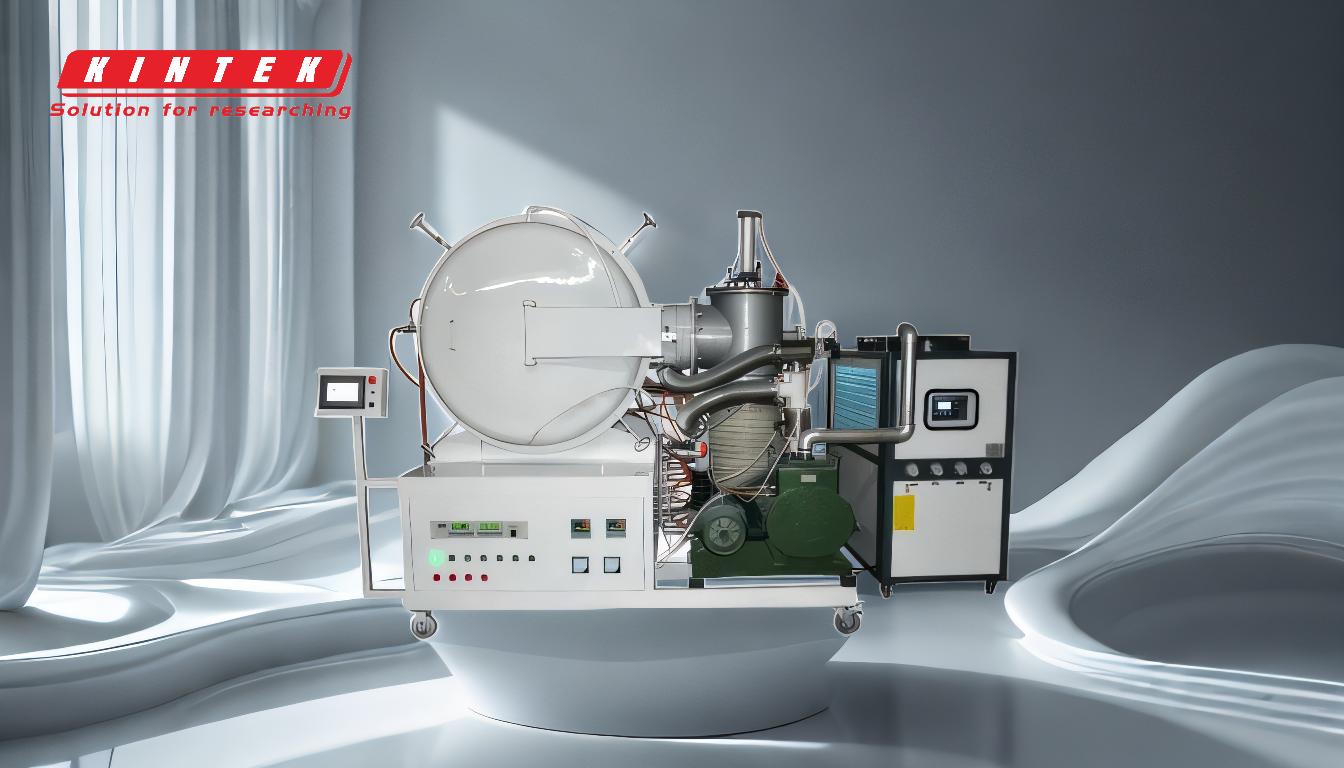
-
Fast Heating Rate and High Efficiency:
- Microwave sintering heats materials directly through the absorption of microwave energy, which leads to rapid heating. This is in contrast to conventional methods that rely on external heat sources and slower conduction processes.
- The direct interaction between microwaves and the material allows for quicker temperature rise, significantly reducing the overall sintering time. This makes the process highly efficient and suitable for industrial applications where time is critical.
-
Uniform Temperature Distribution:
- Microwave sintering ensures uniform heating throughout the material, minimizing internal temperature gradients. This uniformity is crucial for achieving consistent material properties and preventing defects such as warping or cracking.
- Traditional methods often result in uneven heating, especially in thicker or more complex geometries, which can compromise the quality of the final product.
-
Low-Temperature Sintering:
- Microwave sintering enables sintering at lower temperatures compared to conventional methods. This is due to the efficient energy transfer and localized heating within the material.
- Lower sintering temperatures reduce energy consumption and minimize the risk of thermal damage to sensitive materials, making it ideal for advanced ceramics and composites.
-
Energy Efficiency and Environmental Friendliness:
- The direct heating mechanism of microwave sintering reduces energy losses associated with conventional heating methods, such as conduction and radiation.
- This energy efficiency translates to lower operational costs and a reduced carbon footprint, aligning with sustainable manufacturing practices.
-
Improved Mechanical Properties:
- Microwave sintering results in finer grain sizes and rounded porosity, which enhance the mechanical properties of the sintered materials. Finer grains contribute to higher strength and hardness, while rounded porosity improves ductility and toughness.
- These improvements make microwave-sintered materials suitable for demanding applications in industries such as aerospace, automotive, and electronics.
-
Prevention of Oxidation and Pollution:
- Microwave sintering can be performed in controlled atmospheres, preventing oxidation and contamination of the material. This is particularly important for materials that are sensitive to oxygen or other reactive gases.
- The absence of oxidation and pollution ensures higher product quality and reliability.
-
Versatility and Flexibility:
- Microwave sintering furnaces offer options for batch or continuous processing, as well as hybrid solutions for materials that do not absorb microwaves effectively at lower temperatures. This versatility makes the technique adaptable to a wide range of materials and applications.
- The ability to control the atmosphere and heating parameters further enhances the flexibility of the process.
-
Overcoming Limitations of Traditional Methods:
- Traditional sintering methods may struggle with materials that have high compactness, as they can reduce the propagation rate of the combustion wave or cause "self-extinguishing." Microwave sintering overcomes this limitation by enabling rapid and uniform heating, ensuring the reaction is sustained until completion.
In summary, microwave sintering stands out as a superior sintering technique due to its speed, efficiency, and ability to produce high-quality materials with enhanced mechanical properties. Its environmental benefits and versatility further solidify its position as a preferred method for advanced material processing.
Summary Table:
Advantage | Description |
---|---|
Fast Heating Rate | Direct microwave absorption enables rapid heating, reducing sintering time. |
Uniform Temperature | Ensures even heating, minimizing defects like warping or cracking. |
Low-Temperature Sintering | Sinters at lower temperatures, reducing energy use and thermal damage. |
Energy Efficiency | Direct heating reduces energy losses, lowering costs and environmental impact. |
Improved Mechanical Properties | Finer grain sizes and rounded porosity enhance strength, hardness, and ductility. |
Prevents Oxidation | Controlled atmospheres prevent material contamination and oxidation. |
Versatility | Adaptable to batch, continuous, or hybrid processing for diverse applications. |
Overcomes Traditional Limits | Rapid, uniform heating ensures sustained reactions, even for dense materials. |
Transform your material processing with microwave sintering—contact our experts today to learn more!