Plasma deposition, often compared to chemical vapor deposition, offers unique advantages in thin-film coating and material synthesis. It leverages plasma, a highly energized state of matter, to enable precise control over film properties, enhanced adhesion, and the ability to deposit coatings on complex geometries. Plasma deposition is particularly advantageous for creating high-purity, uniform, and durable coatings, making it suitable for applications in electronics, optics, and protective coatings. Its ability to operate at lower temperatures compared to traditional methods also makes it ideal for temperature-sensitive substrates.
Key Points Explained:
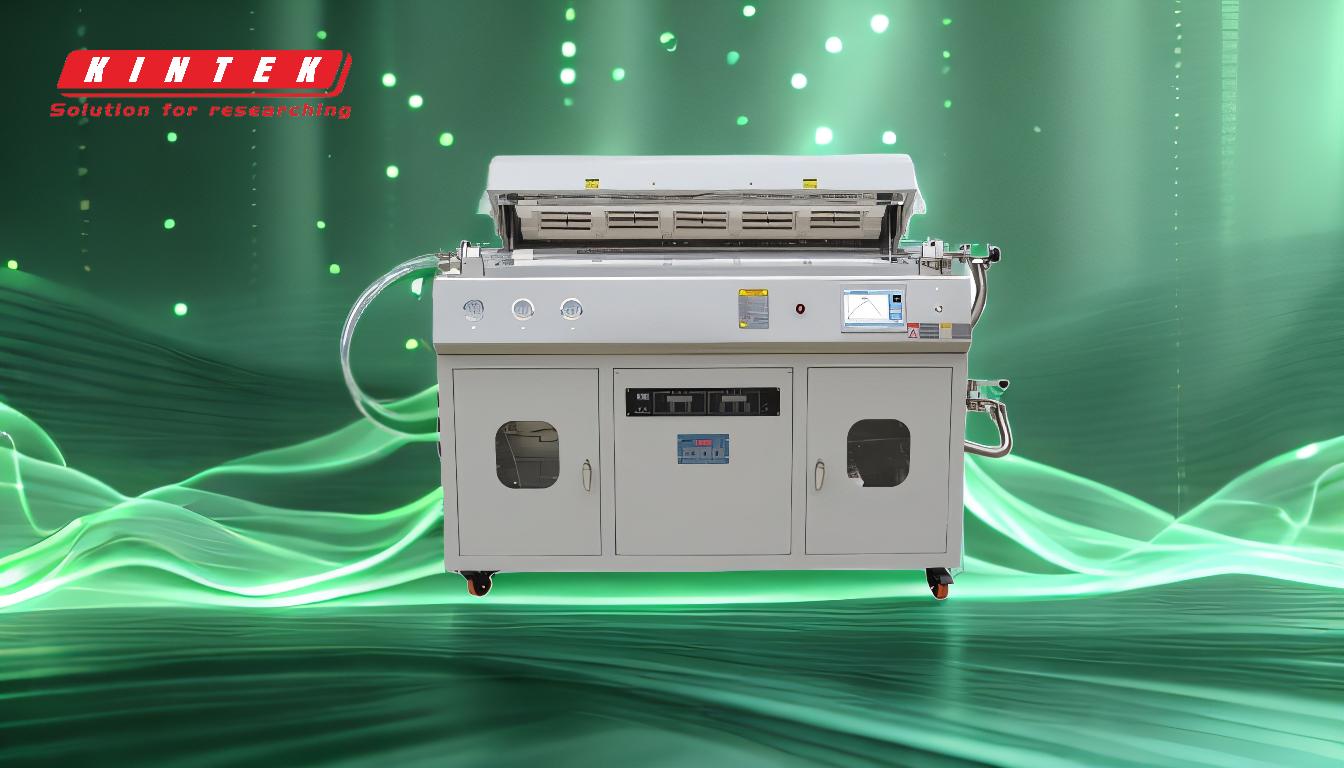
-
Enhanced Control Over Film Properties:
- Plasma deposition allows precise control over film thickness, composition, and microstructure. By adjusting parameters such as plasma power, gas flow rates, and substrate temperature, users can tailor the properties of the deposited films to meet specific application requirements. This level of control is critical for applications in semiconductors, optics, and advanced materials.
-
Improved Adhesion and Durability:
- The high-energy nature of plasma enhances the bonding between the deposited material and the substrate, resulting in superior adhesion. This makes plasma-deposited coatings highly durable and resistant to wear, corrosion, and high-stress environments. For example, plasma-deposited protective coatings are widely used in aerospace and automotive industries.
-
Versatility in Material Deposition:
- Plasma deposition can be used to deposit a wide range of materials, including metals, ceramics, polymers, and composites. This versatility makes it suitable for diverse applications, from creating conductive layers in electronics to depositing anti-reflective coatings on optical lenses.
-
Ability to Coat Complex Geometries:
- Unlike some traditional deposition methods, plasma deposition can uniformly coat complex and three-dimensional surfaces. This is particularly beneficial for applications such as medical devices, where precise and uniform coatings are required on intricate shapes.
-
Lower Temperature Processing:
- Plasma deposition often operates at lower temperatures compared to methods like chemical vapor deposition. This makes it suitable for temperature-sensitive substrates, such as polymers or certain metals, which might degrade or deform at higher temperatures.
-
High Purity and Uniformity:
- The use of plasma ensures that the deposited films are highly pure and uniform. This is essential for applications in microelectronics and photovoltaics, where even minor impurities or inconsistencies can significantly impact performance.
-
Environmental and Energy Efficiency:
- Plasma deposition is generally more energy-efficient and environmentally friendly compared to some traditional methods. It often requires less material waste and can be performed in a vacuum, reducing the risk of contamination and minimizing the release of harmful byproducts.
-
Scalability and Industrial Applicability:
- Plasma deposition techniques are scalable and can be adapted for large-scale industrial production. This makes them a cost-effective solution for manufacturing high-performance coatings and thin films in industries such as electronics, energy, and healthcare.
In summary, plasma deposition offers a combination of precision, versatility, and efficiency that makes it a superior choice for many advanced material applications. Its ability to produce high-quality, durable coatings on a variety of substrates, including complex geometries, positions it as a key technology in modern manufacturing and materials science.
Summary Table:
Advantage | Key Benefit |
---|---|
Enhanced Control Over Film Properties | Precise control over thickness, composition, and microstructure for tailored results. |
Improved Adhesion and Durability | Superior bonding and resistance to wear, corrosion, and high-stress environments. |
Versatility in Material Deposition | Deposits metals, ceramics, polymers, and composites for diverse applications. |
Ability to Coat Complex Geometries | Uniform coatings on intricate 3D surfaces, ideal for medical devices and more. |
Lower Temperature Processing | Suitable for temperature-sensitive substrates like polymers and certain metals. |
High Purity and Uniformity | Ensures highly pure, uniform films critical for microelectronics and photovoltaics. |
Environmental and Energy Efficiency | Energy-efficient, reduces material waste, and minimizes harmful byproducts. |
Scalability and Industrial Applicability | Adaptable for large-scale production in electronics, energy, and healthcare. |
Unlock the potential of plasma deposition for your applications—contact our experts today to learn more!