Spark plasma sintering (SPS) is an advanced sintering technique that offers numerous advantages over traditional sintering methods. It is particularly valued for its ability to produce high-quality, dense materials with fine microstructures in a short time. The process leverages rapid heating, uniform temperature distribution, and controlled grain growth to achieve materials with superior mechanical, electrical, and thermal properties. SPS is also energy-efficient and cost-effective, making it suitable for a wide range of applications, including advanced ceramics, metals, and composites. Below, the key advantages of SPS are explained in detail.
Key Points Explained:
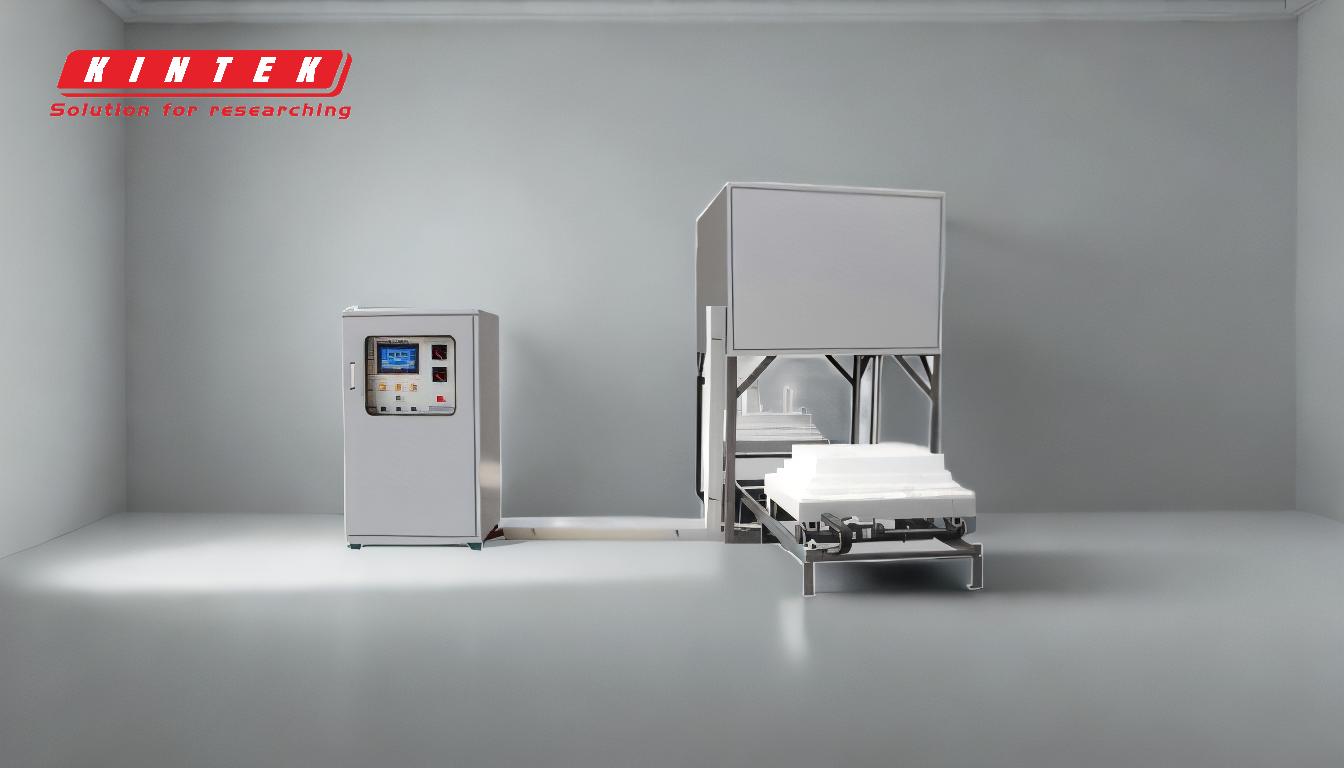
-
Fast Heating Speed and Short Sintering Time
- SPS utilizes direct current pulses to generate rapid heating, significantly reducing the sintering time compared to conventional methods. This rapid heating minimizes grain growth, resulting in a fine and uniform microstructure.
- The short sintering time also enhances production efficiency, making SPS ideal for industrial applications where time is a critical factor.
-
Low Sintering Temperature
- SPS operates at lower temperatures compared to traditional sintering techniques. This is due to the combined effects of Joule heating and plasma generation, which enhance densification without requiring excessively high temperatures.
- Lower sintering temperatures reduce energy consumption and prevent thermal damage to sensitive materials, such as nanostructured ceramics or composites.
-
Uniform Heating and High Density
- The SPS process ensures uniform heating throughout the sample, eliminating temperature gradients that can lead to defects or uneven densification.
- This uniformity, combined with the application of pressure, results in materials with high density and minimal porosity, which are critical for achieving superior mechanical and functional properties.
-
Inhibition of Grain Growth
- One of the standout features of SPS is its ability to inhibit excessive grain growth during sintering. This is achieved through the rapid heating and cooling cycles, which limit the time available for grain coarsening.
- Maintaining fine grain sizes enhances the mechanical strength, hardness, and wear resistance of the sintered material.
-
Energy Efficiency and Cost-Effectiveness
- The fast processing times and lower sintering temperatures of SPS translate into significant energy savings. This makes the process more environmentally friendly and cost-effective, especially for large-scale production.
- Additionally, the ability to produce near-net-shape components reduces material waste and post-processing requirements, further lowering costs.
-
Versatility with Difficult Materials
- SPS is particularly effective for sintering materials that are challenging to process using traditional methods, such as high-melting-point metals, ceramics, and composites.
- The process can achieve full densification of these materials without compromising their unique properties, making it suitable for advanced applications like aerospace components, biomedical implants, and electronic devices.
-
Improved Material Properties
- SPS enhances key material properties, including strength, electrical conductivity, thermal conductivity, and transparency. For example, piezoelectric ceramics produced via SPS exhibit optimized performance due to the elimination of defects and uniform pore distribution.
- The process also allows for the creation of materials with tailored porosity, which is beneficial for applications like filters or catalysts.
-
Simple Operation and High Repeatability
- SPS systems are relatively simple to operate and require minimal technical expertise. The process parameters, such as temperature, pressure, and heating rate, can be precisely controlled, ensuring high repeatability and consistency in the final products.
- This repeatability is crucial for industries that demand high precision and reliability, such as automotive and electronics manufacturing.
-
Production of Complex Geometries
- SPS enables the production of complex, non-machinable geometries with high accuracy. This capability is particularly valuable for mass production, where traditional machining processes would be time-consuming and costly.
- The ability to create near-net-shape components also reduces the need for additional finishing processes, further enhancing efficiency.
In summary, spark plasma sintering offers a combination of speed, precision, and material versatility that makes it a superior choice for modern manufacturing and research. Its ability to produce high-performance materials with fine microstructures and minimal defects positions it as a key technology in advancing materials science and engineering.
Summary Table:
Advantage | Key Benefit |
---|---|
Fast Heating & Short Sintering | Reduces sintering time, minimizes grain growth, and enhances production efficiency. |
Low Sintering Temperature | Lowers energy consumption and prevents thermal damage to sensitive materials. |
Uniform Heating & High Density | Ensures uniform heating, high density, and minimal porosity for superior properties. |
Inhibition of Grain Growth | Maintains fine grain sizes, enhancing strength, hardness, and wear resistance. |
Energy Efficiency & Cost Savings | Saves energy and reduces costs, especially for large-scale production. |
Versatility with Difficult Materials | Effective for high-melting-point metals, ceramics, and composites. |
Improved Material Properties | Enhances strength, conductivity, and transparency while allowing tailored porosity. |
Simple Operation & Repeatability | Easy to operate with precise control for high repeatability and consistency. |
Complex Geometries Production | Enables production of complex, non-machinable geometries with high accuracy. |
Ready to enhance your material performance with spark plasma sintering? Contact us today to learn more!