Chemical vapor deposition (CVD) is a highly versatile and efficient process used to deposit high-quality thin films and coatings on various substrates. Its advantages include affordability, high deposition rates, excellent adhesion, uniform coatings, and the ability to produce high-purity materials. CVD is a non-line-of-sight process, making it suitable for coating complex and precision surfaces. It offers improved performance in terms of thickness control, surface smoothness, and compatibility with other materials. Additionally, CVD is environmentally friendly, with a reduced CO2 footprint compared to other deposition technologies. Its ability to withstand extreme temperatures and high-stress environments further enhances its applicability in industries such as electronics, aerospace, and materials science.
Key Points Explained:
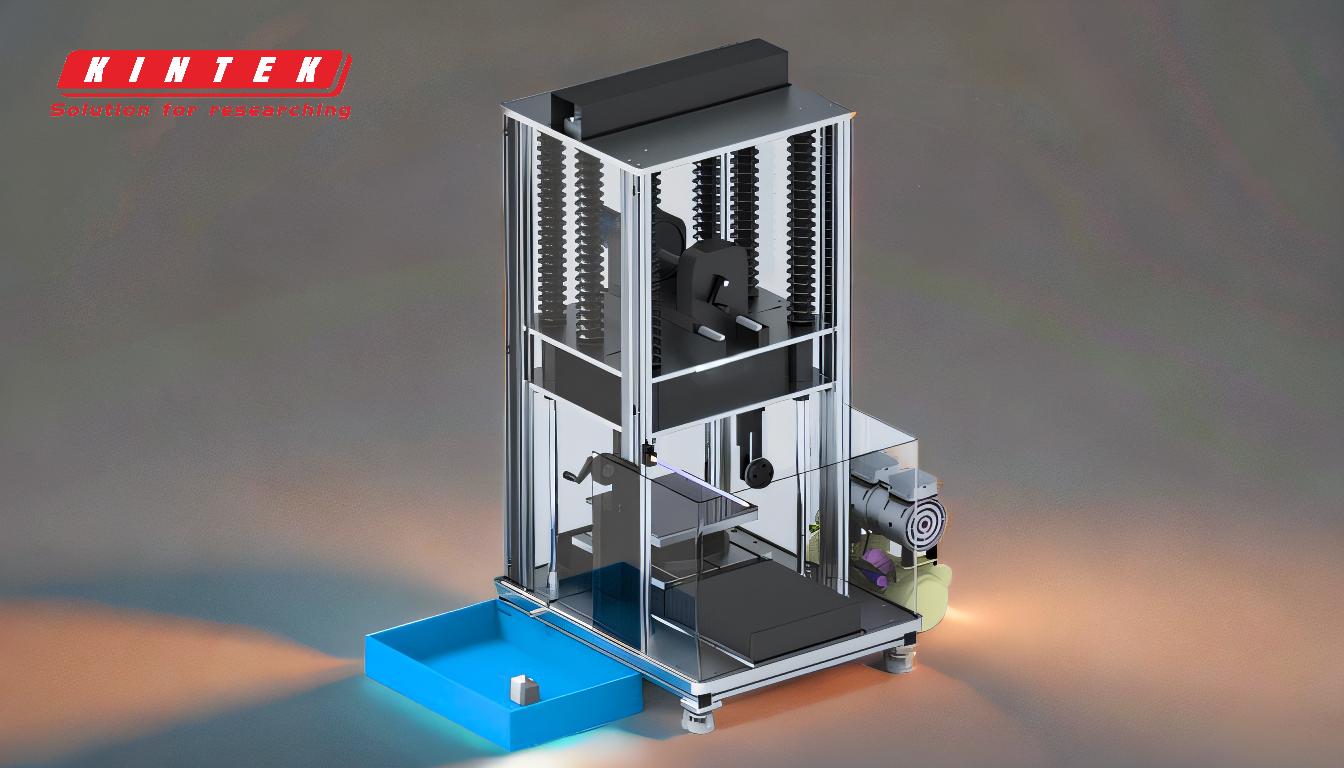
-
Versatility and Wide Applicability:
- CVD can be used on a wide range of materials, including ceramics, metals, and glass. This makes it suitable for diverse applications, from electronics to aerospace.
- The process allows for the optimization of gases to achieve specific properties such as corrosion resistance, abrasion resistance, or high purity.
-
High Deposition Rate and Uniform Coating:
- CVD offers a high deposition rate, which is beneficial for industrial applications requiring rapid production.
- The process provides uniform coatings, ensuring consistent quality across the entire surface of the substrate.
-
High Purity and Dense Films:
- CVD produces high-purity materials, which are essential for applications in electronics and semiconductors.
- The films produced are dense and have low residual stress, contributing to their durability and performance.
-
Non-Line-of-Sight Process:
- As a non-line-of-sight process, CVD can coat complex and precision surfaces, including those with intricate geometries.
- This capability is particularly valuable in industries where components have complex shapes, such as in aerospace and medical devices.
-
Improved Performance and Compatibility:
- CVD provides better thickness control compared to other deposition technologies, resulting in smoother surfaces.
- The process enhances electrical and thermal conductivity and improves mixing compatibility with other materials.
-
Environmental Benefits:
- CVD has a reduced CO2 footprint compared to other coating technologies, making it a more environmentally friendly option.
-
Durability and Resistance:
- The coatings produced by CVD are durable and can withstand high-stress environments.
- They maintain their properties even when exposed to extreme temperatures or temperature variations.
-
Control and Precision:
- CVD allows for full control over the timing of the process, enabling the creation of ultra-thin layers of material.
- This precision is crucial for applications such as the production of electrical circuits and graphene.
-
Simple and Easy to Operate Equipment:
- The equipment used in CVD is relatively simple and easy to operate and maintain, reducing operational costs and complexity.
-
Wrap-Around Properties:
- CVD has good wrap-around properties, meaning it can effectively coat complex surfaces with uniform thickness and quality.
In summary, chemical vapor deposition offers a multitude of advantages, including versatility, high-quality coatings, environmental benefits, and the ability to coat complex surfaces. These attributes make it a preferred choice in various industries for producing high-performance materials and components.
Summary Table:
Advantage | Description |
---|---|
Versatility | Suitable for ceramics, metals, glass; ideal for electronics, aerospace, etc. |
High Deposition Rate | Rapid production with uniform coatings for consistent quality. |
High Purity & Dense Films | Produces durable, low-stress films essential for electronics and semiconductors. |
Non-Line-of-Sight Process | Coats complex and precision surfaces, even with intricate geometries. |
Environmental Benefits | Reduced CO2 footprint compared to other coating technologies. |
Durability & Resistance | Withstands extreme temperatures and high-stress environments. |
Control & Precision | Enables ultra-thin layers for applications like electrical circuits and graphene. |
Simple Equipment Operation | Easy to operate and maintain, reducing costs and complexity. |
Wrap-Around Properties | Uniformly coats complex surfaces with consistent thickness and quality. |
Discover how CVD can enhance your material performance—contact our experts today!