Diamond-like carbon (DLC) coatings are versatile and widely used across multiple industries due to their unique combination of properties, including high hardness, low friction, chemical resistance, and biocompatibility. These coatings are applied to enhance wear resistance, reduce friction, and improve the durability of components in industries such as automotive, machinery, optics, biomedical, and even luxury goods like watches. DLC coatings are particularly valued for their ability to be deposited at low temperatures, ensuring compatibility with a wide range of substrates while maintaining strong adhesion and precise control over thickness and refractive index.
Key Points Explained:
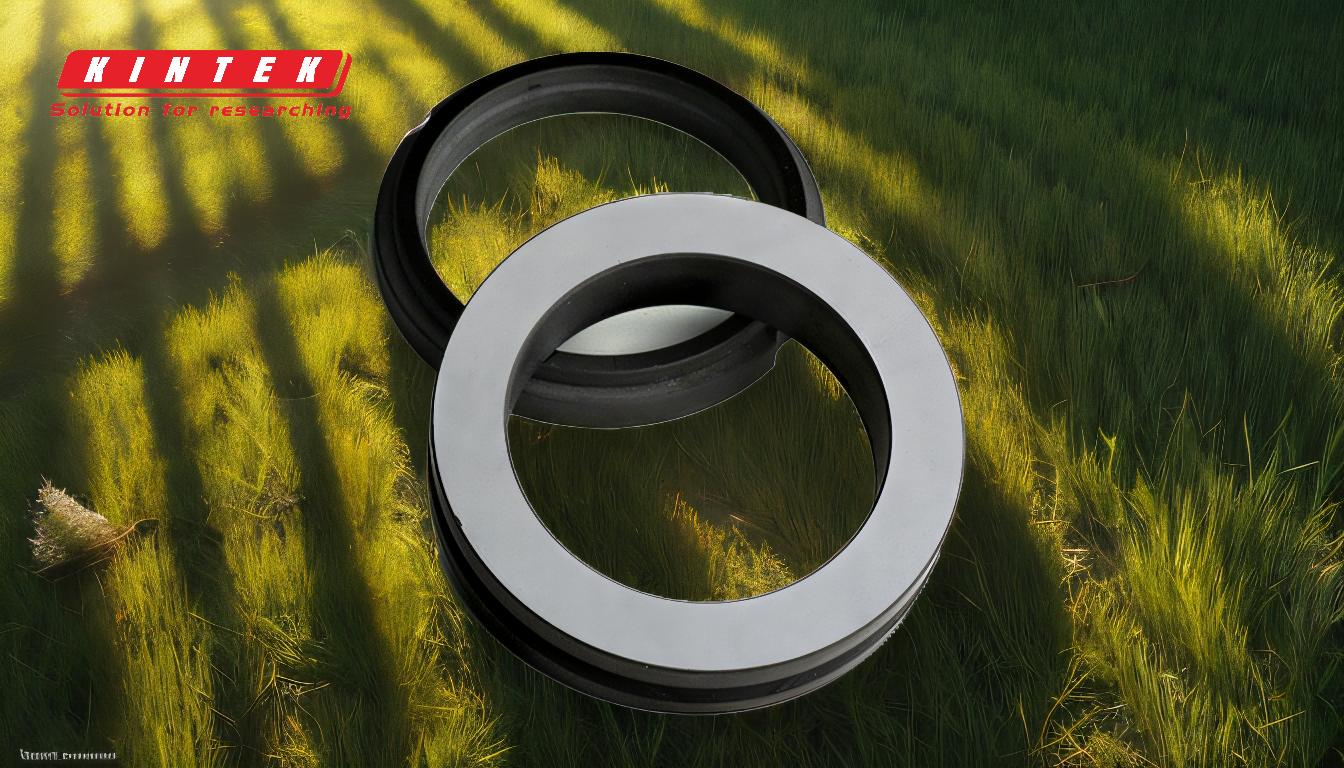
-
Wear-Protective Applications:
- DLC coatings are extensively used to protect components from wear and tear in demanding environments. For example:
- Optical Components: DLC coatings are applied to lenses and mirrors to prevent scratches and abrasions, ensuring long-term optical clarity.
- Magnetic Memory Discs: These coatings protect data storage devices from mechanical damage, enhancing their lifespan.
- Metalworking Tools: DLC coatings improve the durability of cutting tools, drills, and molds by reducing wear and friction during machining processes.
- Biomedical Prostheses: DLC coatings are biocompatible and resistant to corrosion, making them ideal for implants and surgical instruments.
- DLC coatings are extensively used to protect components from wear and tear in demanding environments. For example:
-
Low-Temperature Deposition and Adhesion:
- DLC coatings can be deposited at relatively low temperatures (around 300 °C), making them suitable for temperature-sensitive substrates.
- Adhesion is critical for the performance of DLC coatings. Silicon-based films are often predeposited using plasma-assisted chemical vapor deposition (PACVD) to enhance bonding with steel and hard metal substrates.
-
Low Coefficient of Friction (COF):
- DLC coatings exhibit a low COF, making them ideal for applications requiring reduced friction and energy efficiency. Examples include:
- Automotive Components: DLC coatings are used in power trains, bearings, and camshafts to reduce energy losses and improve fuel efficiency.
- Machinery: Components like gears and sliders benefit from DLC coatings, which minimize wear and extend operational life.
- DLC coatings exhibit a low COF, making them ideal for applications requiring reduced friction and energy efficiency. Examples include:
-
High Hardness and Chemical Resistance:
- DLC coatings have a hardness range of 1500–3000 HV, making them highly resistant to abrasion and deformation.
- Their chemical resistance makes them suitable for use in harsh environments, such as in chemical processing equipment or marine applications.
-
Optical and Sensing Applications:
- DLC coatings are used in optical systems due to their low roughness and precise control over thickness and refractive index. Applications include:
- Antireflective Coatings: These coatings reduce glare and improve light transmission in optical devices.
- Optical Sensors: DLC films are used in sensing applications where precise optical properties are required.
- DLC coatings are used in optical systems due to their low roughness and precise control over thickness and refractive index. Applications include:
-
Biocompatibility and Biomedical Applications:
- DLC coatings are biocompatible, meaning they are safe for use in the human body. This property makes them suitable for:
- Medical Implants: Coatings on implants reduce wear and prevent adverse reactions with bodily tissues.
- Surgical Instruments: DLC coatings enhance the durability and performance of tools used in medical procedures.
- DLC coatings are biocompatible, meaning they are safe for use in the human body. This property makes them suitable for:
-
Decorative and Functional Applications in Luxury Goods:
- DLC coatings are used in luxury items like watches to combine functionality with aesthetics. The coatings provide:
- Enhanced Durability: Scratch resistance and wear protection.
- Luxurious Appearance: A sleek, black finish that is both decorative and functional.
- DLC coatings are used in luxury items like watches to combine functionality with aesthetics. The coatings provide:
-
Process of DLC Coating:
- The DLC coating process involves the use of hydrocarbons, which are ionized to form plasma. The carbon and hydrogen atoms recombine on the substrate surface, creating a hard, durable coating. This process ensures uniformity and strong adhesion to the substrate.
-
Energy-Saving and Environmental Benefits:
- By reducing friction and wear, DLC coatings contribute to energy savings in mechanical systems, such as automotive engines and industrial machinery. This not only improves efficiency but also reduces environmental impact by lowering energy consumption and extending the life of components.
-
Versatility Across Industries:
- The unique properties of DLC coatings make them suitable for a wide range of applications, from industrial machinery to consumer electronics and medical devices. Their adaptability and performance benefits ensure their continued use in both functional and decorative roles.
In summary, DLC coatings are a critical technology in modern engineering and manufacturing, offering solutions for wear protection, friction reduction, and performance enhancement across diverse industries. Their ability to combine hardness, low friction, and biocompatibility with precise deposition techniques makes them indispensable in both functional and aesthetic applications.
Summary Table:
Property | Benefits |
---|---|
Wear Resistance | Protects components from abrasion, scratches, and mechanical damage. |
Low Friction | Reduces energy losses and improves efficiency in automotive and machinery. |
Chemical Resistance | Suitable for harsh environments like chemical processing and marine applications. |
Biocompatibility | Safe for medical implants and surgical instruments. |
Low-Temperature Deposition | Compatible with temperature-sensitive substrates. |
Optical Properties | Enhances light transmission and reduces glare in optical devices. |
Decorative Applications | Combines durability with a sleek, luxurious finish for luxury goods. |
Unlock the potential of DLC coatings for your industry—contact our experts today to learn more!