Microwave sintering is a cutting-edge technology with diverse applications in advanced material preparation. It leverages microwave energy to achieve uniform heating, low-temperature sintering, and rapid processing, making it highly efficient and cost-effective. This method is particularly advantageous for producing ceramic materials, optical fiber components, ferrites, superconducting materials, lithium hydride, and nanomaterials. Its ability to scale for larger volumes and improve mechanical properties makes it a promising solution for industries requiring high-performance materials. However, challenges like equipment cooling are addressed through auxiliary systems, ensuring operational efficiency.
Key Points Explained:
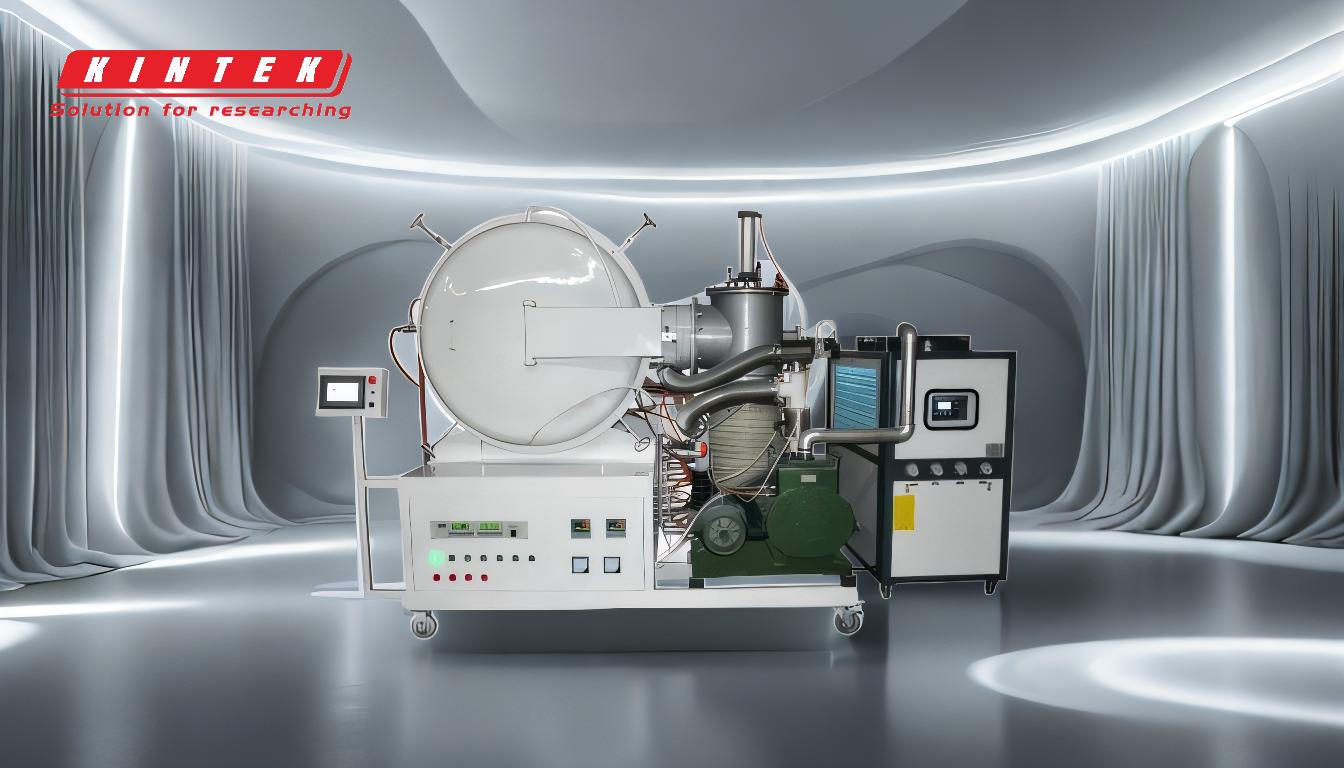
-
Applications in Ceramic Material Preparation:
- Microwave sintering is widely used for preparing sub-meter or even micron-level ceramic materials.
- It ensures uniform heating with a small internal temperature gradient, enabling low-temperature and rapid sintering.
- This method enhances the mechanical properties of ceramics, making it ideal for advanced ceramic applications.
-
Production of Optical Fiber Materials:
- Microwave sintering is employed to produce original components of optical fiber materials.
- The uniform heating and rapid sintering process ensure high-quality optical fiber components with improved performance.
-
Ferrite and Superconducting Material Production:
- This technology is used in the production of ferrites and superconducting materials.
- The efficient energy transfer and low-temperature sintering improve the magnetic and electrical properties of these materials.
-
Lithium Hydride and Nanomaterial Synthesis:
- Microwave sintering is applied in the synthesis of lithium hydride and nanomaterials.
- The rapid and uniform heating process ensures precise control over material properties, making it suitable for advanced applications.
-
High-Speed Sintering and Scalability:
- Microwave sintering is known for its high-speed sintering capabilities.
- It can be scaled for larger volume production, making it a viable option for industrial applications.
-
Energy Efficiency and Cost-Effectiveness:
- The technology does not require a heat source, reducing energy consumption and unit costs.
- Its high production efficiency makes it a cost-effective solution for material preparation.
-
Challenges and Solutions:
- Cooling the operating equipment can be a challenge due to the high-speed sintering process.
- Auxiliary cooling systems are employed to address this issue, ensuring smooth operation and equipment longevity.
-
Future Prospects:
- Microwave sintering has broad application prospects in advanced material preparation.
- Its ability to produce high-performance materials with improved properties positions it as a promising technology for future innovations.
In summary, microwave sintering is a versatile and efficient technology with significant applications in advanced material preparation. Its ability to enhance material properties, reduce costs, and scale for industrial production makes it a valuable tool for various industries.
Summary Table:
Key Benefits | Applications | Challenges & Solutions |
---|---|---|
Uniform heating & low-temperature sintering | Ceramic materials, optical fibers, ferrites | Cooling systems for high-speed sintering |
Rapid processing & scalability | Superconducting materials, lithium hydride | Auxiliary cooling ensures efficiency |
Energy-efficient & cost-effective | Nanomaterials, industrial-scale production | Improved mechanical properties |
Unlock the potential of microwave sintering for your material preparation needs—contact our experts today!