Physical Vapor Deposition (PVD) coating is a versatile and advanced surface treatment technology with a wide range of applications across various industries. It is primarily used to enhance the durability, wear resistance, and corrosion resistance of tools, machinery, and components. Additionally, PVD coatings are valued for their aesthetic appeal, environmental safety, and ability to work with a variety of materials, including metals, ceramics, and composites. Key industries benefiting from PVD coatings include aerospace, automotive, semiconductor manufacturing, telecommunications, and lighting. The technology is also preferred for its precision and eco-friendliness compared to traditional chemical-based coating methods.
Key Points Explained:
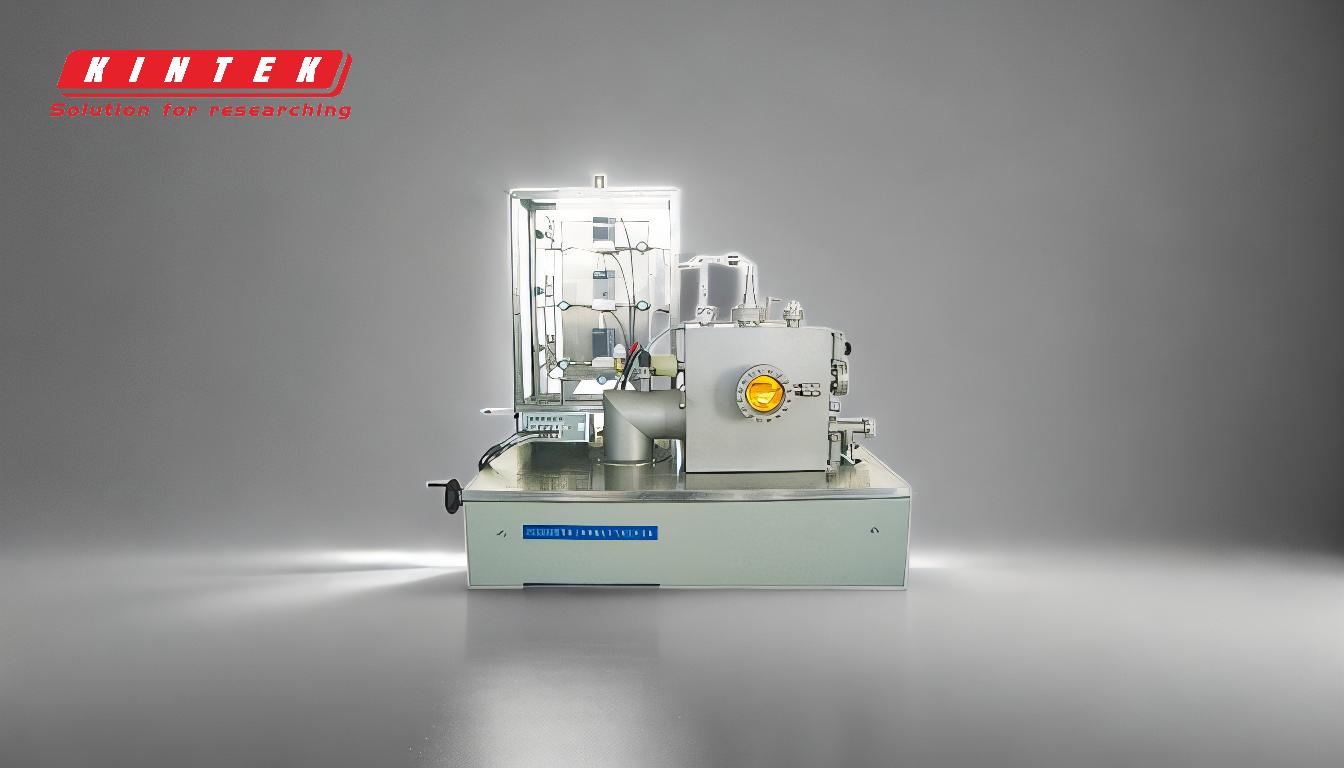
-
Corrosion and Wear Resistance in Aerospace and Automotive Industries
- PVD coatings are extensively used in aerospace and automotive sectors to protect metal parts from wear and corrosion.
- The coatings improve the lifespan and performance of engine components, cutting tools, and other high-stress parts.
- Materials like graphite, titanium, and specialized coatings such as carbides and nitrides are commonly used for high-performance applications.
-
Aesthetic Applications in Automotive and Telecommunications
- PVD coatings provide vibrant colors and finishes, making them ideal for enhancing the visual appeal of automotive interiors, motorcycle trims, and consumer electronics.
- The ability to incorporate precious metals or look-alike materials allows for high-end, customizable designs.
-
Semiconductor Manufacturing
- In semiconductor production, PVD techniques like sputtering are used to deposit thin films of metals such as platinum, tungsten, and copper onto microchips.
- The technology is also employed in creating thin-film photovoltaic cells, where materials like copper, indium, gallium, and tellurium are coated onto glass or plastic substrates.
-
Lighting Applications
- PVD coatings are used in lighting for both aesthetic and functional purposes.
- They enable precise color customization and improve the durability of lighting devices, making them resistant to environmental conditions.
-
Environmental and Safety Benefits
- PVD coating is safer and more environmentally friendly than chemical-based methods, as it reduces the need for toxic substances and minimizes waste.
- The molecular-scale application ensures a superior finish with minimal environmental impact.
-
Versatility Across Industries
- PVD coatings are applicable to almost any inorganic material, making them suitable for a wide range of industries, including defense, construction, and cutting tools.
- The technology's ability to reduce friction and enhance durability makes it a preferred choice for high-performance applications.
In summary, PVD coating is a highly adaptable and efficient technology that offers significant benefits in terms of durability, aesthetics, and environmental sustainability. Its applications span across critical industries, making it an indispensable tool for modern manufacturing and design.
Summary Table:
Industry | Applications | Key Benefits |
---|---|---|
Aerospace & Automotive | Corrosion and wear resistance for engine components, cutting tools, and parts | Improved lifespan, high-performance materials like titanium and carbides |
Automotive & Electronics | Aesthetic finishes for interiors, trims, and consumer electronics | Vibrant colors, customizable designs with precious metals |
Semiconductor Manufacturing | Thin-film deposition for microchips and photovoltaic cells | Precision coating with metals like platinum, tungsten, and copper |
Lighting | Aesthetic and functional coatings for lighting devices | Color customization, durability in harsh environments |
Environmental & Safety | Eco-friendly alternative to chemical-based coatings | Reduced toxic substances, minimal waste, superior finish |
Versatility | Applicable to metals, ceramics, and composites across industries | Enhanced durability, reduced friction, and high-performance applications |
Unlock the potential of PVD coating for your industry—contact our experts today to learn more!