PVD (Physical Vapor Deposition) thin films have a wide range of applications across various industries due to their unique properties such as high durability, corrosion resistance, and ability to enhance surface performance. These films are used in the construction of microchips, semiconductor devices, durable protective layers, optical lenses, solar panels, and medical devices. Additionally, they are critical in industries like aerospace, defense, automotive, and cutting tools, where reducing friction and increasing durability are essential. PVD coatings are also environmentally friendly and can be applied to strong materials like stainless steel and titanium, making them versatile for high-performance applications.
Key Points Explained:
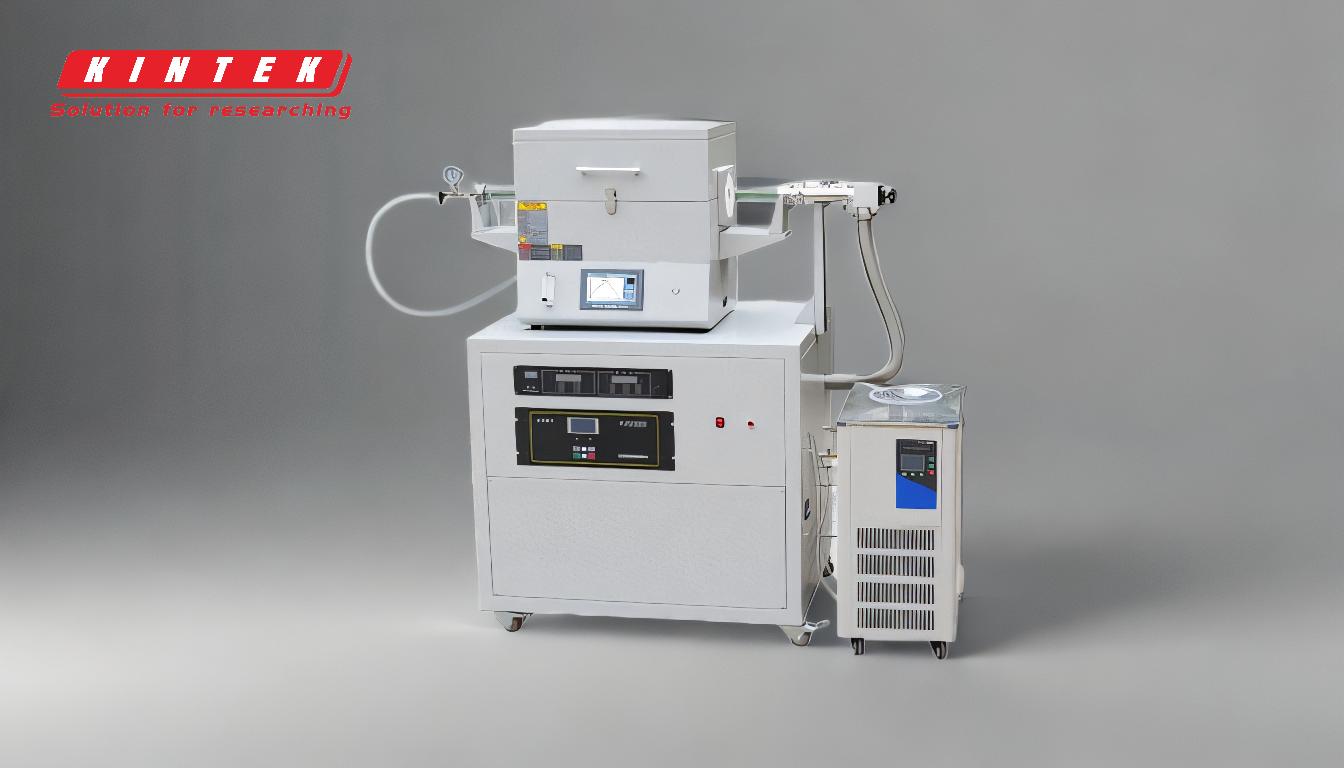
-
Microelectronics and Semiconductors:
- PVD thin films are integral in the production of microchips and semiconductor devices. They provide conductive and insulating layers that are essential for the functionality of electronic components.
- The precision and uniformity of PVD coatings ensure high performance and reliability in microelectronic devices, which are critical for modern technology.
-
Durable Protective Coatings:
- PVD coatings are widely used to create durable protective layers on various materials. These coatings enhance the wear resistance, corrosion resistance, and overall durability of the substrate.
- Applications include protective layers on cutting tools, automotive parts, and aerospace components, where longevity and performance under extreme conditions are crucial.
-
Optical Applications:
- PVD thin films are used in the production of optical lenses and mirrors. They provide anti-reflective, reflective, and protective coatings that improve the performance and lifespan of optical components.
- These coatings are essential in industries such as photography, microscopy, and laser technology, where precision and clarity are paramount.
-
Solar Panels and Renewable Energy:
- PVD coatings are applied in the manufacturing of solar panels to enhance their efficiency and durability. These coatings help in improving light absorption and reducing reflection, thereby increasing the overall energy output.
- The use of PVD in renewable energy applications supports the development of sustainable energy solutions.
-
Medical Devices:
- PVD thin films are used in medical devices to provide biocompatible and wear-resistant coatings. These coatings are essential for devices such as surgical instruments, implants, and diagnostic equipment.
- The biocompatibility and durability of PVD coatings ensure the safety and longevity of medical devices, which is critical for patient care.
-
Aerospace and Defense:
- In the aerospace and defense industries, PVD coatings are used to enhance the performance and durability of components exposed to extreme conditions. These coatings provide resistance to high temperatures, corrosion, and wear.
- Applications include coatings on turbine blades, engine components, and military equipment, where reliability and performance are critical.
-
Automotive Industry:
- PVD coatings are used in the automotive industry to improve the durability and performance of various components. These coatings reduce friction, enhance wear resistance, and provide corrosion protection.
- Applications include coatings on engine parts, transmission components, and decorative finishes, contributing to the overall efficiency and aesthetics of vehicles.
-
Cutting Tools and Industrial Applications:
- PVD coatings are extensively used on cutting tools to enhance their hardness, wear resistance, and performance. These coatings extend the life of tools and improve machining efficiency.
- Industrial applications also include coatings on molds, dies, and other machinery components, where durability and performance are essential.
-
Energy Generation and Data Storage:
- PVD thin films are used in energy generation applications, such as coatings on fuel cells and batteries, to enhance their performance and efficiency.
- In data storage, PVD coatings are used to create thin films on hard drives and other storage media, improving data density and reliability.
-
Environmental and Economic Benefits:
- PVD is an environmentally sound process that reduces the need for hazardous chemicals and produces minimal waste. This makes it a sustainable choice for various industrial applications.
- The economic benefits of PVD coatings include extended product life, reduced maintenance costs, and improved performance, making them a cost-effective solution for many industries.
In summary, PVD thin films are versatile and essential in a wide range of applications across multiple industries. Their ability to enhance durability, performance, and efficiency makes them a critical component in modern manufacturing and technology.
Summary Table:
Industry | Applications | Key Benefits |
---|---|---|
Microelectronics | Microchips, semiconductor devices | Precision, uniformity, high performance |
Durable Protective Coatings | Cutting tools, automotive parts, aerospace components | Wear resistance, corrosion resistance, durability |
Optical Applications | Lenses, mirrors, laser technology | Anti-reflective, reflective, protective coatings |
Solar Panels | Renewable energy solutions | Improved light absorption, reduced reflection, enhanced efficiency |
Medical Devices | Surgical instruments, implants, diagnostic equipment | Biocompatibility, wear resistance, safety |
Aerospace & Defense | Turbine blades, engine components, military equipment | High-temperature resistance, corrosion resistance, reliability |
Automotive | Engine parts, transmission components, decorative finishes | Friction reduction, wear resistance, corrosion protection |
Cutting Tools | Industrial machinery, molds, dies | Hardness, wear resistance, extended tool life |
Energy Generation | Fuel cells, batteries | Enhanced performance, efficiency |
Data Storage | Hard drives, storage media | Improved data density, reliability |
Environmental Benefits | Sustainable industrial processes | Reduced hazardous chemicals, minimal waste, cost-effectiveness |
Unlock the potential of PVD thin films for your industry—contact us today to learn more!