Spark plasma sintering (SPS) is an advanced powder metallurgy technique that combines high-pressure and pulsed electric current to achieve rapid densification of materials at relatively low temperatures. This method is widely used in various fields due to its ability to produce high-density, fine-grained materials with enhanced mechanical, thermal, and electrical properties. Applications of SPS span across industries such as aerospace, automotive, electronics, biomedical, and energy, where the demand for high-performance materials is critical.
Key Points Explained:
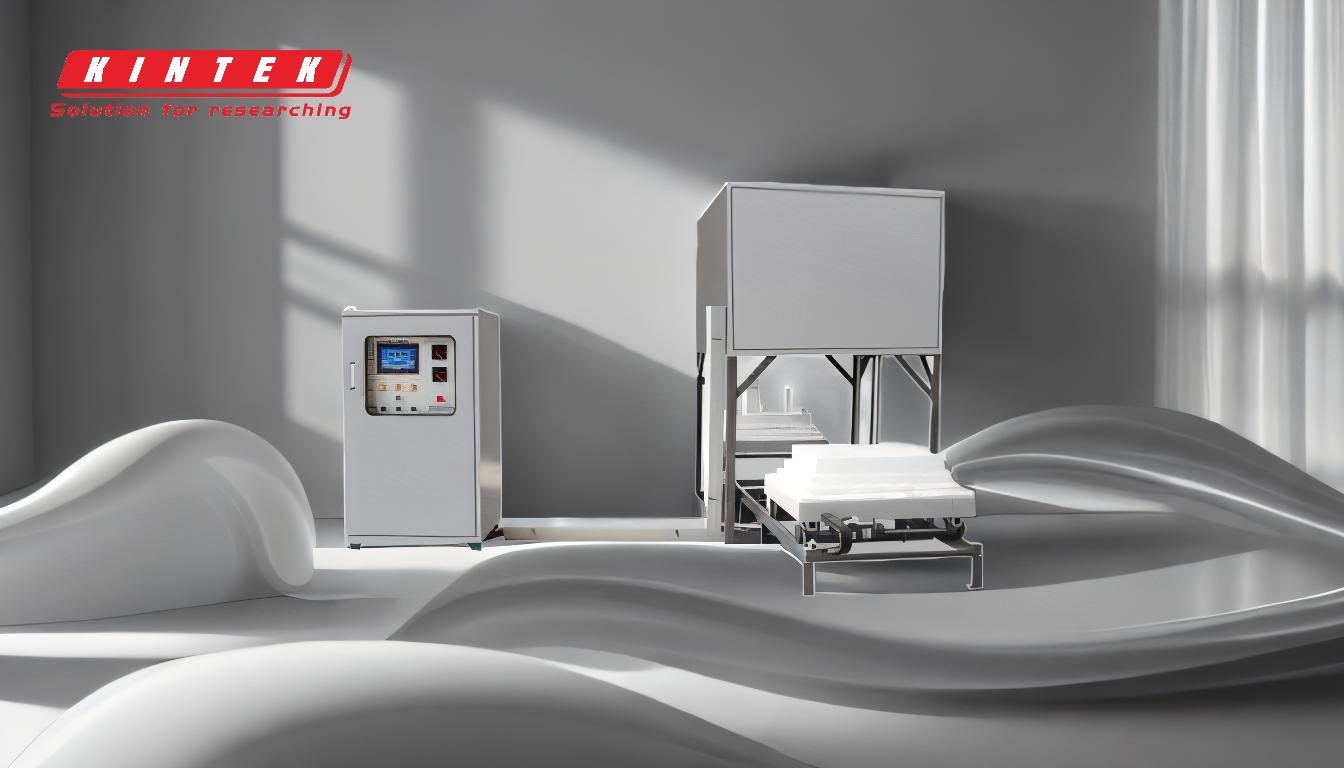
-
Aerospace Industry:
- SPS is used to fabricate lightweight, high-strength materials such as titanium alloys, ceramic matrix composites, and intermetallic compounds. These materials are essential for components like turbine blades, engine parts, and structural elements, where high temperature resistance and mechanical strength are paramount.
- The rapid sintering process minimizes grain growth, resulting in materials with superior mechanical properties and fatigue resistance, which are crucial for aerospace applications.
-
Automotive Industry:
- In the automotive sector, SPS is employed to produce advanced materials such as aluminum-based composites, silicon carbide ceramics, and high-entropy alloys. These materials are used in engine components, brake systems, and lightweight structural parts, contributing to improved fuel efficiency and performance.
- The ability to sinter materials at lower temperatures reduces energy consumption and enhances the sustainability of manufacturing processes.
-
Electronics and Semiconductors:
- SPS is utilized to manufacture materials with tailored electrical and thermal properties, such as thermoelectric materials, conductive ceramics, and high-performance insulators. These materials are critical for electronic devices, sensors, and energy storage systems.
- The precise control over microstructure and density achieved through SPS ensures optimal performance of electronic components, enabling advancements in miniaturization and efficiency.
-
Biomedical Applications:
- SPS is applied in the production of biocompatible materials such as hydroxyapatite, zirconia, and titanium alloys for dental implants, bone scaffolds, and prosthetics. The high density and fine-grained structure of SPS-processed materials enhance their mechanical strength and biocompatibility.
- The ability to incorporate bioactive coatings and functional gradients during sintering further improves the integration and performance of biomedical implants.
-
Energy Sector:
- SPS is used to fabricate materials for energy storage and conversion, including solid oxide fuel cells, thermoelectric generators, and supercapacitors. The rapid densification process ensures high ionic and electronic conductivity, which is essential for efficient energy conversion and storage.
- The technique is also employed in the production of advanced nuclear materials, such as uranium dioxide and thorium-based fuels, where high density and thermal stability are critical.
-
Research and Development:
- SPS is a valuable tool in material science research, enabling the synthesis of novel materials with unique properties. Researchers use SPS to explore new alloys, composites, and nanostructured materials, pushing the boundaries of material performance.
- The ability to rapidly prototype and test materials with SPS accelerates the development of innovative solutions for various industrial challenges.
In summary, spark plasma sintering is a versatile and powerful technique with applications across multiple industries. Its ability to produce high-performance materials with tailored properties makes it an indispensable tool in modern manufacturing and research.
Summary Table:
Industry | Applications |
---|---|
Aerospace | Lightweight, high-strength materials for turbine blades, engine parts, and structural elements. |
Automotive | Advanced materials for engine components, brake systems, and lightweight structural parts. |
Electronics | Tailored electrical and thermal materials for sensors, devices, and energy storage systems. |
Biomedical | Biocompatible materials for dental implants, bone scaffolds, and prosthetics. |
Energy | Materials for solid oxide fuel cells, thermoelectric generators, and nuclear fuels. |
Research | Synthesis of novel alloys, composites, and nanostructured materials for innovative solutions. |
Unlock the potential of spark plasma sintering for your industry—contact our experts today!