Vapor deposition is a versatile and widely used technique in various industries for creating thin films and coatings on substrates. This process involves the deposition of material in a vaporized form onto a surface, resulting in high-quality, uniform layers with precise thickness control. The applications of vapor deposition span across electronics, optics, aerospace, automotive, and biomedical fields. It is used for creating semiconductor devices, optical coatings, protective layers, and even biocompatible implants. The ability to deposit materials at the atomic or molecular level makes vapor deposition a critical technology in modern manufacturing and research.
Key Points Explained:
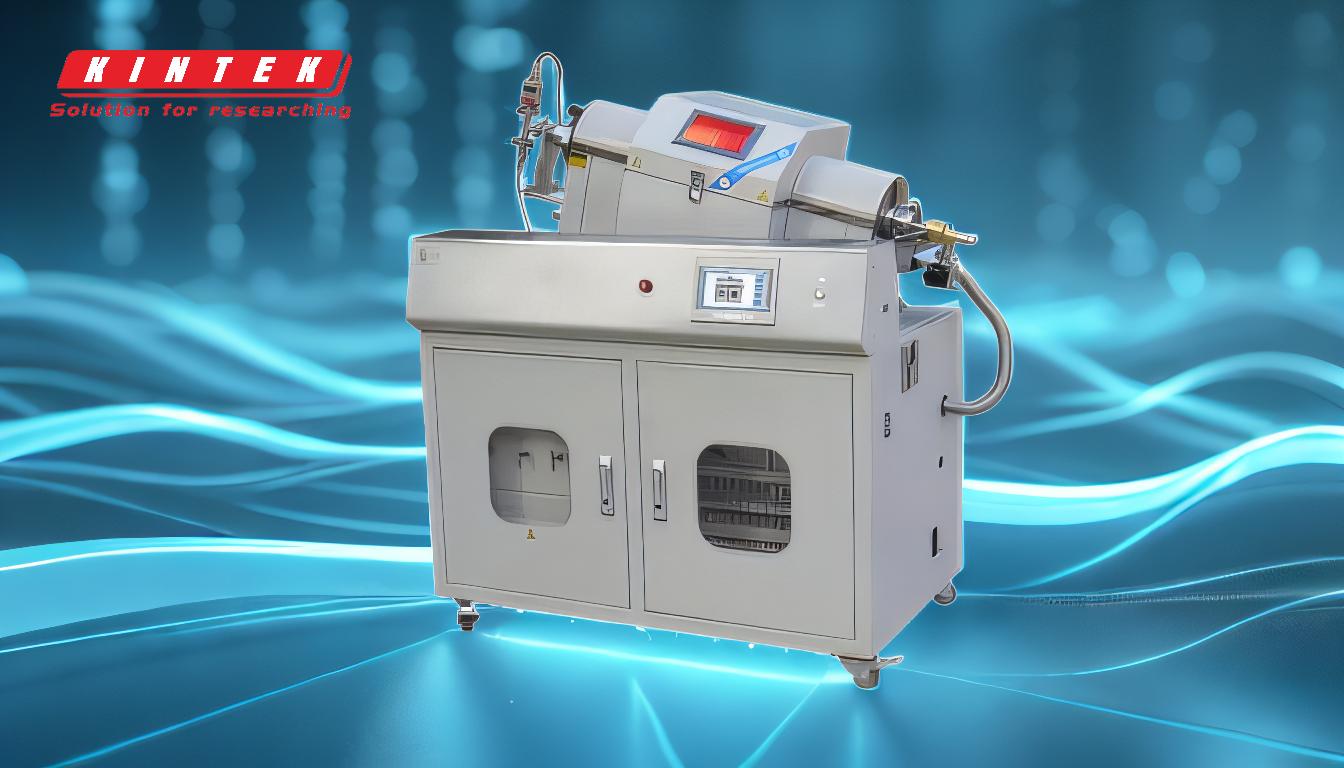
-
Electronics and Semiconductor Industry:
- Vapor deposition is extensively used in the fabrication of semiconductor devices, such as integrated circuits, transistors, and solar cells. Techniques like Chemical Vapor Deposition (CVD) and Physical Vapor Deposition (PVD) are employed to deposit thin films of silicon, silicon dioxide, and other semiconductor materials.
- These thin films are crucial for the miniaturization and performance enhancement of electronic components. For example, CVD is used to grow high-quality silicon layers for microprocessors, while PVD is used for depositing metal layers in interconnects.
-
Optical Coatings:
- Vapor deposition is used to create anti-reflective, reflective, and protective coatings on optical components such as lenses, mirrors, and filters. These coatings improve the performance of optical systems by enhancing light transmission, reducing glare, and increasing durability.
- For instance, PVD is commonly used to deposit thin films of materials like titanium dioxide and silicon dioxide on lenses to create anti-reflective coatings, which are essential for high-quality imaging systems.
-
Aerospace and Automotive Industries:
- In aerospace and automotive applications, vapor deposition is used to apply protective coatings that enhance the durability and performance of components. These coatings can provide resistance to wear, corrosion, and high temperatures.
- For example, PVD is used to deposit hard coatings like titanium nitride on turbine blades and engine components, which significantly extends their lifespan and improves efficiency.
-
Biomedical Applications:
- Vapor deposition is used in the biomedical field to create biocompatible coatings on implants and medical devices. These coatings can improve the integration of implants with biological tissues and reduce the risk of rejection or infection.
- For instance, CVD is used to deposit diamond-like carbon (DLC) coatings on surgical instruments and implants, providing a combination of hardness, wear resistance, and biocompatibility.
-
Energy Sector:
- Vapor deposition plays a crucial role in the development of energy-related technologies, such as thin-film solar cells, fuel cells, and batteries. These applications rely on the precise deposition of materials to achieve high efficiency and performance.
- For example, CVD is used to deposit thin films of materials like cadmium telluride and copper indium gallium selenide in thin-film solar cells, which are more cost-effective and flexible than traditional silicon-based solar cells.
-
Decorative and Functional Coatings:
- Vapor deposition is also used for decorative purposes, such as applying metallic or colored coatings on consumer products like watches, jewelry, and electronics. These coatings not only enhance the aesthetic appeal but also provide functional benefits like scratch resistance.
- For example, PVD is used to deposit thin films of gold, titanium, or chromium on watch cases and smartphone bodies, giving them a premium finish while also improving durability.
-
Research and Development:
- Vapor deposition is a key tool in materials science research, enabling the development of new materials with unique properties. Researchers use vapor deposition to explore the properties of thin films, nanostructures, and composite materials.
- For instance, CVD is used to grow graphene, a single layer of carbon atoms with exceptional electrical, thermal, and mechanical properties, which has potential applications in electronics, sensors, and energy storage.
In conclusion, vapor deposition is a critical technology with a wide range of applications across multiple industries. Its ability to create high-quality, precise thin films and coatings makes it indispensable in modern manufacturing and research. Whether it's enhancing the performance of electronic devices, improving the durability of aerospace components, or enabling the development of new materials, vapor deposition continues to play a vital role in advancing technology and innovation.
Summary Table:
Industry | Applications |
---|---|
Electronics & Semiconductors | Fabrication of integrated circuits, transistors, and solar cells. |
Optical Coatings | Anti-reflective, reflective, and protective coatings on lenses and mirrors. |
Aerospace & Automotive | Protective coatings for wear, corrosion, and high-temperature resistance. |
Biomedical | Biocompatible coatings on implants and surgical instruments. |
Energy Sector | Thin-film solar cells, fuel cells, and batteries for energy efficiency. |
Decorative & Functional | Metallic or colored coatings on watches, jewelry, and electronics. |
Research & Development | Development of new materials like graphene and nanostructures. |
Learn how vapor deposition can transform your industry—contact our experts today!