Heat treatment furnaces utilize various atmospheres to achieve specific material properties during processes like annealing, carburizing, and oxidation. These atmospheres include gases such as carbon, nitrogen, argon, and carbon dioxide, each serving a unique purpose in enhancing material characteristics. For instance, carbon is used for carburizing finishes, nitrogen aids in annealing, argon improves annealing processes, and carbon dioxide provides strong oxygenation properties. These controlled environments ensure uniform heating, precise temperature control, and consistent cooling rates, which are critical for achieving desired material properties. In industries like aerospace and defense, these furnaces are essential for manufacturing components with high-temperature resistance and structural integrity.
Key Points Explained:
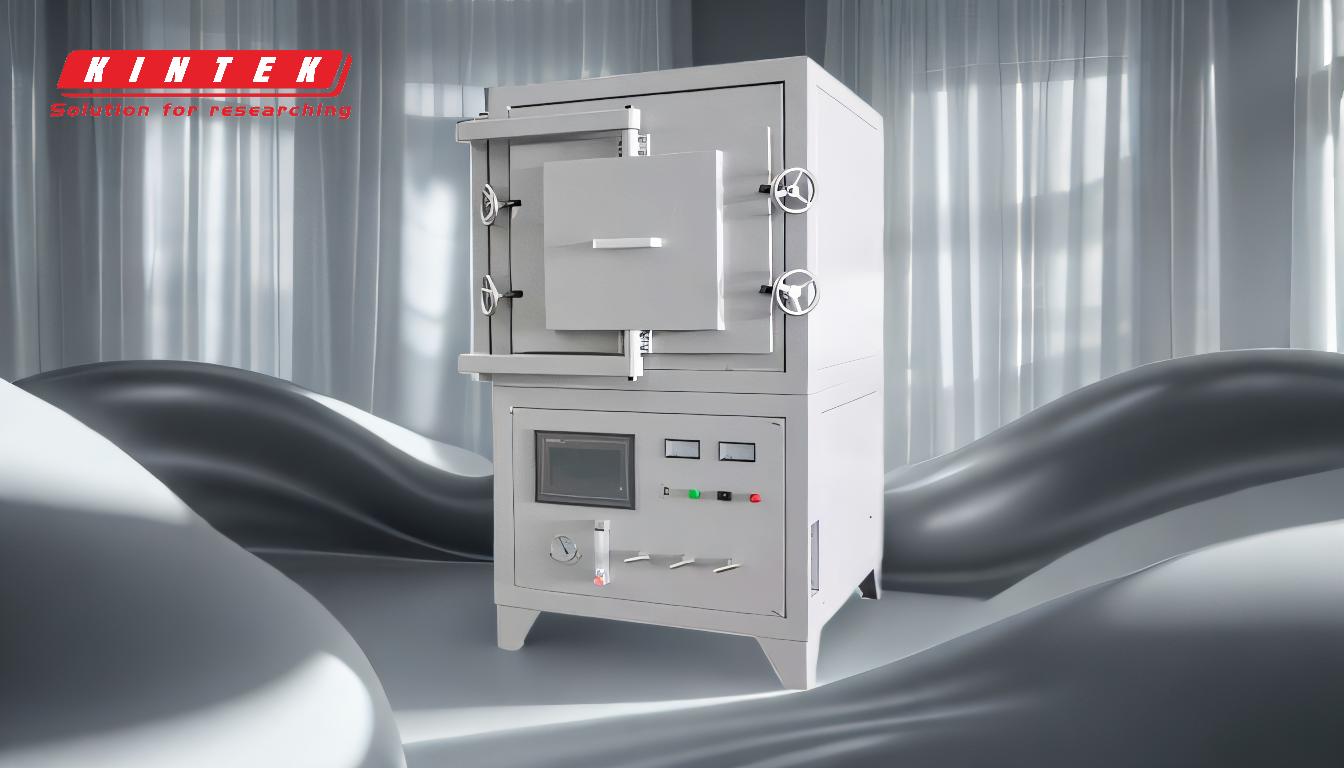
-
Role of Atmospheres in Heat Treatment Furnaces:
- Heat treatment furnaces rely on specific gaseous atmospheres to achieve precise material properties. These atmospheres are tailored to the requirements of processes like carburizing, annealing, and oxidation.
- The controlled environment ensures uniform heating, accurate temperature regulation, and consistent cooling, which are vital for achieving desired material characteristics.
-
Types of Gaseous Mediums:
- Carbon: Used primarily in carburizing processes to introduce carbon into the surface of steel, enhancing hardness and wear resistance.
- Nitrogen: Augments the annealing process by preventing oxidation and decarburization, ensuring the material retains its desired properties.
- Argon: An inert gas that improves annealing by creating a non-reactive environment, preventing contamination and oxidation.
- Carbon Dioxide: Provides strong oxygenation properties, aiding in oxidation processes where controlled surface reactions are required.
-
Importance of Controlled Atmospheres:
- Controlled atmospheres in heat treatment furnaces ensure that materials achieve specific mechanical and chemical properties.
- These environments are critical for processes like annealing, where precise control prevents unwanted reactions and ensures uniformity.
-
Applications in Aerospace and Defense:
- In industries such as aerospace and defense, atmosphere furnaces are indispensable for manufacturing critical components like aircraft engine parts, turbines, rocket components, and armor plating.
- The precise control of atmospheres ensures that these components exhibit high-temperature resistance, structural integrity, and other necessary properties.
-
Benefits of Using Specific Atmospheres:
- Uniform Heating: Ensures consistent material properties throughout the component.
- Precise Temperature Control: Allows for accurate execution of heat treatment processes.
- Controlled Cooling Rates: Prevents defects like cracking or warping, ensuring the material retains its desired shape and properties.
By understanding the specific roles of different atmospheres and their applications, manufacturers can optimize heat treatment processes to meet the stringent requirements of various industries.
Summary Table:
Atmosphere | Purpose | Key Benefits |
---|---|---|
Carbon | Carburizing | Enhances hardness and wear resistance |
Nitrogen | Annealing | Prevents oxidation and decarburization |
Argon | Annealing | Creates a non-reactive, contamination-free environment |
Carbon Dioxide | Oxidation | Provides strong oxygenation properties |
Need the right atmosphere for your heat treatment process? Contact our experts today to optimize your furnace performance!