Electric arc furnaces (EAFs) are a critical technology in modern steelmaking, primarily used for recycling scrap metal into new steel products. They operate by generating intense heat through electric arcs, which melt the metal. EAFs are energy-efficient, environmentally friendly, and versatile, making them a preferred choice for producing carbon and alloy steels. The process involves key components like electrodes, a tilting mechanism, and a fume extraction system, and follows a structured workflow of charging, melting, and refining. This technology is widely adopted due to its ability to produce high-quality steel with minimal environmental impact.
Key Points Explained:
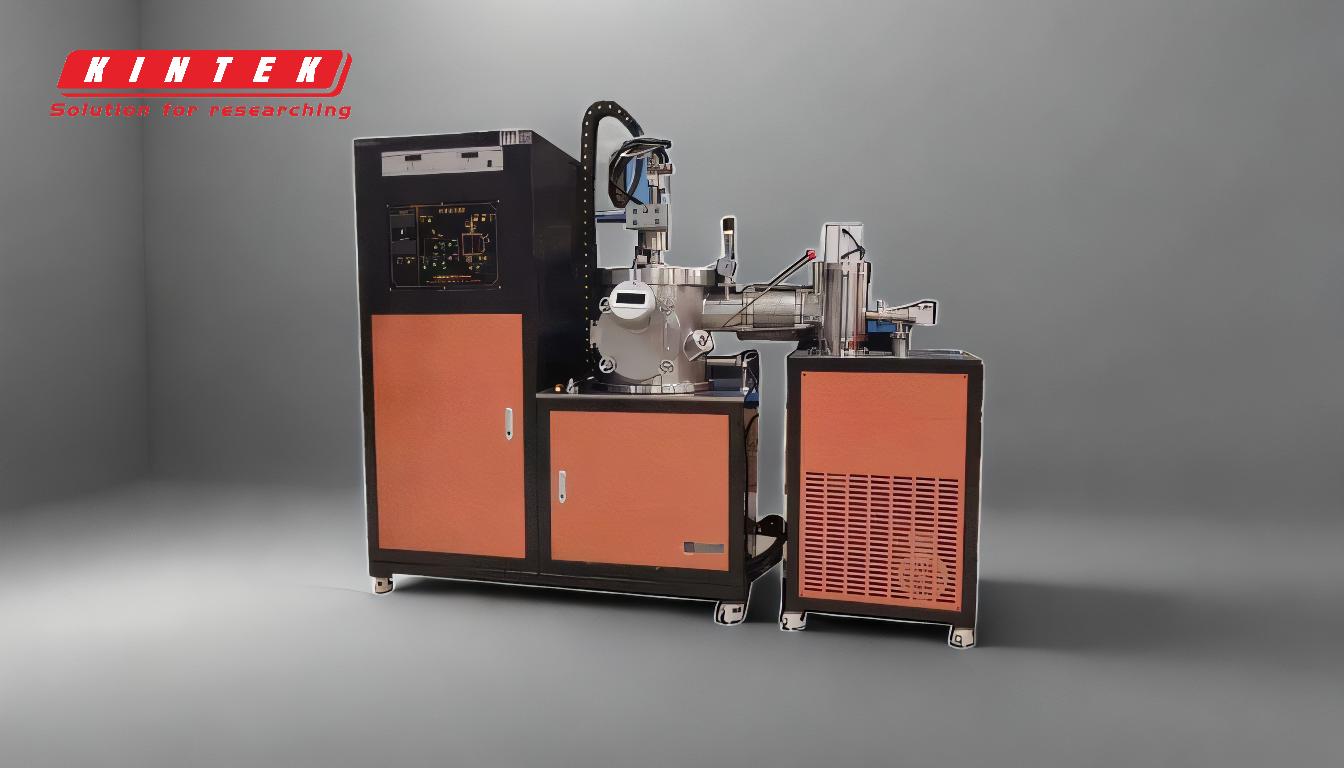
-
Basic Function and Purpose of Electric Arc Furnaces (EAFs):
- EAFs are used primarily for melting scrap metal to produce new steel, including carbon steel and alloy steel.
- They generate heat through electric arcs, which can reach temperatures up to 3275°F (1800°C), enabling rapid melting of materials.
- The process is highly efficient and environmentally friendly, as it recycles scrap metal and reduces the need for raw materials.
-
Key Components of an Electric Arc Furnace:
- Roof: Contains holes for electrode insertion and is constructed from refractory materials like alumina and magnesite-chromite bricks.
- Hearth: Holds the molten metal and slag, often lined with refractory materials to withstand high temperatures.
- Electrodes: Typically made of graphite or carbon, these are used to create the electric arc that generates heat.
- Tilting Mechanism: Allows the furnace to tilt for pouring molten metal.
- Fume Extraction System: Ensures operator safety by removing harmful gases and particulates generated during the melting process.
-
Working Principle of an EAF:
- Charging: Scrap metal is loaded into the furnace, often preheated using exhaust gases to improve energy efficiency.
- Meltdown Period: Electrodes are lowered onto the scrap, and an electric arc is formed, generating intense heat to melt the metal.
- Refining: Additives like burnt lime and spar are introduced to form slag, which helps remove impurities from the molten metal.
- Pouring: Once the metal is fully melted and refined, the furnace tilts to pour the molten metal into molds or ladles.
-
Energy Requirements and Efficiency:
- EAFs require approximately 350 to 370 kWh of energy to melt one ton of scrap metal.
- The use of electrical energy makes the process more controllable and efficient compared to traditional blast furnaces.
- Preheating scrap metal with exhaust gases further enhances energy efficiency.
-
Applications and Advantages:
- EAFs are widely used in the steel industry for producing carbon steel, alloy steel, and cast-iron products.
- They are particularly advantageous for recycling scrap metal, reducing the environmental impact of steel production.
- The ability to reach high temperatures quickly and control the melting process precisely makes EAFs suitable for producing high-quality steel.
-
Safety and Environmental Considerations:
- The fume extraction system is crucial for maintaining a safe working environment by removing harmful gases and particulates.
- EAFs produce fewer greenhouse gas emissions compared to traditional blast furnaces, contributing to more sustainable steel production.
- The use of scrap metal as the primary raw material reduces the need for mining and processing raw ores, further minimizing environmental impact.
-
Operational Workflow:
- Loading: Scrap metal is loaded into the furnace, often in a large basket.
- Preheating: Exhaust gases are used to preheat the scrap, improving energy efficiency.
- Melting: The electric arc generates heat to melt the scrap, with carbon, silicon, and manganese oxidizing during the process.
- Refining: Additives are introduced to form slag and remove impurities.
- Pouring: The furnace tilts to pour the molten metal into molds or ladles for further processing.
In summary, electric arc furnaces are a versatile and efficient technology for steel production, particularly for recycling scrap metal. Their ability to generate high temperatures quickly, combined with precise control over the melting process, makes them a preferred choice in the steel industry. The key components and operational workflow ensure safe, efficient, and environmentally friendly steel production.
Summary Table:
Key Aspect | Details |
---|---|
Primary Function | Melts scrap metal to produce carbon and alloy steel. |
Key Components | Roof, hearth, electrodes, tilting mechanism, fume extraction system. |
Working Principle | Charging, melting, refining, and pouring molten metal. |
Energy Efficiency | 350-370 kWh per ton of scrap; preheating enhances efficiency. |
Applications | Carbon steel, alloy steel, and cast-iron production. |
Environmental Benefits | Reduces greenhouse emissions and recycles scrap, minimizing raw material use. |
Ready to learn more about how electric arc furnaces can transform your steel production? Contact us today for expert guidance!