Physical Vapor Deposition (PVD) is a sophisticated coating process used to deposit thin films of material onto a substrate. The process involves converting a solid material into a vapor phase, transporting it through a vacuum or low-pressure environment, and then condensing it onto the substrate to form a thin, durable, and often functional coating. PVD is widely used in industries such as electronics, optics, and manufacturing for creating corrosion-resistant, wear-resistant, and decorative coatings. The process is carried out in a controlled environment, typically involving vacuum chambers, and employs methods like sputtering, evaporation, or arc discharge to achieve the desired coating properties.
Key Points Explained:
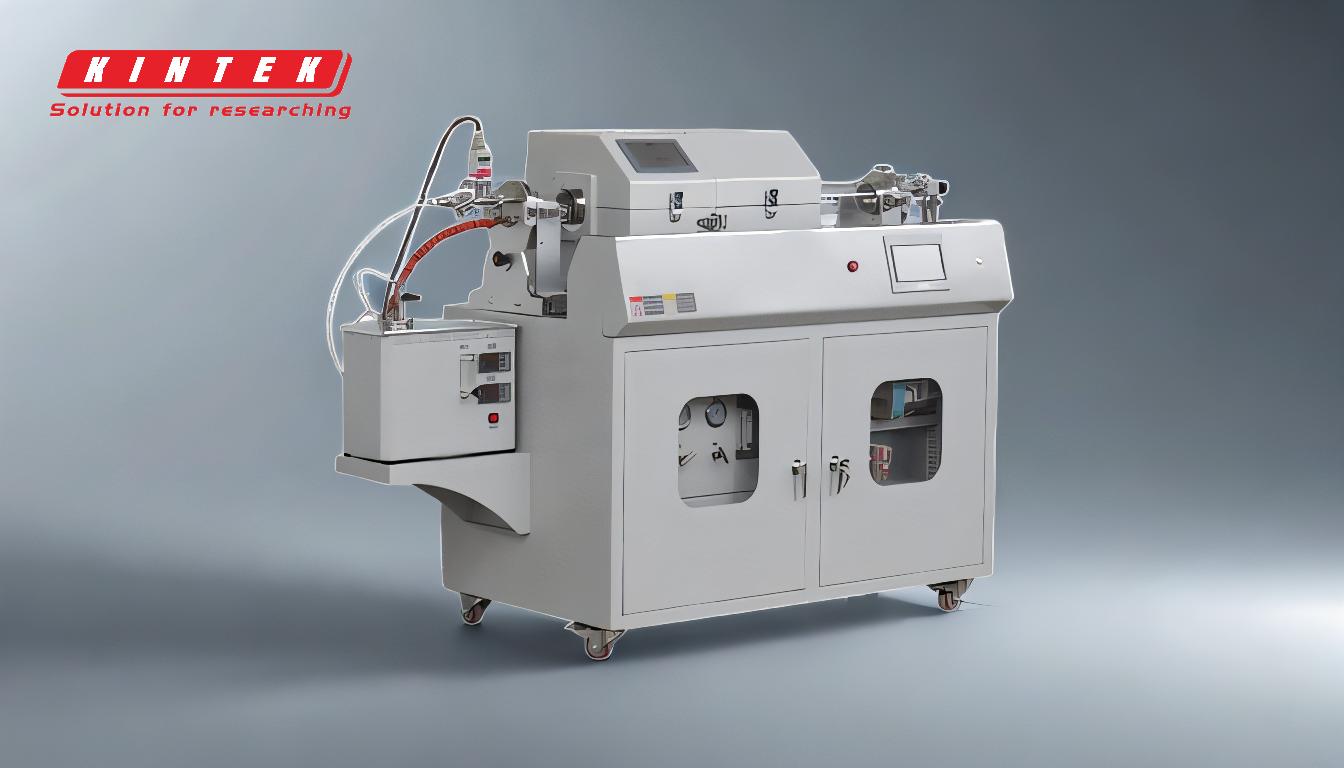
-
Gasification of the Plating Material:
- The first step in PVD involves converting the solid coating material (target) into a vapor phase. This is achieved through methods such as:
- Thermal Evaporation: Heating the material until it evaporates.
- Sputtering: Bombarding the target with high-energy ions to dislodge atoms.
- Arc Discharge: Using an electric arc to vaporize the material.
- Laser Beam or Electron Beam: Focused energy beams are used to vaporize the target material.
- The choice of method depends on the material properties and the desired coating characteristics.
- The first step in PVD involves converting the solid coating material (target) into a vapor phase. This is achieved through methods such as:
-
Migration of Plating Atoms, Molecules, or Ions:
- Once gasified, the atoms, molecules, or ions of the coating material travel through the reaction chamber. This step involves:
- Collisions and Reactions: The vaporized particles may collide with other particles or background gases, leading to reactions that can modify their properties.
- Line-of-Sight Deposition: The particles travel in a straight path and deposit onto the substrate, ensuring precise and controlled coating.
- The migration process is influenced by the vacuum level, temperature, and pressure within the chamber.
- Once gasified, the atoms, molecules, or ions of the coating material travel through the reaction chamber. This step involves:
-
Deposition onto the Substrate:
- The final step involves the condensation of the vaporized material onto the substrate to form a thin film. Key aspects include:
- Adhesion: The coating material bonds strongly with the substrate, ensuring durability.
- Thickness Control: The thickness of the coating is controlled using a quartz crystal rate monitor, which measures the deposition rate and ensures uniformity.
- Properties of the Coating: The resulting film can have properties such as high hardness, corrosion resistance, and thermal stability, depending on the material and process parameters.
- The final step involves the condensation of the vaporized material onto the substrate to form a thin film. Key aspects include:
-
Vacuum Environment:
- PVD is conducted in a vacuum or low-pressure chamber to minimize contamination and unwanted chemical reactions. The vacuum environment:
- Reduces the presence of background gases that could interfere with the deposition process.
- Enhances the purity and quality of the coating.
- Allows for precise control over the deposition process.
- PVD is conducted in a vacuum or low-pressure chamber to minimize contamination and unwanted chemical reactions. The vacuum environment:
-
Applications of PVD:
- PVD is used in a wide range of industries due to its ability to produce high-quality, functional coatings. Common applications include:
- Electronics: Thin films for semiconductors and microelectronics.
- Optics: Anti-reflective and protective coatings for lenses and mirrors.
- Manufacturing: Wear-resistant and corrosion-resistant coatings for tools and components.
- Decorative Coatings: Durable and aesthetically pleasing finishes for consumer products.
- PVD is used in a wide range of industries due to its ability to produce high-quality, functional coatings. Common applications include:
-
Advantages of PVD:
- Durability: PVD coatings are highly durable and resistant to wear, corrosion, and high temperatures.
- Precision: The process allows for precise control over film thickness and composition.
- Versatility: PVD can be used with a wide range of materials and substrates.
- Eco-Friendly: PVD is a clean process that produces minimal waste and does not involve harmful chemicals.
-
Limitations of PVD:
- Cost: The equipment and process can be expensive, especially for large-scale applications.
- Complexity: The process requires specialized equipment and expertise.
- Line-of-Sight Limitation: The coating is applied only to surfaces directly exposed to the vaporized material, which can limit its use for complex geometries.
In summary, PVD is a versatile and precise coating technology that involves the vaporization of a solid material, its transportation in a vacuum environment, and its deposition onto a substrate to form a thin, functional film. The process is widely used across various industries due to its ability to produce durable, high-performance coatings with excellent adhesion and uniformity.
Summary Table:
Aspect | Details |
---|---|
Process | Converts solid material into vapor, transports in vacuum, deposits on substrate. |
Methods | Thermal evaporation, sputtering, arc discharge, laser/electron beam. |
Key Steps | Gasification, migration, deposition. |
Applications | Electronics, optics, manufacturing, decorative coatings. |
Advantages | Durability, precision, versatility, eco-friendly. |
Limitations | High cost, complexity, line-of-sight limitation. |
Discover how PVD can enhance your products—contact us today for expert advice!