Sintering is a critical manufacturing process used to fuse particles into a solid mass without melting the materials. It is widely applied in ceramics, metals, and plastics, leveraging heat and pressure below the material's melting point to reduce porosity and create a dense, cohesive structure. The process involves several stages, including powder preparation, compaction, and heating in a sintering furnace to bond particles through solid-state diffusion. Understanding the basics of sintering is essential for optimizing material properties and achieving desired outcomes in various industrial applications.
Key Points Explained:
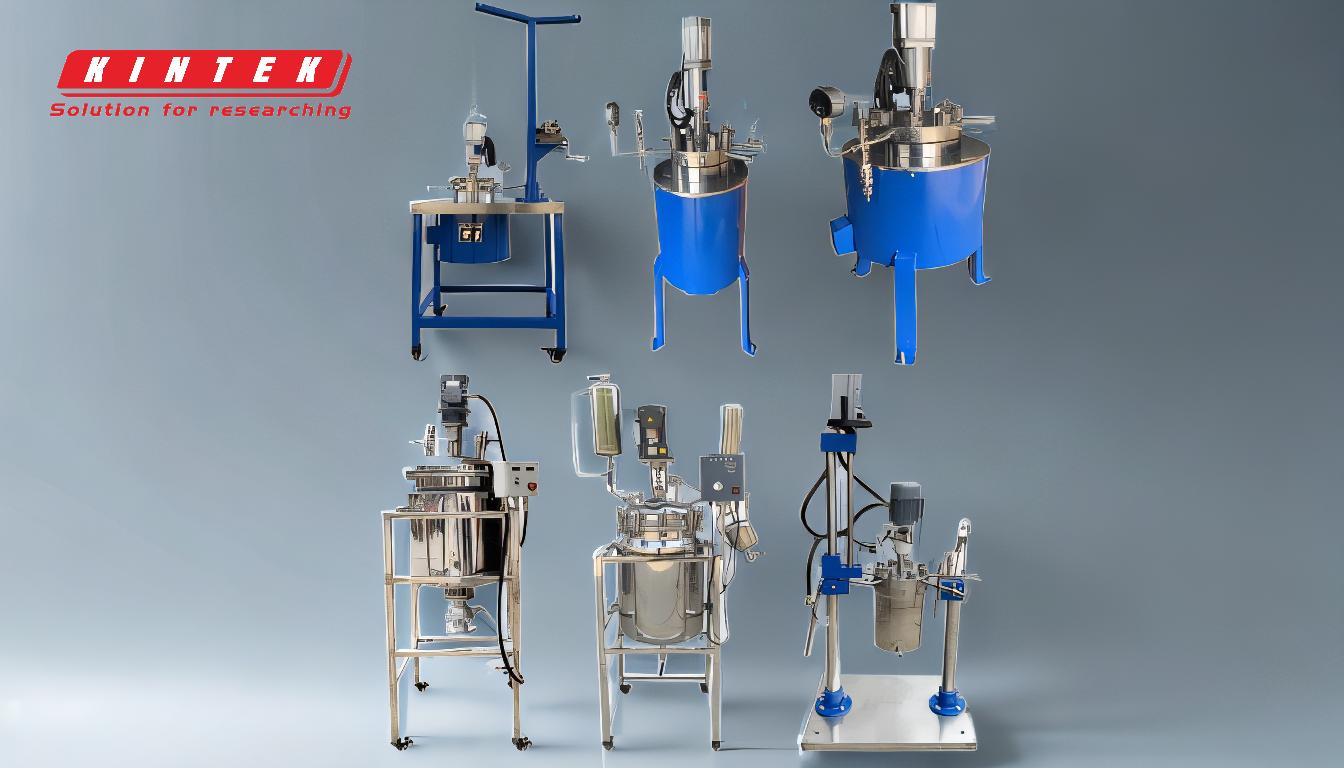
-
Definition and Purpose of Sintering:
- Sintering is a thermal process that bonds particles together using heat and pressure without reaching the material's melting point.
- It is used to create solid, dense materials from powdered forms, reducing porosity and improving mechanical properties.
- Common applications include ceramics, metals, and sintered plastics.
-
Stages of the Sintering Process:
- Powder Preparation: The process begins with the preparation of powdered materials, often mixed with bonding agents like water, wax, or polymers.
- Compaction: The powder is pressed into a desired shape using high pressure to form a "green" part.
- Heating: The green part is heated in a sintering furnace at temperatures below the melting point to remove the bonding agent and fuse the particles.
- Cooling: The material is cooled to solidify the structure, resulting in a low-porosity, high-strength product.
-
Mechanisms of Sintering:
- Solid-State Diffusion: Particles bond through atomic diffusion at their surfaces without liquefaction.
- Liquid-Phase Sintering: In some cases, a secondary material (e.g., bronze) melts and flows between particles, bonding them while the primary material remains solid.
- Oxide Reduction and Lubricant Removal: During heating, oxides are reduced, and any lubricants or binders are burned away.
-
Types of Sintering:
- Metal Sintering: Involves compacting metal powders and heating them in a furnace to create strong, durable components.
- Ceramic Sintering: Uses high temperatures and pressures to fuse ceramic powders into solid structures.
- Hot Press Sintering: Combines high temperature and pressure in a vacuum environment to achieve dense, high-quality materials.
-
Equipment: Sintering Furnace:
- A sintering furnace is a critical piece of equipment that provides controlled heating and cooling environments.
- It typically consists of a furnace body, heating elements, a pressure system, and a vacuum system for specialized applications.
- The furnace ensures uniform heating and precise temperature control, which are essential for consistent results.
-
Benefits of Sintering:
- Material Efficiency: Sintering allows the use of powdered materials, minimizing waste.
- Complex Shapes: It enables the production of intricate shapes that are difficult to achieve with traditional manufacturing methods.
- Improved Properties: The process enhances material properties such as strength, wear resistance, and thermal conductivity.
-
Applications of Sintering:
- Automotive Industry: Used to produce engine components, gears, and bearings.
- Electronics: Sintered materials are used in capacitors, resistors, and magnetic components.
- Medical Devices: Sintering is employed to create implants and surgical tools with high precision and biocompatibility.
By understanding these fundamentals, purchasers of equipment and consumables can make informed decisions about the types of sintering furnaces and materials needed for specific applications, ensuring optimal performance and cost-effectiveness.
Summary Table:
Aspect | Details |
---|---|
Definition | Thermal process bonding particles using heat and pressure below melting point. |
Stages | Powder preparation, compaction, heating, and cooling. |
Mechanisms | Solid-state diffusion, liquid-phase sintering, oxide reduction. |
Types | Metal sintering, ceramic sintering, hot press sintering. |
Equipment | Sintering furnace with controlled heating, pressure, and vacuum systems. |
Benefits | Material efficiency, complex shapes, improved mechanical properties. |
Applications | Automotive, electronics, medical devices. |
Ready to optimize your sintering process? Contact our experts today for tailored solutions!