LPCVD (Low Pressure Chemical Vapor Deposition) is a highly advantageous technique in semiconductor manufacturing, offering a range of benefits that make it a preferred choice for thin film deposition. It operates at low temperatures, enabling high-quality film production with excellent conformal step coverage and uniformity. LPCVD is versatile, capable of depositing various materials such as silicon dioxide, silicon nitride, and polycrystalline silicon, making it suitable for diverse applications in the electronics and semiconductor industries. Additionally, it provides high deposition rates, reduces particle pollution by eliminating the need for carrier gases, and ensures better composition and structure control. Its simple design, high throughput, and cost-effectiveness further enhance its appeal for high-value-added semiconductor production.
Key Points Explained:
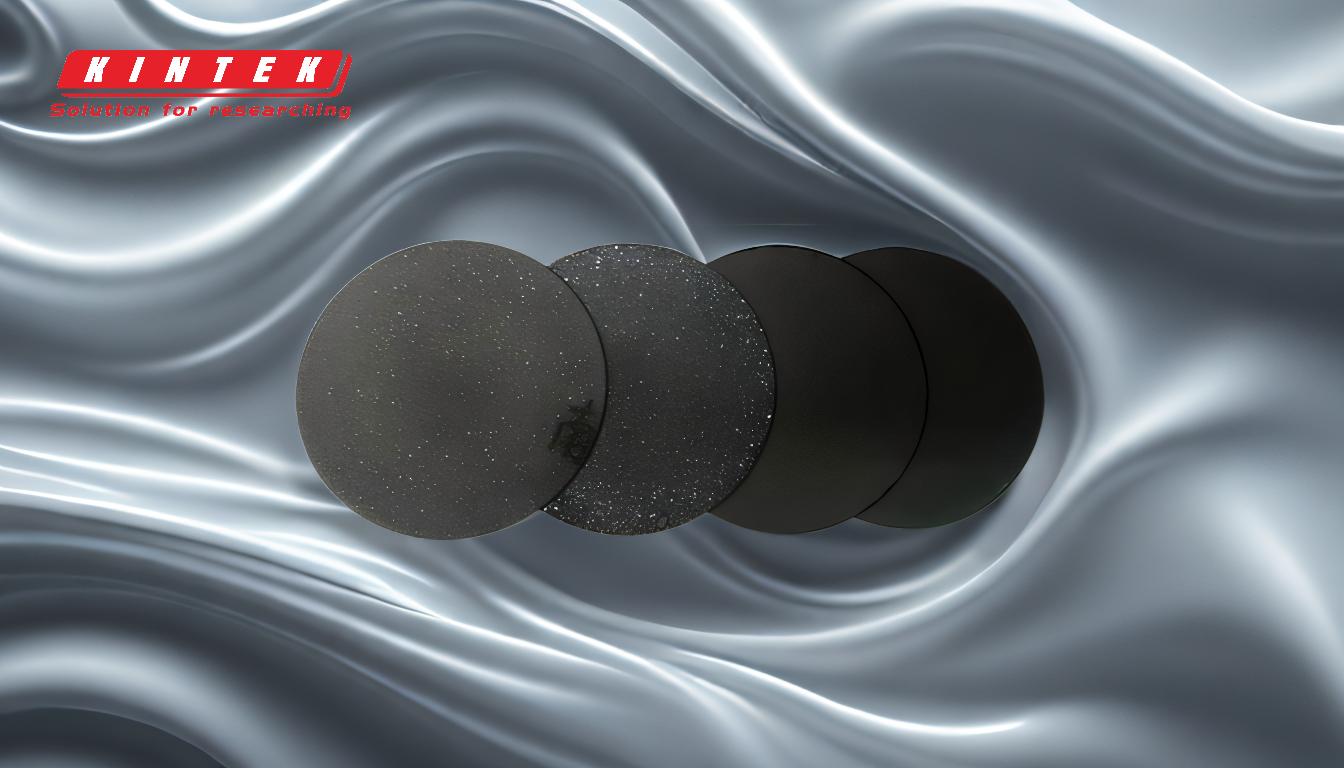
-
Low-Temperature Processing:
- LPCVD operates at relatively low temperatures compared to other deposition methods, which is crucial for maintaining the integrity of temperature-sensitive substrates and materials.
- This feature allows for the deposition of high-quality films without compromising the structural or electrical properties of the underlying materials.
-
High-Quality Films with Excellent Conformal Step Coverage:
- LPCVD produces films with superior uniformity and conformal step coverage, ensuring even deposition over complex geometries and high-aspect-ratio structures.
- This is particularly important in semiconductor manufacturing, where precise film thickness and uniformity are critical for device performance.
-
Versatility in Material Deposition:
- LPCVD can deposit a wide range of materials, including silicon dioxide, silicon nitride, polycrystalline silicon, and advanced materials like graphene and carbon nanotubes.
- This versatility makes it suitable for various applications, from traditional IC manufacturing to cutting-edge nanotechnology.
-
High Deposition Rates and Output:
- The process offers high deposition rates, enabling faster production cycles and increased throughput.
- This efficiency is beneficial for large-scale semiconductor manufacturing, where time and output are critical factors.
-
Reduced Particle Pollution:
- LPCVD does not require carrier gases, which minimizes particle contamination during the deposition process.
- This results in cleaner films with fewer defects, enhancing the reliability and performance of semiconductor devices.
-
Improved Film Uniformity and Resistivity Control:
- LPCVD ensures excellent film uniformity and resistivity control, which are essential for consistent device performance.
- This capability is particularly valuable in applications requiring precise electrical properties, such as in transistors and memory devices.
-
Trench Coverage and Filling Capability:
- The technique excels in filling trenches and other high-aspect-ratio features, making it ideal for advanced semiconductor architectures like 3D NAND and FinFETs.
- This capability ensures reliable device functionality even in complex designs.
-
Economic and Throughput Advantages:
- LPCVD systems are relatively simple in design, offering cost-effective solutions for thin film deposition.
- Their high throughput and excellent economy make them a practical choice for both research and industrial applications.
-
Wide Application in High-Value-Added Semiconductor Industry:
- LPCVD is widely used in the semiconductor industry for producing high-value-added products, including advanced logic and memory devices.
- Its ability to deposit high-quality films with specific properties makes it indispensable for manufacturing cutting-edge semiconductor technologies.
-
Flexibility in Material Properties:
- LPCVD allows for the customization of material properties, such as conductivity and doping levels, to meet specific application requirements.
- This flexibility enables the production of tailored materials for diverse semiconductor applications.
In summary, LPCVD stands out as a highly effective and versatile deposition technique, offering numerous benefits that cater to the demanding requirements of modern semiconductor manufacturing. Its ability to produce high-quality, uniform films with excellent step coverage, combined with its economic and throughput advantages, makes it a cornerstone technology in the electronics industry.
Summary Table:
Advantage | Description |
---|---|
Low-Temperature Processing | Operates at low temperatures, preserving substrate integrity and material quality. |
High-Quality Films | Produces uniform films with excellent conformal step coverage. |
Versatile Material Deposition | Deposits silicon dioxide, silicon nitride, polycrystalline silicon, and more. |
High Deposition Rates | Enables faster production cycles and increased throughput. |
Reduced Particle Pollution | Eliminates carrier gases, minimizing contamination and defects. |
Improved Film Uniformity | Ensures consistent resistivity and device performance. |
Trench Coverage | Fills high-aspect-ratio features for advanced semiconductor designs. |
Economic and Throughput Advantages | Simple design, high throughput, and cost-effectiveness. |
Wide Application | Used in high-value-added semiconductor production, including logic and memory. |
Flexibility in Material Properties | Customizes conductivity and doping levels for tailored applications. |
Ready to enhance your semiconductor manufacturing process with LPCVD? Contact us today to learn more!