Sintering is a critical manufacturing process that transforms powdery materials into dense, solid masses without melting the materials. It involves the application of heat and pressure to bond particles together, enhancing material properties such as strength, durability, and hardness. The process is influenced by factors like temperature, pressure, particle size, composition, and the surrounding atmosphere. Sintering is widely used in industries such as powder metallurgy and ceramic manufacturing, where it directly impacts the microstructure and performance of the final product. Understanding the characteristics of sintering is essential for optimizing material properties and achieving desired outcomes in various applications.
Key Points Explained:
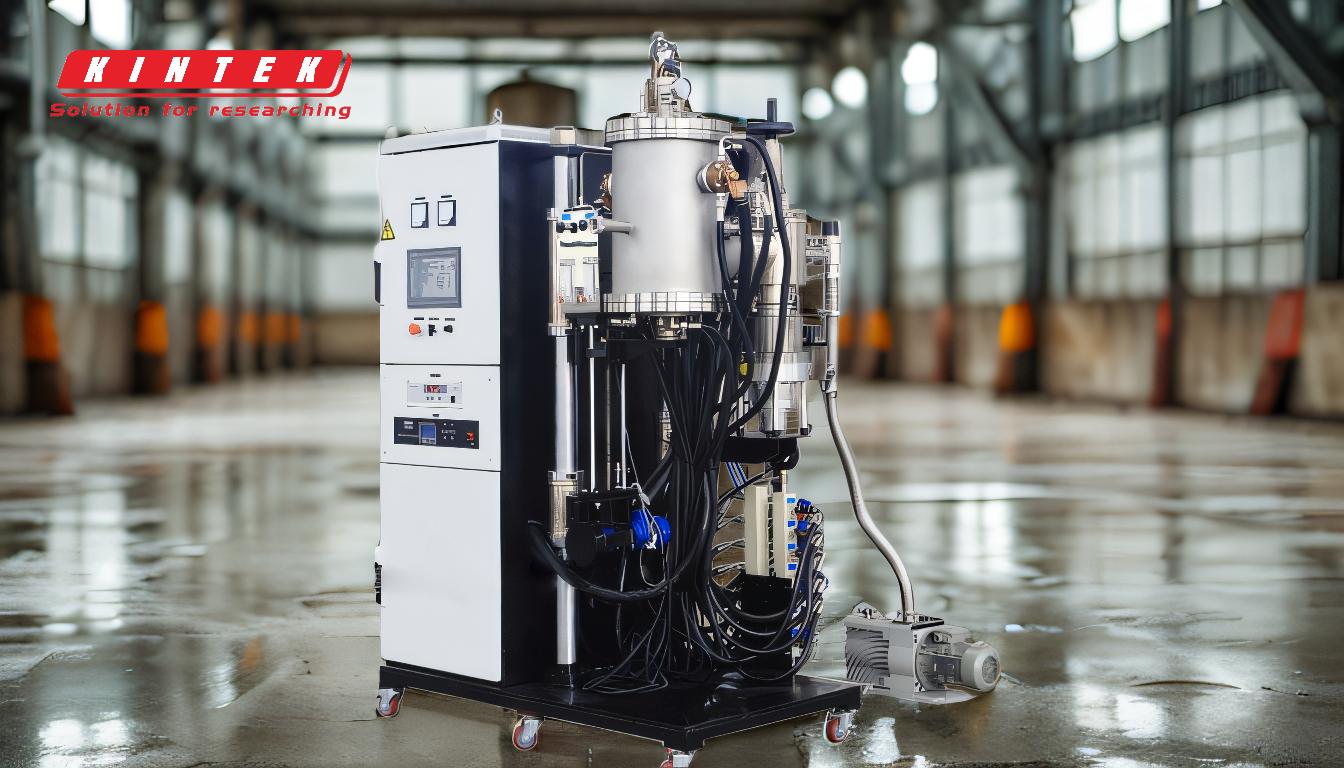
-
Definition and Purpose of Sintering:
- Sintering is a process that combines small particles into a solid mass without melting the materials. It is achieved through the application of heat and pressure, which forces atoms into tighter bonds, resulting in a harder, stronger, and more durable material.
- This process is commonly used in powder metallurgy and ceramic manufacturing, where it transforms powdery materials into dense bodies with improved mechanical properties.
-
Key Factors Influencing Sintering:
- Temperature: Determines the kinetics of sintering and the final material properties. Higher temperatures generally enhance densification and bonding between particles.
- Heating Rate: Affects the rate at which densification occurs. A controlled heating rate is crucial to avoid defects and ensure uniform densification.
- Pressure: Enhances particle rearrangement and helps eliminate porosity, leading to a more compact and dense material.
- Particle Size: Smaller particles have a higher surface area-to-volume ratio, which promotes better densification and bonding during sintering.
- Composition: Homogeneous compositions lead to more uniform sintering behavior and better material properties.
-
Microstructural Changes During Sintering:
- Sintering directly affects the grain size, pore size, and grain boundary shape and distribution in the microstructure of materials.
- These changes influence the material's mechanical properties, such as strength, durability, and hardness. For example, reducing porosity through sintering can significantly enhance the material's tensile strength and fatigue resistance.
-
Atmosphere and Cooling Rate:
- The atmosphere in which sintering occurs (e.g., air, vacuum, or inert gases like argon or nitrogen) can impact the final material properties. For instance, sintering in a vacuum or inert atmosphere can prevent oxidation and improve material quality.
- The cooling rate after sintering also plays a role in determining the final microstructure and properties. Rapid cooling can lead to finer grain structures, while slower cooling may result in larger grains.
-
Applications of Sintering:
- Sintering is widely used in the production of ceramics, where it transforms clay and other ceramic powders into durable products like pottery and tiles.
- In powder metallurgy, sintering is used to produce metal parts with complex shapes and high strength, such as gears, bearings, and automotive components.
- The process is also applicable to plastics and other materials, where it enhances the mechanical properties and durability of the final product.
-
Advantages of Sintering:
- Enhanced Material Properties: Sintering improves the strength, hardness, and durability of materials by reducing porosity and enhancing atomic bonding.
- Cost-Effective: Sintering allows for the production of complex shapes with minimal material waste, making it a cost-effective manufacturing process.
- Versatility: The process can be applied to a wide range of materials, including metals, ceramics, and plastics, making it versatile for various industrial applications.
-
Challenges and Limitations:
- Control of Process Parameters: Achieving the desired material properties requires precise control of temperature, pressure, and other sintering parameters. Inconsistent conditions can lead to defects or suboptimal material performance.
- Material Limitations: Not all materials are suitable for sintering. Some materials may require specific conditions or additives to achieve the desired densification and bonding.
By understanding these key characteristics of sintering, manufacturers can optimize the process to produce materials with tailored properties for specific applications. Whether in ceramics, metals, or plastics, sintering remains a fundamental technique for enhancing material performance and achieving high-quality, durable products.
Summary Table:
Key Aspect | Details |
---|---|
Definition | Combines particles into a solid mass without melting. |
Key Factors | Temperature, pressure, particle size, composition, atmosphere. |
Applications | Ceramics, powder metallurgy, plastics. |
Advantages | Enhanced strength, cost-effectiveness, versatility. |
Challenges | Precise parameter control, material suitability. |
Optimize your sintering process for superior material performance—contact our experts today!