Chemical deposition processes, particularly Chemical Vapor Deposition (CVD), are widely used in various industries to create thin films and coatings on substrates. These processes involve the reaction of gaseous precursors to form a solid material on a substrate. The key types of CVD processes include Atmospheric Pressure CVD (APCVD), Low Pressure CVD (LPCVD), Ultrahigh Vacuum CVD (UHVCVD), Laser Induced CVD (LICVD), Metal-Organic CVD (MOCVD), and Plasma Enhanced CVD (PECVD). Each type is characterized by its unique operating conditions, such as pressure, temperature, and the use of plasma or laser energy, which make them suitable for different materials and applications. Additionally, other deposition methods like sputtering and aerosol-assisted CVD offer alternative approaches for specific needs.
Key Points Explained:
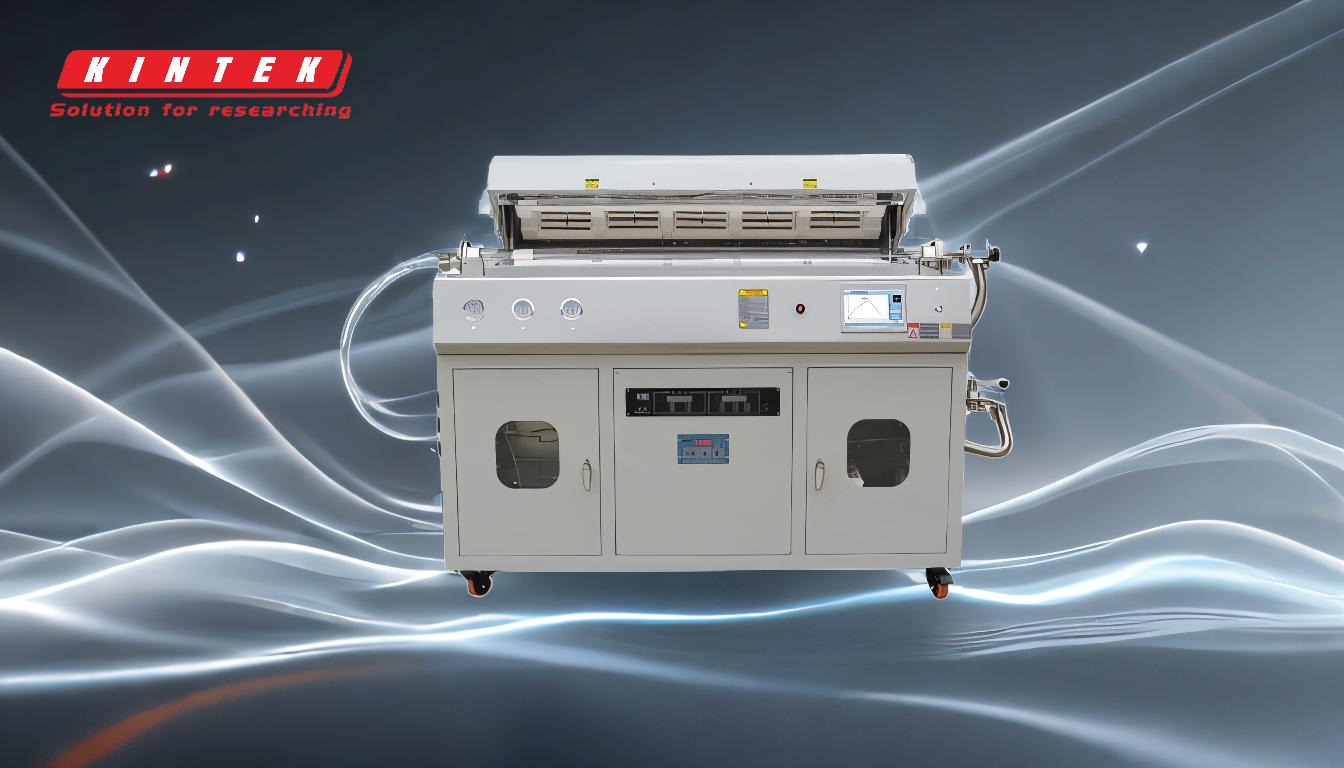
-
Atmospheric Pressure CVD (APCVD):
- Operates at atmospheric pressure, making it simpler and more cost-effective.
- Typically used for depositing oxides and nitrides.
- The reaction rate is mass transfer limited, meaning the process is controlled by the diffusion of reactants to the substrate surface.
-
Low Pressure CVD (LPCVD):
- Operates at reduced pressures, which enhances the uniformity and quality of the deposited films.
- Commonly used for depositing polysilicon and silicon nitride.
- The reaction rate is surface reaction limited, allowing for better control over film properties.
-
Ultrahigh Vacuum CVD (UHVCVD):
- Operates under extremely high vacuum conditions, reducing contamination and allowing for the deposition of high-purity materials.
- Ideal for applications requiring ultra-clean environments, such as in semiconductor manufacturing.
-
Laser Induced CVD (LICVD):
- Utilizes laser energy to locally heat the substrate, enabling precise deposition patterns.
- Suitable for applications requiring high spatial resolution, such as in microfabrication.
-
Metal-Organic CVD (MOCVD):
- Uses metal-organic compounds as precursors, allowing for the deposition of compound semiconductors like GaAs and InP.
- Widely used in the production of optoelectronic devices, such as LEDs and laser diodes.
-
Plasma Enhanced CVD (PECVD):
- Incorporates plasma to lower the deposition temperature, making it suitable for temperature-sensitive substrates.
- Commonly used for depositing silicon-based films and amorphous carbon.
-
Sputtering:
- A physical deposition process where atoms are ejected from a target material and deposited onto a substrate.
- Used for depositing metals, alloys, and insulating materials.
- Offers excellent control over film composition and thickness.
-
Aerosol-Assisted CVD:
- Involves the use of aerosolized precursors, which are easier to transport and control.
- Suitable for depositing complex materials and multi-component films.
-
Direct Liquid Injection CVD:
- Involves injecting a liquid precursor into a heated chamber where it is vaporized.
- Allows for precise control over precursor delivery, making it ideal for depositing high-quality films.
-
Plasma-Based Methods:
- Utilize plasma to enhance the chemical reactions, enabling deposition at lower temperatures.
- Suitable for depositing a wide range of materials, including dielectrics and metals.
Each of these chemical deposition processes has its own set of advantages and limitations, making them suitable for specific applications. Understanding the nuances of each method allows for the selection of the most appropriate technique based on the desired film properties, substrate material, and application requirements.
Summary Table:
Process | Key Features | Applications |
---|---|---|
APCVD | Operates at atmospheric pressure; cost-effective; mass transfer limited | Depositing oxides and nitrides |
LPCVD | Reduced pressure; uniform films; surface reaction limited | Depositing polysilicon and silicon nitride |
UHVCVD | Ultrahigh vacuum; high-purity materials; low contamination | Semiconductor manufacturing |
LICVD | Laser-induced; precise deposition; high spatial resolution | Microfabrication |
MOCVD | Metal-organic precursors; compound semiconductors | Optoelectronic devices (LEDs, laser diodes) |
PECVD | Plasma-enhanced; lower deposition temperature | Silicon-based films, amorphous carbon |
Sputtering | Physical deposition; excellent control over film composition | Metals, alloys, insulating materials |
Aerosol-Assisted CVD | Aerosolized precursors; complex materials | Multi-component films |
Direct Liquid Injection CVD | Liquid precursors; precise delivery | High-quality films |
Plasma-Based Methods | Plasma-enhanced; lower temperatures | Dielectrics, metals |
Need help selecting the right chemical deposition process for your application? Contact our experts today!