Chemical vapor deposition (CVD) is a highly controlled process used to deposit thin films of materials onto substrates through chemical reactions in the vapor phase. The process involves several critical parameters, including the choice of precursor materials, reaction conditions, and deposition techniques. These parameters influence the quality, thickness, and properties of the deposited films. Key stages of the CVD process include the transport of gaseous reactants to the substrate, adsorption of reactants, surface reactions, and the desorption of by-products. Understanding these parameters is essential for optimizing the CVD process for specific applications, such as creating ultra-thin layers for electrical circuits or semiconductor devices.
Key Points Explained:
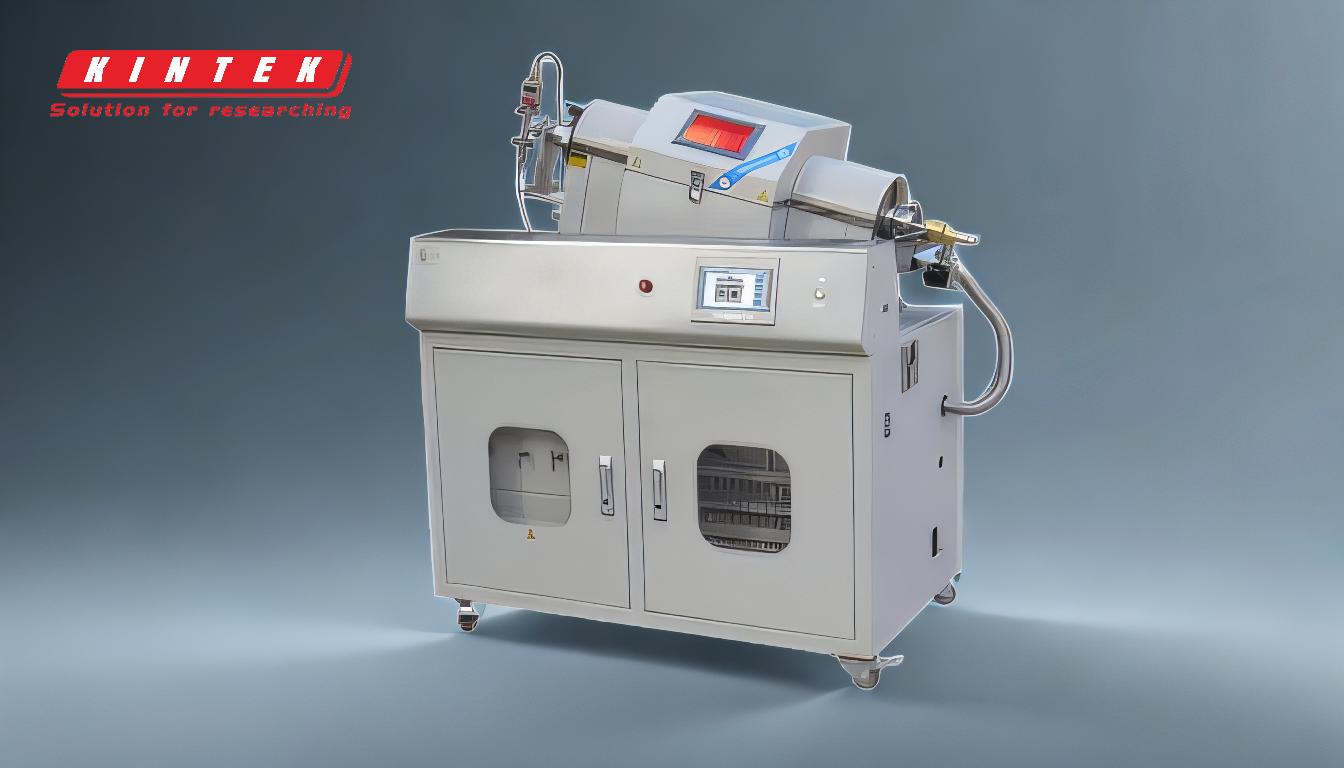
-
Precursor Materials and Volatility
- The CVD process begins with the selection of volatile precursor materials, which are typically in gaseous or vapor form. These precursors must be stable enough to be transported to the substrate but reactive enough to decompose or react under specific conditions. Common precursors include metal-organic compounds, halides, and hydrides.
- The volatility of the precursor is crucial because it determines the efficiency of transport to the substrate surface. Precursors with low volatility may require higher temperatures or specialized delivery systems.
-
Transport of Gaseous Reactants
- The gaseous reactants are transported to the substrate surface through a carrier gas, such as nitrogen or argon. The flow rate and pressure of the carrier gas are critical parameters that influence the uniformity and deposition rate of the film.
- Proper transport ensures that the reactants reach the substrate evenly, which is essential for achieving a uniform film thickness.
-
Adsorption and Surface Reactions
- Once the reactants reach the substrate, they adsorb onto its surface. Adsorption is influenced by factors such as substrate temperature, surface chemistry, and the reactivity of the precursors.
- Surface reactions then occur, leading to the formation of the desired material. These reactions can be thermally driven or catalyzed by the substrate surface. The type and rate of these reactions are controlled by parameters such as temperature, pressure, and the presence of catalysts.
-
Deposition Techniques
- CVD encompasses various techniques, including atmospheric pressure chemical vapor deposition (APCVD), low-pressure chemical vapor deposition (LPCVD), and plasma-enhanced chemical vapor deposition (PECVD). Each technique has specific advantages and is chosen based on the desired film properties and application requirements.
- For example, PECVD allows for lower deposition temperatures, making it suitable for temperature-sensitive substrates.
-
Substrate Temperature and Chamber Pressure
- The substrate temperature is a critical parameter that affects the kinetics of surface reactions and the quality of the deposited film. Higher temperatures generally increase reaction rates but may also lead to undesirable side reactions or film defects.
- Chamber pressure influences the mean free path of the gas molecules and the deposition rate. Low-pressure conditions are often used to reduce impurities and improve film uniformity.
-
Desorption and By-product Removal
- After the surface reactions, gaseous by-products are desorbed from the substrate and transported away from the reaction zone. Efficient removal of by-products is essential to prevent contamination and ensure the purity of the deposited film.
- The design of the CVD system, including the exhaust and vacuum systems, plays a significant role in this step.
-
Applications and Advantages
- CVD is widely used in industries such as electronics, optics, and coatings due to its ability to produce high-quality, ultra-thin films with precise control over thickness and composition.
- The versatility of CVD allows it to be adapted for various materials, including metals, semiconductors, and ceramics, making it a cornerstone of modern manufacturing processes.
By carefully controlling these parameters, the CVD process can be tailored to meet the specific requirements of different applications, ensuring optimal performance and reliability of the deposited films.
Summary Table:
Parameter | Description |
---|---|
Precursor Materials | Volatile compounds (e.g., metal-organic, halides) chosen for reactivity and stability. |
Transport of Reactants | Carrier gas flow rate and pressure ensure uniform delivery to the substrate. |
Adsorption & Reactions | Substrate temperature, surface chemistry, and catalysts drive surface reactions. |
Deposition Techniques | Includes APCVD, LPCVD, and PECVD, each suited for specific film properties. |
Temperature & Pressure | Substrate temperature and chamber pressure control reaction kinetics and purity. |
By-product Removal | Efficient desorption and removal of by-products ensure film purity. |
Applications | Used in electronics, optics, and coatings for high-quality, ultra-thin films. |
Optimize your CVD process for superior thin film quality—contact our experts today!