Hydraulic systems are widely used in various industries due to their efficiency and power transmission capabilities. However, like any mechanical system, they are prone to faults that can affect performance and reliability. Common faults in hydraulic systems include issues such as fluid contamination, overheating, leaks, pressure problems, and component wear. These faults can lead to system inefficiencies, increased maintenance costs, and even catastrophic failures if not addressed promptly. Understanding the root causes of these faults and implementing preventive measures is crucial for maintaining the optimal performance of hydraulic systems.
Key Points Explained:
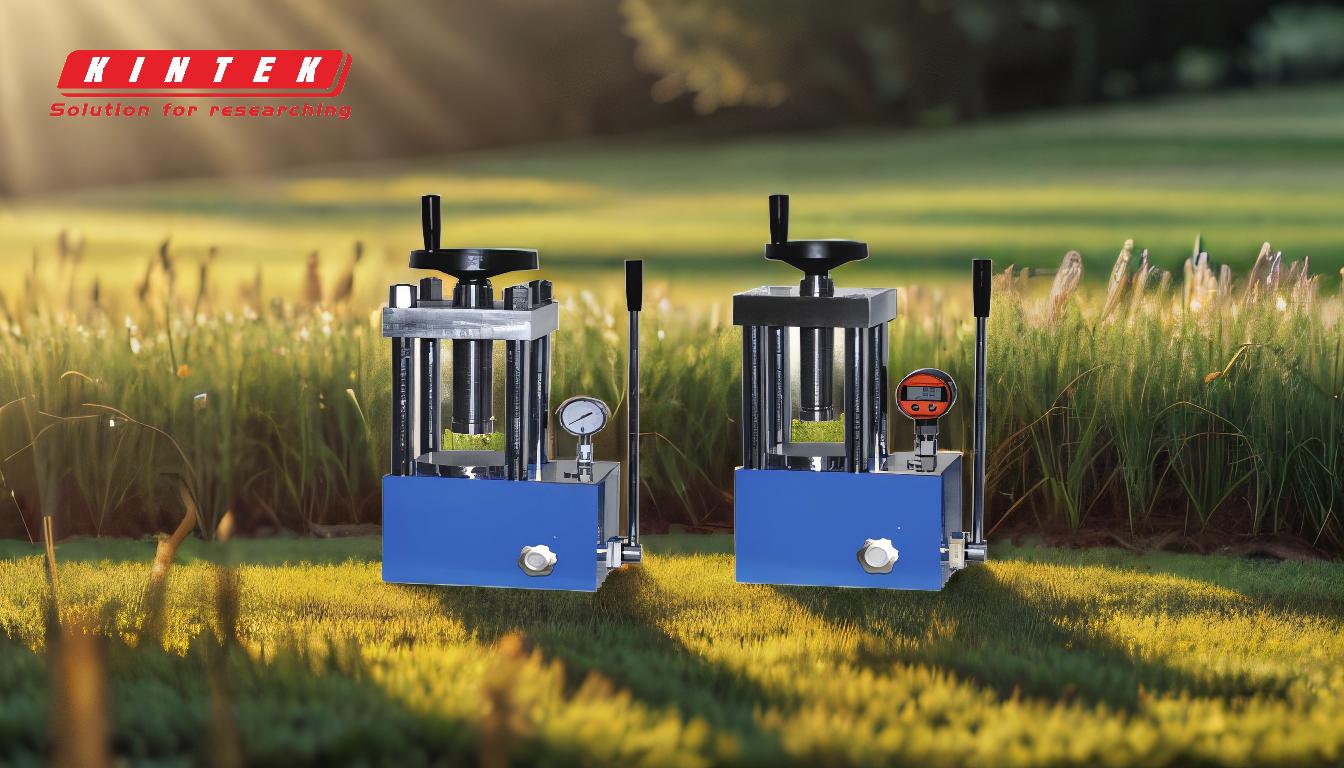
-
Fluid Contamination:
- Cause: Hydraulic fluid contamination is one of the most common issues in hydraulic systems. Contaminants such as dirt, water, and metal particles can enter the system through improper sealing, poor maintenance, or during fluid replacement.
- Impact: Contaminated fluid can cause abrasion, corrosion, and clogging of components like valves, pumps, and actuators, leading to reduced efficiency and potential system failure.
- Prevention: Regular fluid analysis, proper filtration, and maintaining clean working conditions can help prevent contamination.
-
Overheating:
- Cause: Overheating in hydraulic systems can result from excessive load, insufficient cooling, or high ambient temperatures. It can also be caused by internal leakage or inefficient components.
- Impact: Overheating can degrade the hydraulic fluid, reduce its lubricating properties, and cause thermal expansion of components, leading to increased wear and potential system failure.
- Prevention: Ensuring proper system design, adequate cooling, and regular maintenance can help mitigate overheating issues.
-
Leaks:
- Cause: Hydraulic leaks can occur due to worn seals, loose fittings, or damaged hoses and pipes. They can also result from excessive pressure or vibration within the system.
- Impact: Leaks lead to a loss of hydraulic fluid, reduced system pressure, and potential environmental hazards. They can also cause contamination if external debris enters the system.
- Prevention: Regular inspection of seals, fittings, and hoses, along with proper installation and maintenance, can help prevent leaks.
-
Pressure Problems:
- Cause: Pressure issues in hydraulic systems can arise from faulty pressure relief valves, pump inefficiencies, or blockages in the system. Incorrect pressure settings can also lead to problems.
- Impact: Low pressure can result in inadequate system performance, while high pressure can cause component damage and safety hazards.
- Prevention: Regular calibration of pressure relief valves, proper system design, and monitoring of pressure levels can help maintain optimal system pressure.
-
Component Wear:
- Cause: Wear and tear of hydraulic components such as pumps, valves, and cylinders are inevitable over time. However, accelerated wear can occur due to factors like poor lubrication, contamination, or excessive load.
- Impact: Worn components can lead to reduced system efficiency, increased leakage, and eventual system failure.
- Prevention: Regular maintenance, proper lubrication, and timely replacement of worn components can help extend the life of hydraulic systems.
-
Noise and Vibration:
- Cause: Excessive noise and vibration in hydraulic systems can be caused by cavitation, air entrapment, or misaligned components. It can also result from worn or damaged parts.
- Impact: Noise and vibration can indicate underlying issues such as cavitation or air in the system, which can lead to component damage and reduced system performance.
- Prevention: Ensuring proper fluid levels, addressing air entrapment, and maintaining alignment of components can help reduce noise and vibration.
-
Cavitation:
- Cause: Cavitation occurs when the hydraulic fluid vaporizes due to low pressure, forming bubbles that collapse violently when they reach high-pressure areas. This can be caused by restricted fluid flow or excessive pump speed.
- Impact: Cavitation can cause pitting and erosion of components, leading to reduced efficiency and potential system failure.
- Prevention: Ensuring proper fluid flow, maintaining adequate pressure, and avoiding excessive pump speeds can help prevent cavitation.
By understanding these common faults and their causes, operators and maintenance personnel can take proactive steps to prevent issues and ensure the reliable operation of hydraulic systems. Regular maintenance, proper system design, and adherence to best practices are key to minimizing downtime and extending the lifespan of hydraulic equipment.
Summary Table:
Fault | Cause | Impact | Prevention |
---|---|---|---|
Fluid Contamination | Dirt, water, or metal particles entering through improper sealing or poor maintenance | Abrasion, corrosion, clogging, and potential system failure | Regular fluid analysis, proper filtration, and clean working conditions |
Overheating | Excessive load, insufficient cooling, high ambient temperatures, or internal leakage | Degraded fluid, reduced lubrication, thermal expansion, and system failure | Proper system design, adequate cooling, and regular maintenance |
Leaks | Worn seals, loose fittings, damaged hoses, or excessive pressure/vibration | Fluid loss, reduced pressure, environmental hazards, and contamination | Regular inspection, proper installation, and maintenance of seals and fittings |
Pressure Problems | Faulty pressure relief valves, pump inefficiencies, or blockages | Inadequate performance or component damage | Regular calibration, proper system design, and pressure monitoring |
Component Wear | Poor lubrication, contamination, or excessive load | Reduced efficiency, increased leakage, and system failure | Regular maintenance, proper lubrication, and timely replacement of components |
Noise and Vibration | Cavitation, air entrapment, misaligned components, or worn/damaged parts | Component damage and reduced system performance | Proper fluid levels, addressing air entrapment, and maintaining alignment |
Cavitation | Restricted fluid flow or excessive pump speed | Pitting, erosion, reduced efficiency, and system failure | Ensuring proper fluid flow, maintaining adequate pressure, and avoiding high speeds |
Ensure your hydraulic system runs smoothly—contact our experts today for tailored solutions!