MOCVD (Metal-Organic Chemical Vapor Deposition) systems are complex and require careful design and operation due to the use of hazardous materials. The system's components are designed to ensure safety, precision, and efficiency in the deposition process. Below is a detailed explanation of the key components and their roles in maintaining safety and functionality.
Key Points Explained:
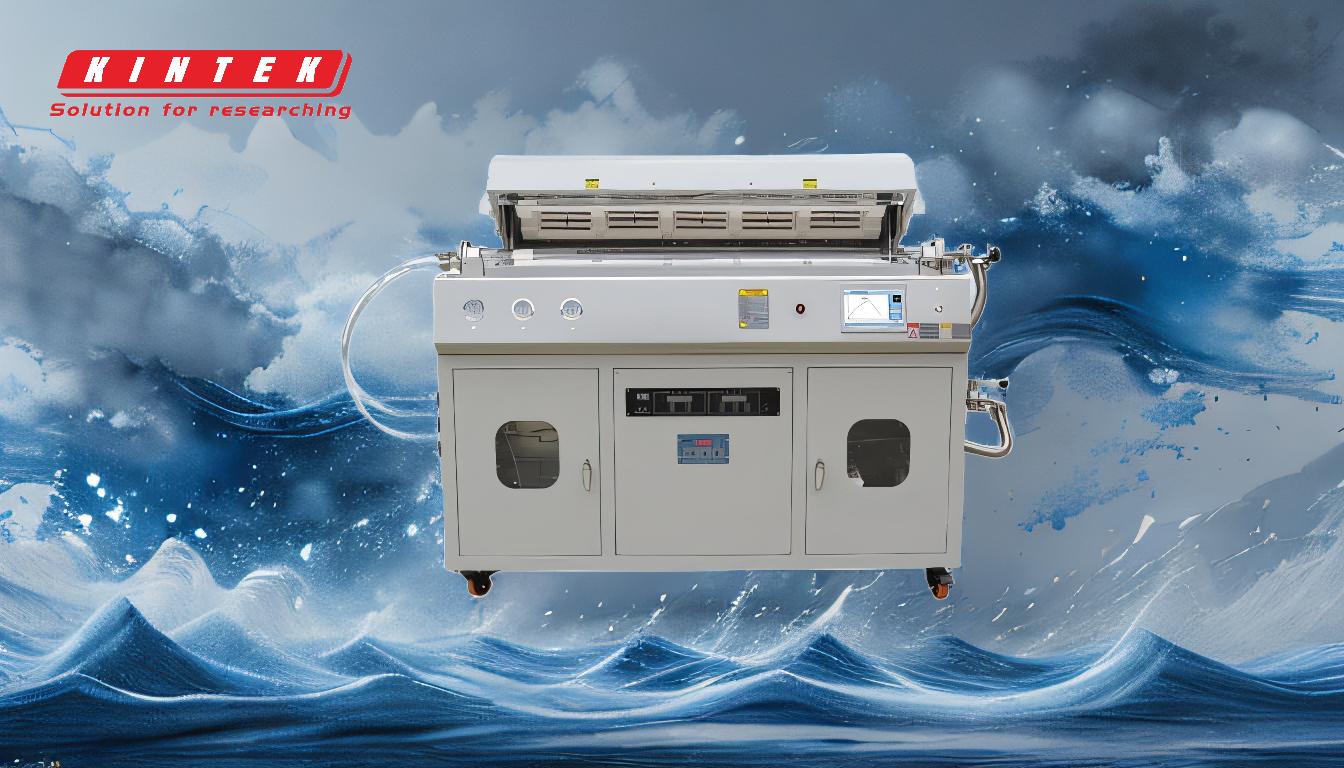
-
Gas Delivery System:
- The gas delivery system is responsible for transporting the metal-organic precursors and carrier gases to the reaction chamber. It includes:
- Mass Flow Controllers (MFCs): These ensure precise control of gas flow rates, which is critical for maintaining the correct stoichiometry of the deposited films.
- Gas Lines and Valves: These are designed to be leak-tight to prevent the escape of toxic or flammable gases.
- Bubblers: Used to vaporize liquid precursors, these must be carefully controlled to avoid over-pressurization or leaks.
- The gas delivery system is responsible for transporting the metal-organic precursors and carrier gases to the reaction chamber. It includes:
-
Reaction Chamber:
- The reaction chamber is where the actual deposition process occurs. It is designed to withstand high temperatures and corrosive environments. Key features include:
- Heating Elements: These provide the necessary thermal energy for the chemical reactions to take place.
- Substrate Holder: This holds the wafers or substrates in place during deposition and may rotate to ensure uniform film thickness.
- Exhaust System: This removes by-products and unreacted gases from the chamber, which is crucial for maintaining a clean environment and preventing the buildup of hazardous materials.
- The reaction chamber is where the actual deposition process occurs. It is designed to withstand high temperatures and corrosive environments. Key features include:
-
Safety Systems:
- Safety is a paramount concern in MOCVD systems due to the use of toxic and flammable gases. Key safety components include:
- Leak Detection Systems: These monitor for any gas leaks and trigger alarms if detected.
- Pressure Relief Valves: These prevent over-pressurization in the system, which could lead to explosions or leaks.
- Tail Gas Treatment Units: These neutralize or scrub harmful by-products before they are released into the environment, ensuring compliance with environmental regulations.
- Safety is a paramount concern in MOCVD systems due to the use of toxic and flammable gases. Key safety components include:
-
Control and Monitoring Systems:
- Advanced control systems are essential for the precise operation of MOCVD systems. These include:
- Temperature Controllers: These maintain the reaction chamber at the desired temperature, which is critical for the quality of the deposited films.
- Flow Controllers: These regulate the flow of gases into the chamber, ensuring consistent deposition rates.
- Alarm Systems: These provide immediate alerts in case of any system malfunctions or safety breaches, allowing for rapid response to potential hazards.
- Advanced control systems are essential for the precise operation of MOCVD systems. These include:
-
Cooling Systems:
- MOCVD systems generate significant heat, and effective cooling is necessary to prevent damage to the system and ensure safe operation. Cooling systems may include:
- Water Cooling: This is commonly used to remove heat from the reaction chamber and other critical components.
- Heat Exchangers: These help to dissipate heat efficiently, maintaining the system within safe operating temperatures.
- MOCVD systems generate significant heat, and effective cooling is necessary to prevent damage to the system and ensure safe operation. Cooling systems may include:
-
Vacuum System:
- Many MOCVD systems operate under vacuum or low-pressure conditions to enhance the deposition process. The vacuum system includes:
- Pumps: These create and maintain the necessary vacuum levels within the reaction chamber.
- Pressure Gauges: These monitor the pressure inside the chamber, ensuring it remains within the desired range.
- Many MOCVD systems operate under vacuum or low-pressure conditions to enhance the deposition process. The vacuum system includes:
-
Substrate Loading and Unloading Mechanisms:
- Efficient and safe handling of substrates is crucial for the operation of MOCVD systems. These mechanisms include:
- Load Locks: These allow substrates to be loaded and unloaded without exposing the reaction chamber to atmospheric conditions, which could introduce contaminants or cause safety issues.
- Robotic Arms: These automate the transfer of substrates, reducing the risk of human error and exposure to hazardous materials.
- Efficient and safe handling of substrates is crucial for the operation of MOCVD systems. These mechanisms include:
In summary, the components of an MOCVD system are intricately designed to ensure safety, precision, and efficiency. Each component plays a critical role in the overall operation, from gas delivery and reaction control to safety monitoring and substrate handling. Understanding these components is essential for anyone involved in the operation, maintenance, or procurement of MOCVD systems.
Summary Table:
Component | Key Features |
---|---|
Gas Delivery System | Mass Flow Controllers, Gas Lines, Bubblers |
Reaction Chamber | Heating Elements, Substrate Holder, Exhaust System |
Safety Systems | Leak Detection, Pressure Relief Valves, Tail Gas Treatment |
Control & Monitoring | Temperature Controllers, Flow Controllers, Alarm Systems |
Cooling Systems | Water Cooling, Heat Exchangers |
Vacuum System | Pumps, Pressure Gauges |
Substrate Handling | Load Locks, Robotic Arms |
Learn more about MOCVD systems and how they can enhance your processes—contact our experts today!