A rotary furnace is a complex piece of equipment designed for high-temperature processing of materials. Its key components include the furnace body, furnace lining, drive gear, internal heat source, rotating drum, chassis, roller drive mechanism, charging door, tapping ports, and exhaust system. The furnace body, typically made of steel, is insulated with refractory materials to withstand extreme temperatures and prevent corrosion. The drive gear rotates the furnace, while the heat source (gas or electric) ensures efficient heating through conduction, convection, or radiation. Additional features like the charging door, tapping ports, and exhaust system facilitate material handling and gas management, making the rotary furnace a versatile tool for industrial applications.
Key Points Explained:
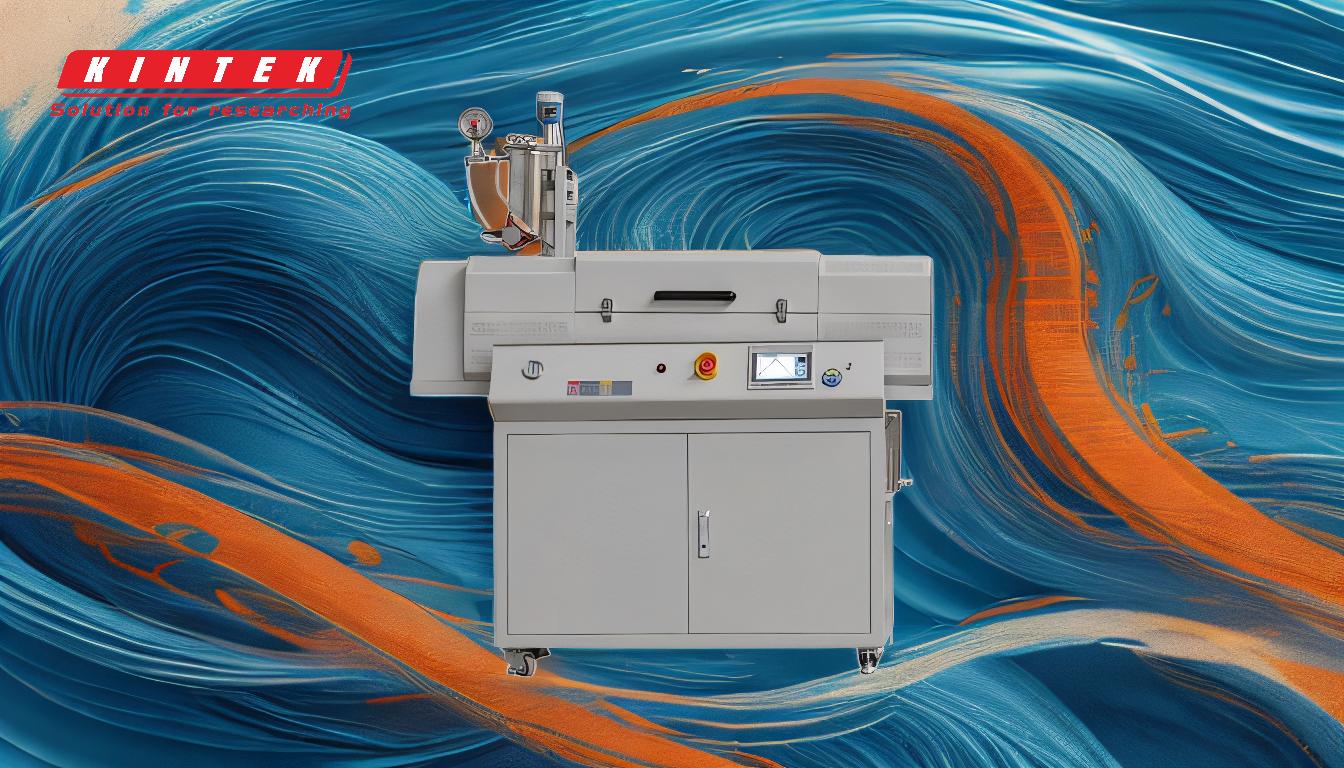
-
Furnace Body:
- The furnace body is the primary structure of the rotary furnace, typically constructed from steel plates welded into a barrel shape.
- Its length can vary depending on the specific application, ensuring it meets the requirements of the material being processed.
- The steel construction provides durability and structural integrity, enabling the furnace to operate under high-temperature conditions.
-
Furnace Lining:
- The furnace lining is made from refractory materials, which serve as insulation to protect the steel body from extreme heat.
- These materials are highly durable and resistant to corrosion, ensuring the furnace's longevity and efficiency.
- The lining also helps maintain consistent temperatures within the furnace, which is critical for uniform material processing.
-
Drive Gear:
- The drive gear is responsible for rotating the furnace, allowing materials to be mixed and heated evenly as they move through the furnace.
- This rotation ensures thorough processing of materials, which is essential for achieving the desired chemical or physical transformations.
- The drive mechanism is typically mounted on a fabricated chassis, providing stability and precision during operation.
-
Internal Heat Source:
- The heat source within the rotary furnace can be either gas or electric, depending on the application and operational requirements.
- Heating is achieved through conduction, convection, or radiation, ensuring efficient energy transfer to the materials being processed.
- The heat source is often controlled automatically or manually to maintain the required furnace temperature.
-
Rotating Drum (Shell):
- The rotating drum, or shell, is the core component where materials are processed.
- It is mounted on a chassis equipped with a roller drive mechanism, which facilitates smooth and consistent rotation.
- The drum's design ensures that materials are transported and mixed effectively as they move through the furnace.
-
Charging Door:
- The charging door is used for loading materials into the furnace.
- It is typically located at one end of the furnace and may include an automatic or manual burner to achieve the desired temperature.
- This component is essential for efficient material handling and process control.
-
Tapping Ports:
- Tapping ports are provided for emptying processed materials from the furnace.
- These ports are strategically placed to allow easy removal of materials without disrupting the furnace's operation.
- They play a crucial role in maintaining the continuous flow of materials through the furnace.
-
Exhaust System:
- The exhaust system is designed to carry flue gases out of the furnace for further processing or disposal.
- It includes an exhaust door, which ensures that harmful gases are safely removed from the working environment.
- This component is vital for maintaining safe and efficient furnace operation.
-
Additional Features:
- Heat-resistant insulation bricks are used to enhance the furnace's thermal efficiency and protect the outer shell from excessive heat.
- The roller drive mechanism ensures smooth and consistent rotation of the drum, which is critical for uniform material processing.
- The furnace may also include cooling chambers and loading mechanisms, depending on its specific application.
By understanding these components, purchasers can make informed decisions about selecting the right rotary furnace for their needs, ensuring optimal performance and longevity.
Summary Table:
Component | Function |
---|---|
Furnace Body | Primary structure made of steel, designed for durability and high heat. |
Furnace Lining | Insulates the body with refractory materials for heat resistance. |
Drive Gear | Rotates the furnace for even material mixing and heating. |
Internal Heat Source | Provides heat via gas or electric systems for efficient processing. |
Rotating Drum | Core component for material processing, mounted on a chassis. |
Charging Door | Allows material loading into the furnace for processing. |
Tapping Ports | Facilitates removal of processed materials without disrupting operations. |
Exhaust System | Removes flue gases safely, ensuring efficient and safe operation. |
Additional Features | Includes insulation bricks, roller drive mechanisms, and cooling chambers. |
Need help selecting the right rotary furnace for your needs? Contact our experts today for personalized advice!