Sintering is a critical manufacturing process that transforms powdery materials into dense, solid bodies by applying heat and pressure below the material's melting point. This process is widely used in industries such as powder metallurgy, ceramics, and additive manufacturing. The key components of sintering include the materials used (e.g., metal powders, ceramics, and plastics), the application of heat and pressure, and the bonding of particles through atomic diffusion. The process enhances the structural integrity, strength, and durability of the final product. Below, the components of sintering are explained in detail.
Key Points Explained:
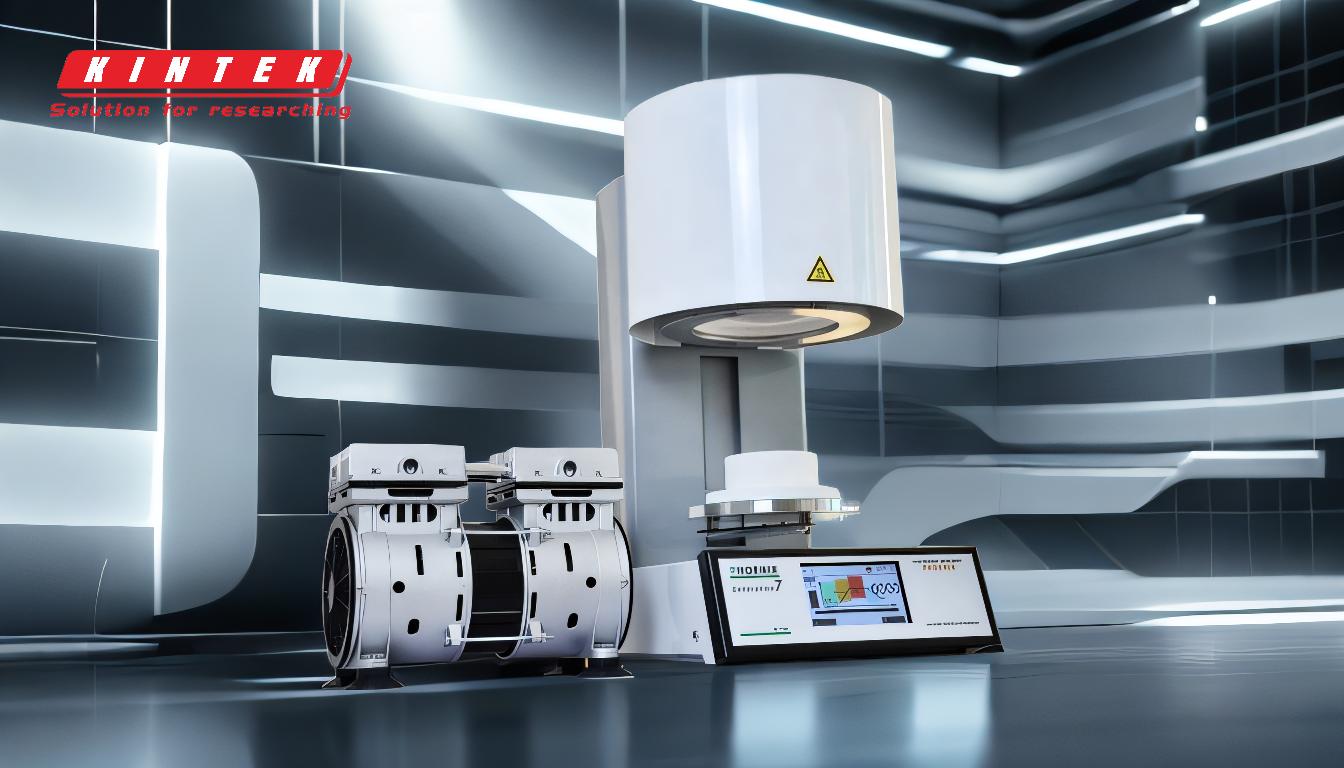
-
Materials Used in Sintering
- Sintering involves a variety of materials, including:
- Metal Powders: Commonly used metals include stainless steel, aluminum, nickel, copper, and titanium alloys. These materials are refined to improve their properties for sintering.
- Ceramics: Used in pottery and advanced ceramics, where sintering enhances hardness and thermal resistance.
- Plastics: Certain polymers can be sintered for applications in additive manufacturing and 3D printing.
- Other Materials: Tungsten, molybdenum, and other high-melting-point materials are often sintered due to their resistance to liquefaction.
- The choice of material depends on the desired properties of the final product, such as strength, durability, and thermal resistance.
- Sintering involves a variety of materials, including:
-
Heat Application
- Heat is a fundamental component of sintering, applied at temperatures below the material's melting point.
- Temperature Zones: Furnaces used in sintering often have multiple temperature zones to ensure uniform heating and bonding.
- Atomic Diffusion: Heat causes atoms to diffuse across particle boundaries, fusing them together without melting the entire mass.
- Temperature Control: Precise control of temperature is crucial to avoid melting, which would compromise the structural integrity of the material.
- Heat is a fundamental component of sintering, applied at temperatures below the material's melting point.
-
Pressure Application
- Pressure is applied to compact the powdery materials into a solid mass.
- Compaction: Initial pressure forms the powder into a green body, which is then sintered to achieve final density.
- Enhanced Bonding: Pressure ensures close contact between particles, facilitating atomic diffusion and bonding.
- Uniformity: Proper pressure application ensures uniformity in the final product, reducing defects and improving strength.
- Pressure is applied to compact the powdery materials into a solid mass.
-
Bonding Mechanisms
- Sintering relies on atomic diffusion to bond particles together.
- Surface Bonding: Adjacent particles bond at their surfaces, forming a continuous solid structure.
- Grain Growth: Over time, grains within the material grow, further strengthening the bond.
- Porosity Reduction: Sintering reduces porosity, making the material denser and more durable.
- Sintering relies on atomic diffusion to bond particles together.
-
Applications of Sintering
- Sintering is used in various industries to produce high-performance materials.
- Powder Metallurgy: Used to create metal components with complex shapes and high strength.
- Ceramics: Produces durable and heat-resistant ceramic products.
- Additive Manufacturing: Sintering is a key process in 3D printing, enabling the creation of intricate designs.
- High-Temperature Materials: Materials like tungsten and molybdenum are sintered for use in extreme environments.
- Sintering is used in various industries to produce high-performance materials.
-
Advantages of Sintering
- Sintering offers several benefits, including:
- Cost-Effectiveness: Reduces material waste and energy consumption compared to melting processes.
- Material Versatility: Can be applied to a wide range of materials, including metals, ceramics, and plastics.
- Enhanced Properties: Improves strength, hardness, and durability of the final product.
- Complex Shapes: Enables the production of complex geometries that are difficult to achieve with other methods.
- Sintering offers several benefits, including:
-
Challenges in Sintering
- Despite its advantages, sintering presents some challenges:
- Temperature Control: Maintaining precise temperatures is critical to avoid melting or incomplete bonding.
- Material Limitations: Not all materials are suitable for sintering, especially those with low melting points.
- Porosity Management: Achieving uniform density can be difficult, especially in large or complex parts.
- Despite its advantages, sintering presents some challenges:
In summary, sintering is a versatile and efficient process that transforms powdery materials into dense, durable products. Its key components—materials, heat, pressure, and bonding mechanisms—work together to create high-performance materials for a wide range of applications. By understanding these components, manufacturers can optimize the sintering process to meet specific needs and achieve superior results.
Summary Table:
Component | Details |
---|---|
Materials | Metal powders, ceramics, plastics, tungsten, molybdenum |
Heat Application | Applied below melting point; enables atomic diffusion and bonding |
Pressure Application | Compacts powder into a solid mass; ensures uniformity and strength |
Bonding Mechanisms | Atomic diffusion, surface bonding, grain growth, porosity reduction |
Applications | Powder metallurgy, ceramics, additive manufacturing, high-temperature uses |
Advantages | Cost-effective, versatile, enhances properties, enables complex shapes |
Challenges | Temperature control, material limitations, porosity management |
Discover how sintering can optimize your manufacturing process—contact our experts today!