Chemical Vapor Deposition (CVD) systems are essential in various industries for depositing thin films and coatings onto substrates. These systems are composed of several critical components that work together to ensure precise and efficient deposition processes. The key components of a CVD system include the gas delivery system, reactor chamber, substrate loading mechanism, energy source, vacuum system, exhaust system, exhaust treatment systems, and process control equipment. Each component plays a vital role in maintaining the stability, repeatability, and quality of the deposition process.
Key Points Explained:
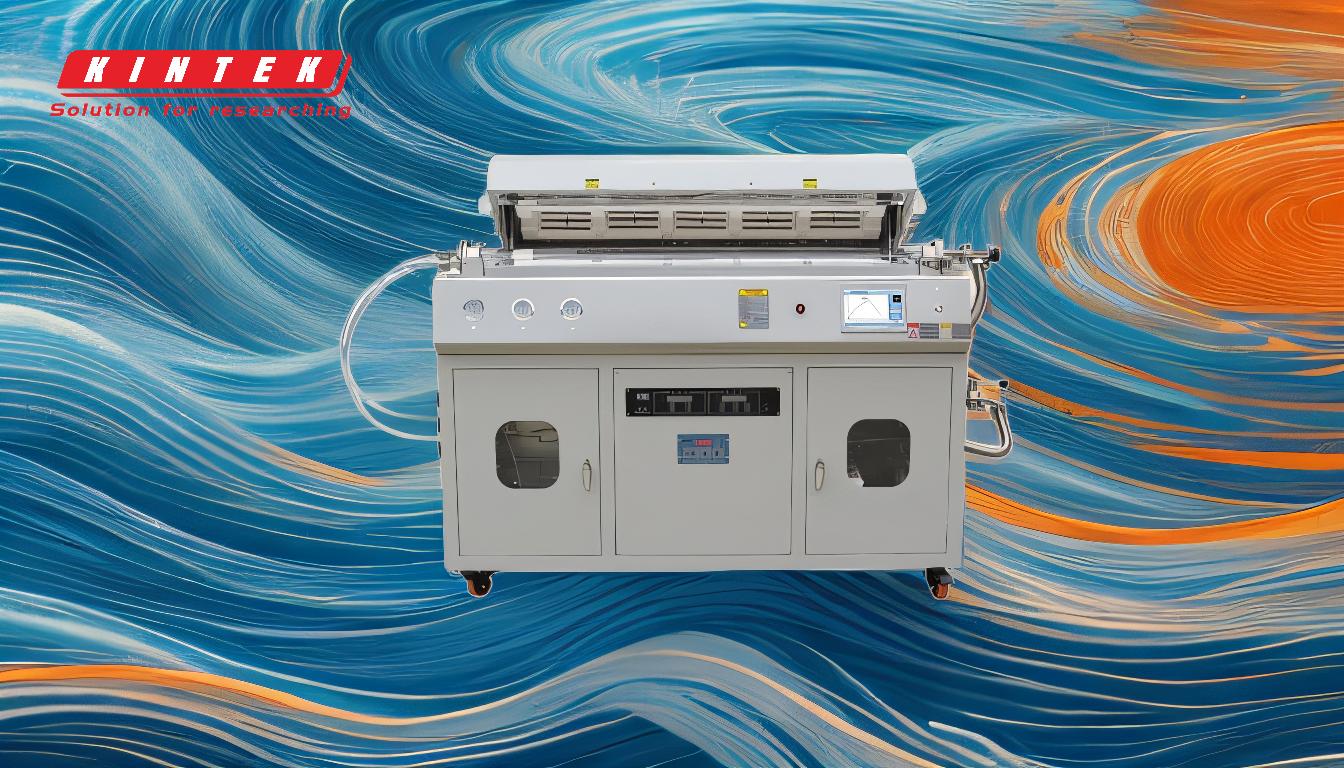
-
Gas Delivery System:
- The gas delivery system is responsible for supplying precursor gases to the reactor chamber. These gases are typically stored in high-pressure cylinders and are delivered through stainless steel feed lines.
- Mass flow controllers are used to regulate the flow rate of these precursor gases, ensuring precise control over the deposition process.
- The system may also include mixing chambers to combine different gases in specific ratios before they enter the reactor chamber.
-
Reactor Chamber:
- The reactor chamber is the core of the CVD system where the actual deposition process takes place. It is usually made of materials like quartz or stainless steel, which can withstand high temperatures and corrosive environments.
- The chamber houses the substrate, which is placed on a holder or susceptor. The substrate can be heated directly or indirectly to facilitate the deposition process.
- The chamber is designed to maintain a controlled atmosphere, often under vacuum or at specific pressures, to ensure uniform deposition.
-
Substrate Loading Mechanism:
- The substrate loading mechanism is used to introduce and remove substrates from the reactor chamber. This mechanism must be precise to avoid contamination and ensure consistent deposition.
- Automated systems may be used for loading and unloading substrates, especially in high-throughput industrial applications.
-
Energy Source:
- The energy source provides the heat required for the precursor gases to react or decompose on the substrate surface. Common energy sources include resistive heaters, induction heaters, or microwave generators.
- The choice of energy source depends on the specific requirements of the deposition process, such as the temperature range and the type of precursor gases used.
-
Vacuum System:
- The vacuum system is used to remove unwanted gaseous species from the reactor chamber, creating a controlled environment for deposition.
- The vacuum system typically includes pumps (such as rotary vane pumps, turbomolecular pumps, or cryogenic pumps) and pressure sensors to monitor and maintain the desired vacuum level.
-
Exhaust System:
- The exhaust system removes volatile by-products and unreacted precursor gases from the reactor chamber. This is crucial for maintaining the purity of the deposition environment and preventing contamination.
- The exhaust system may include filters and scrubbers to capture and neutralize harmful by-products before they are released into the atmosphere.
-
Exhaust Treatment Systems:
- Exhaust treatment systems are used to treat harmful exhaust gases before they are released into the environment. These systems may include chemical scrubbers, thermal oxidizers, or catalytic converters.
- The treatment process ensures that any toxic or hazardous by-products are neutralized, making the CVD process environmentally friendly.
-
Process Control Equipment:
- Process control equipment is essential for monitoring and regulating various parameters of the CVD process, such as temperature, pressure, gas flow rates, and deposition time.
- This equipment typically includes sensors, controllers, and software systems that provide real-time feedback and allow for precise adjustments to the process parameters.
- Advanced systems may also include automation and data logging capabilities to ensure repeatability and quality control.
In summary, a CVD system is a complex assembly of components that work together to achieve precise and controlled deposition of thin films. Each component, from the gas delivery system to the process control equipment, plays a critical role in ensuring the success of the CVD process. Understanding the function and importance of each component is essential for optimizing the deposition process and achieving high-quality results.
Summary Table:
Component | Function |
---|---|
Gas Delivery System | Supplies precursor gases, regulates flow rates, and mixes gases as needed. |
Reactor Chamber | Core area for deposition; maintains controlled atmosphere and temperature. |
Substrate Loading Mechanism | Introduces and removes substrates with precision to avoid contamination. |
Energy Source | Provides heat for precursor gas reactions or decomposition. |
Vacuum System | Removes unwanted gases and maintains a controlled environment. |
Exhaust System | Removes by-products and unreacted gases, ensuring deposition purity. |
Exhaust Treatment Systems | Neutralizes harmful exhaust gases for environmentally safe disposal. |
Process Control Equipment | Monitors and regulates temperature, pressure, gas flow, and deposition time. |
Optimize your thin film deposition process with a high-quality CVD system—contact our experts today!