Deposition techniques are essential in various industries, particularly for creating thin films and coatings on substrates. These techniques can be broadly categorized into physical and chemical methods, each with its unique processes and applications. Physical Vapor Deposition (PVD) is a common method where materials are vaporized in a low-pressure environment and then deposited onto a substrate. This method is known for producing durable, corrosion-resistant coatings that can withstand high temperatures. Other techniques like Electron Beam Deposition (E-Beam) and Sputtering Deposition offer precise control over film properties, such as thickness and adhesion, by using advanced technologies like electron-beam bombardment and ion beam enhancement. Each deposition method involves balancing various process conditions to achieve the desired film characteristics, such as uniformity, stress, and density.
Key Points Explained:
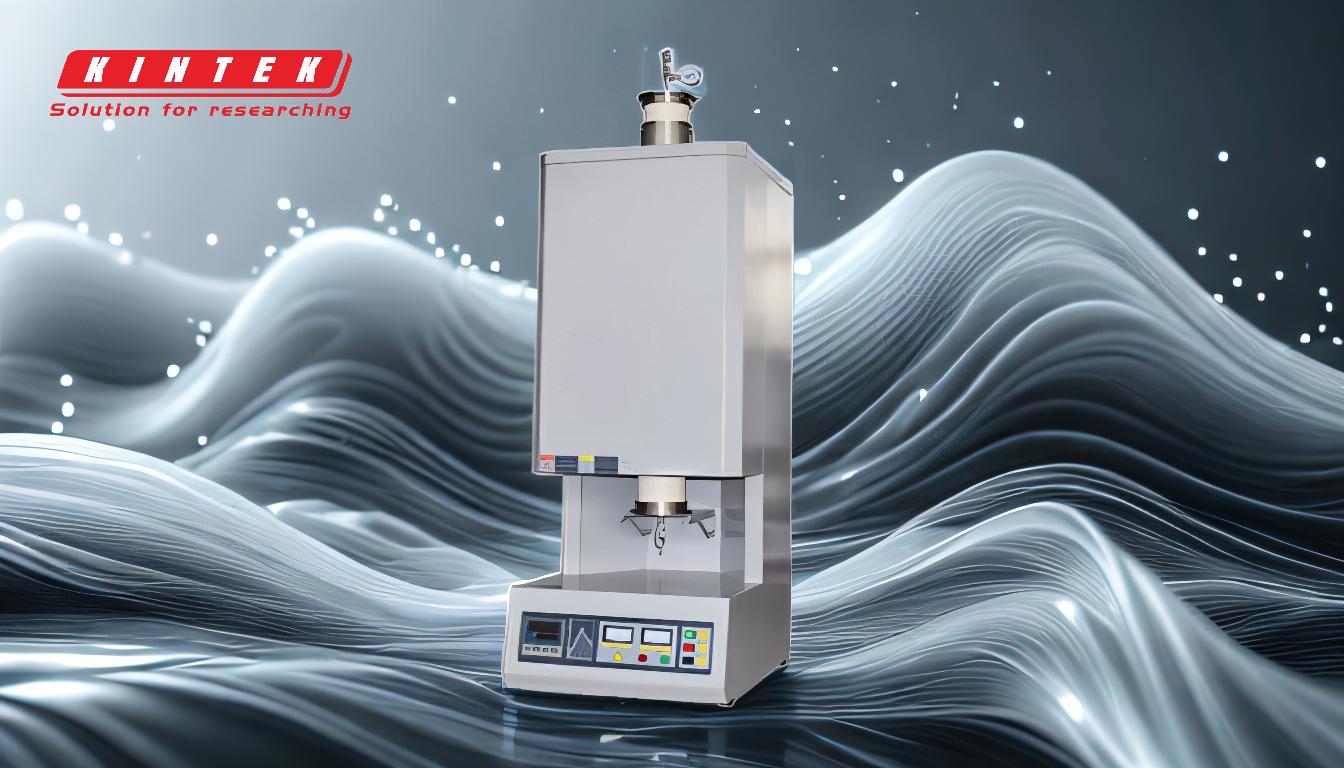
-
Physical Vapor Deposition (PVD):
- Process: Involves vaporizing materials in a low-pressure chamber and then depositing them onto a substrate.
- Applications: Produces highly durable, corrosion-resistant coatings that can tolerate high temperatures.
- Advantages: Suitable for creating robust films with specific mechanical and chemical properties.
-
Electron Beam Deposition (E-Beam):
- Process: Utilizes electron-beam bombardment to vaporize source materials, which then condense onto the substrate.
- Control: Precision computer control of heating, vacuum levels, substrate location, and rotation ensures conformal optical coatings of pre-specified thicknesses.
- Enhancements: Ion beam can be used to increase adhesion energy, resulting in denser and more robust coatings with less stress.
-
Sputtering Deposition:
- Process: High-energy ions of argon gas bombard the surface of the target material, removing its molecules, which then deposit on the substrate.
- Applications: Commonly used for creating thin films in semiconductor manufacturing and other high-tech industries.
- Advantages: Offers good control over film composition and uniformity.
-
Trade-offs in Deposition Processes:
- Factors: Deposition rates, power, temperature, and gas flows can significantly affect film properties.
- Balancing Act: Achieving the desired film characteristics often requires balancing these factors to optimize uniformity, stress, and density.
- Considerations: Faster deposition rates may necessitate higher power or temperatures, which can impact other film properties.
Each of these deposition techniques has its own set of advantages and challenges, making them suitable for different applications depending on the required film properties and process conditions. Understanding these methods and their trade-offs is crucial for selecting the appropriate technique for specific industrial needs.
Summary Table:
Technique | Process | Applications | Advantages |
---|---|---|---|
Physical Vapor Deposition (PVD) | Vaporizes materials in a low-pressure chamber, depositing them onto a substrate. | Durable, corrosion-resistant coatings for high-temperature applications. | Creates robust films with specific mechanical and chemical properties. |
Electron Beam Deposition (E-Beam) | Uses electron-beam bombardment to vaporize materials, condensing onto the substrate. | Precision optical coatings with controlled thickness and adhesion. | Denser, more robust coatings with less stress; enhanced by ion beam technology. |
Sputtering Deposition | High-energy argon ions bombard the target material, depositing molecules on the substrate. | Thin films for semiconductor manufacturing and high-tech industries. | Excellent control over film composition and uniformity. |
Need help selecting the right deposition technique for your application? Contact our experts today!