Cooling methods after heat treatment are critical for achieving desired material properties, such as hardness, strength, and ductility. The choice of cooling method depends on the material, the heat treatment process, and the desired outcome. Common methods include slow cooling in a furnace, quenching in various media (water, oil, gases, or polymers), and cooling with inert gases like argon in vacuum furnaces. Each method has specific applications and benefits, with quenching being the most widely used for rapid cooling. Understanding these methods helps in selecting the appropriate cooling technique for specific material and performance requirements.
Key Points Explained:
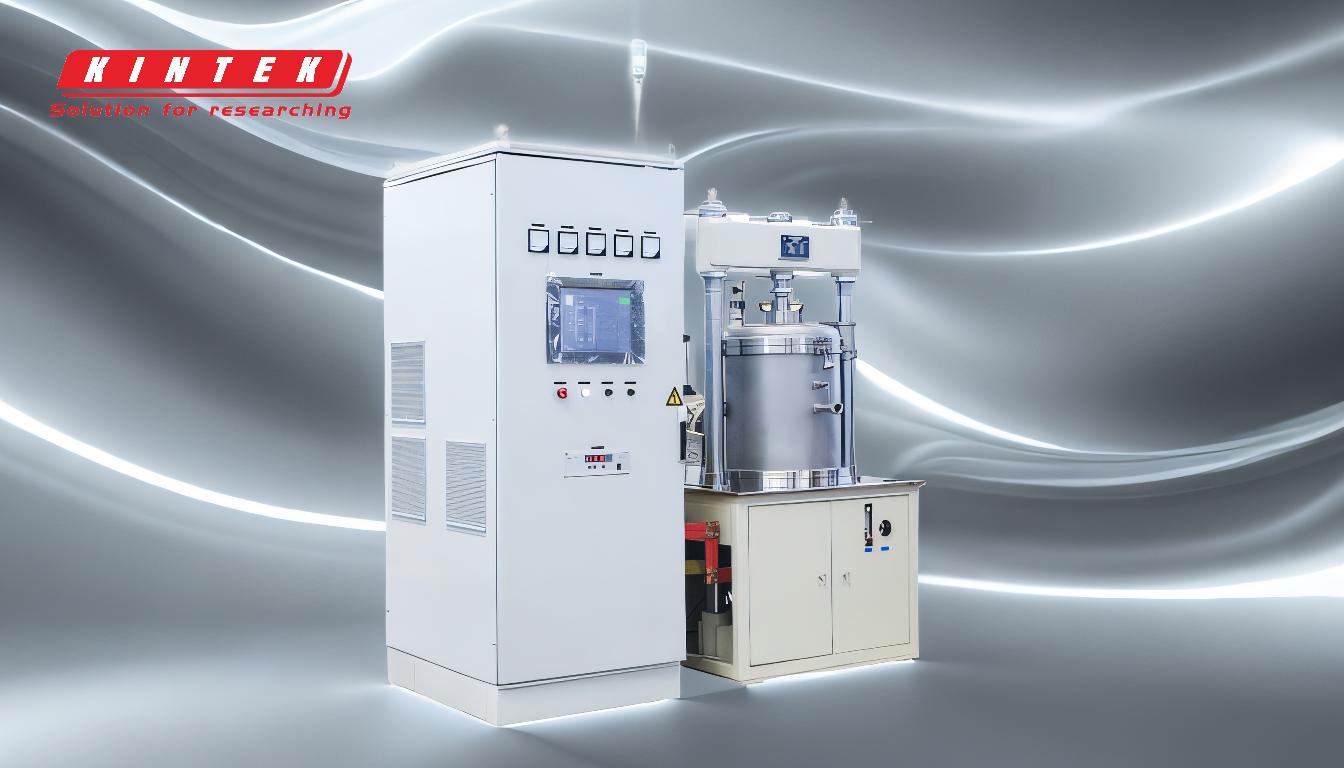
-
Slow Cooling in Furnace
- Process: After heat treatment, some materials are cooled slowly within the furnace. This method allows the material to cool at a controlled rate, preventing thermal stresses and ensuring uniform cooling.
- Applications: Typically used for processes like annealing, where the goal is to soften the material, relieve internal stresses, and improve ductility.
- Benefits: Reduces the risk of cracking or warping, making it suitable for materials that are sensitive to rapid temperature changes.
-
Quenching
- Process: Quenching involves rapidly cooling the material by immersing it in a quenching medium. Common media include water, brine, oils, polymer solutions, molten salts, molten metals, and gases.
- Applications: Widely used in processes like hardening and tempering to achieve high hardness and strength. About 90% of parts are quenched in water, oil, gases, or polymers.
- Benefits: Rapid cooling helps in achieving the desired microstructure and mechanical properties. However, it can introduce internal stresses, which may require subsequent tempering.
-
Cooling with Inert Gases
- Process: In vacuum furnace heat treatment, parts are cooled by cycling inert gases such as argon into the heating chamber. Inert gases are ideal because they do not react chemically with the material.
- Applications: Suitable for materials that require a controlled cooling environment, such as high-precision components or those sensitive to oxidation.
- Benefits: Provides a clean, non-reactive cooling environment, reducing the risk of contamination and ensuring uniform cooling.
-
Specific Quenching Media
- Water and Brine: Provide very rapid cooling, ideal for achieving high hardness in steels. However, they can cause distortion or cracking due to the high cooling rate.
- Oils: Offer a slower cooling rate compared to water, reducing the risk of cracking. Commonly used for alloy steels and tool steels.
- Polymer Solutions: Provide a cooling rate between water and oil, offering a balance between hardness and reduced risk of distortion.
- Molten Salts and Metals: Used for specialized applications where precise control over cooling rates is required.
- Gases: Such as nitrogen or argon, used in gas quenching for high-precision components, providing a clean and uniform cooling environment.
-
Selection of Cooling Method
- Material Considerations: The choice of cooling method depends on the material's properties and the desired outcome. For example, steels often require quenching for hardness, while aluminum alloys may benefit from slow cooling.
- Process Requirements: The heat treatment process (e.g., annealing, hardening, tempering) dictates the cooling method. Rapid cooling is essential for hardening, while slow cooling is preferred for annealing.
- Component Geometry: Complex shapes may require controlled cooling to prevent distortion or cracking, making methods like gas quenching or polymer solutions more suitable.
-
Post-Cooling Treatments
- Tempering: Often performed after quenching to relieve internal stresses and improve toughness. The material is reheated to a lower temperature and then cooled slowly.
- Stress Relieving: A heat treatment process used to reduce residual stresses in materials, often involving slow cooling to prevent new stresses from forming.
Understanding these cooling methods and their applications is crucial for selecting the appropriate technique to achieve the desired material properties and performance characteristics.
Summary Table:
Cooling Method | Process | Applications | Benefits |
---|---|---|---|
Slow Cooling in Furnace | Controlled cooling within the furnace to prevent thermal stresses. | Annealing to soften materials and improve ductility. | Reduces cracking and warping, ideal for sensitive materials. |
Quenching | Rapid cooling using water, oil, polymers, or gases. | Hardening and tempering for high hardness and strength. | Achieves desired microstructure but may require tempering to relieve stress. |
Cooling with Inert Gases | Cooling in vacuum furnaces using argon or nitrogen. | High-precision components and oxidation-sensitive materials. | Ensures clean, uniform cooling without contamination. |
Quenching Media | Water, brine, oils, polymers, molten salts, or gases. | Tailored for specific materials and cooling needs. | Balances hardness and reduced distortion risks. |
Post-Cooling Treatments | Tempering and stress relieving to improve toughness and reduce residual stress. | Essential after quenching to enhance material performance. | Improves toughness and reduces internal stresses. |
Need help selecting the best cooling method for your heat treatment process? Contact our experts today for personalized guidance!