Thin film deposition techniques are essential for creating thin layers of material on substrates, with applications ranging from electronics to optics. These techniques are broadly categorized into physical vapor deposition (PVD) and chemical vapor deposition (CVD), each with its own sub-techniques. PVD methods, such as evaporation and sputtering, rely on physical processes to deposit materials, while CVD methods, including plasma-enhanced CVD and atomic layer deposition, use chemical reactions. Other methods like spin coating and spray pyrolysis also play a role in specific applications. Understanding these techniques helps in selecting the right method for precise control over film thickness, composition, and quality.
Key Points Explained:
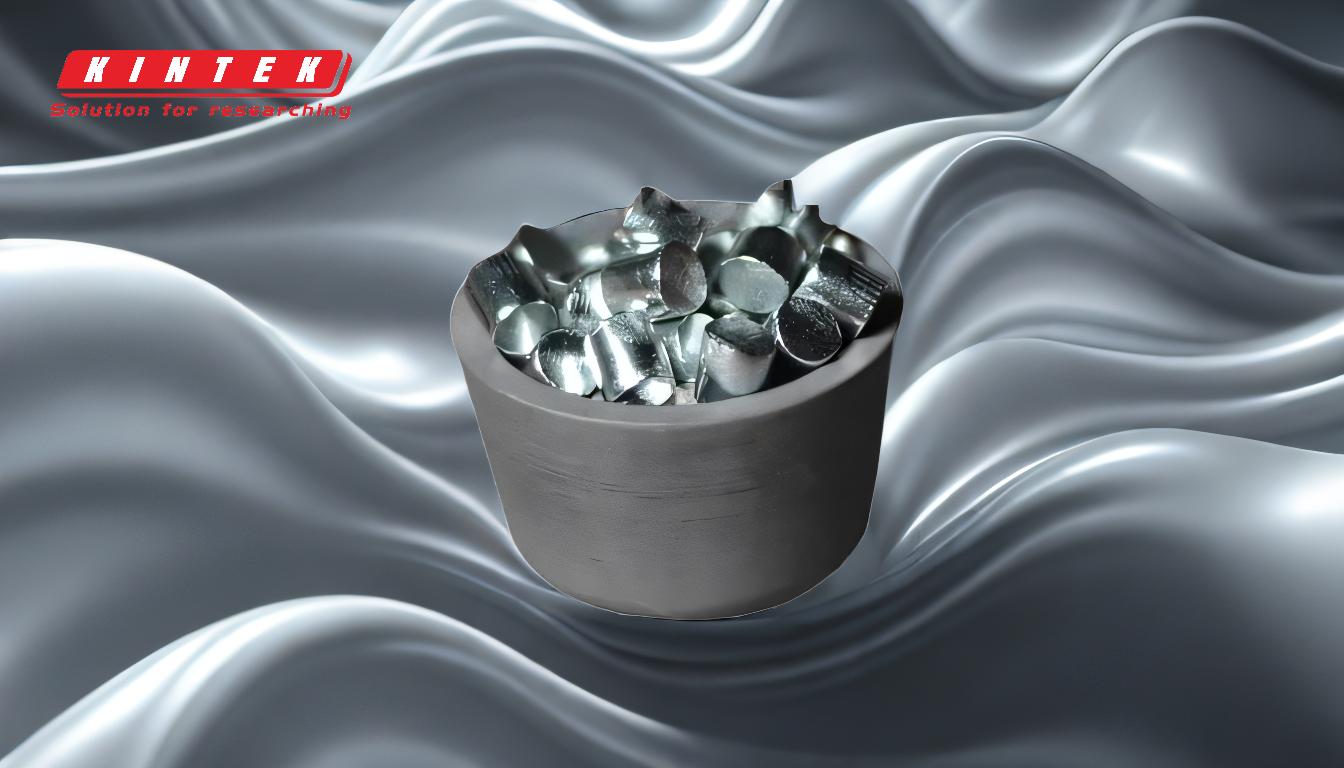
-
Physical Vapor Deposition (PVD):
- Definition: PVD involves vaporizing a solid material in a vacuum and depositing it onto a substrate.
-
Techniques:
- Evaporation: The material is heated until it vaporizes and then condenses on the substrate. Techniques include thermal evaporation and electron beam evaporation.
- Sputtering: High-energy particles bombard a target material, ejecting atoms that deposit onto the substrate. Methods include magnetron sputtering and ion beam sputtering.
- Molecular Beam Epitaxy (MBE): A highly controlled form of evaporation used for growing high-quality crystalline films.
- Pulsed Laser Deposition (PLD): A laser ablates material from a target, which then deposits onto the substrate.
-
Chemical Vapor Deposition (CVD):
- Definition: CVD uses chemical reactions to deposit a thin film on a substrate from gaseous precursors.
-
Techniques:
- Standard CVD: Reactant gases are introduced into a chamber, where they react on the substrate surface to form a solid film.
- Plasma-Enhanced CVD (PECVD): Plasma is used to enhance the chemical reaction, allowing deposition at lower temperatures.
- Atomic Layer Deposition (ALD): Films are deposited one atomic layer at a time, providing exceptional control over thickness and uniformity.
-
Other Deposition Techniques:
- Spin Coating: A liquid precursor is applied to a substrate, which is then spun at high speed to spread the material into a thin, uniform layer.
- Spray Pyrolysis: A solution containing the material is sprayed onto a heated substrate, where it decomposes to form a thin film.
- Electroplating: An electrical current is used to deposit a metal layer onto a conductive substrate.
- Sol-Gel: A colloidal solution (sol) is used to form a gel, which is then dried and sintered to create a thin film.
-
Comparison of PVD and CVD:
-
PVD:
- Advantages: High purity, good adhesion, and compatibility with a wide range of materials.
- Disadvantages: Requires high vacuum, limited to line-of-sight deposition.
-
CVD:
- Advantages: Excellent step coverage, high deposition rates, and ability to deposit complex materials.
- Disadvantages: High temperatures and hazardous gases may be required.
-
PVD:
-
Applications:
- PVD: Used in semiconductor manufacturing, optical coatings, and decorative finishes.
- CVD: Common in microelectronics, solar cells, and protective coatings.
- Other Techniques: Spin coating is widely used in photolithography, while spray pyrolysis is used in solar cell fabrication.
By understanding these techniques, one can select the appropriate method based on the desired film properties, substrate material, and application requirements.
Summary Table:
Technique | Category | Key Methods | Advantages | Disadvantages |
---|---|---|---|---|
PVD | Physical | Evaporation, Sputtering, MBE, PLD | High purity, good adhesion, wide material compatibility | Requires high vacuum, limited to line-of-sight deposition |
CVD | Chemical | Standard CVD, PECVD, ALD | Excellent step coverage, high deposition rates, complex material compatibility | High temperatures, hazardous gases |
Spin Coating | Other | - | Uniform layers, cost-effective | Limited to specific materials and applications |
Spray Pyrolysis | Other | - | Simple, scalable | Limited control over film thickness |
Electroplating | Other | - | Low cost, good for conductive substrates | Limited to metals, uneven thickness |
Sol-Gel | Other | - | Versatile, low-temperature processing | Time-consuming, limited to specific materials |
Need help selecting the right thin film deposition technique for your project? Contact our experts today!