Chemical vapor deposition (CVD) is a versatile and widely used technique for depositing thin films of materials onto substrates. It involves the decomposition of volatile compounds into atoms and molecules, which then react to form a solid film on the substrate. CVD can be categorized into several types based on the operating conditions, precursor delivery methods, and energy sources used. These include atmospheric pressure CVD (APCVD), low-pressure CVD (LPCVD), high-vacuum CVD (UHVCVD), subatmospheric pressure CVD (SACVD), aerosol-assisted CVD, direct liquid injection CVD, and plasma-enhanced CVD (PECVD). Each method has unique advantages, such as high purity, uniformity, and scalability, making CVD suitable for various applications in industries like semiconductors, optics, and coatings.
Key Points Explained:
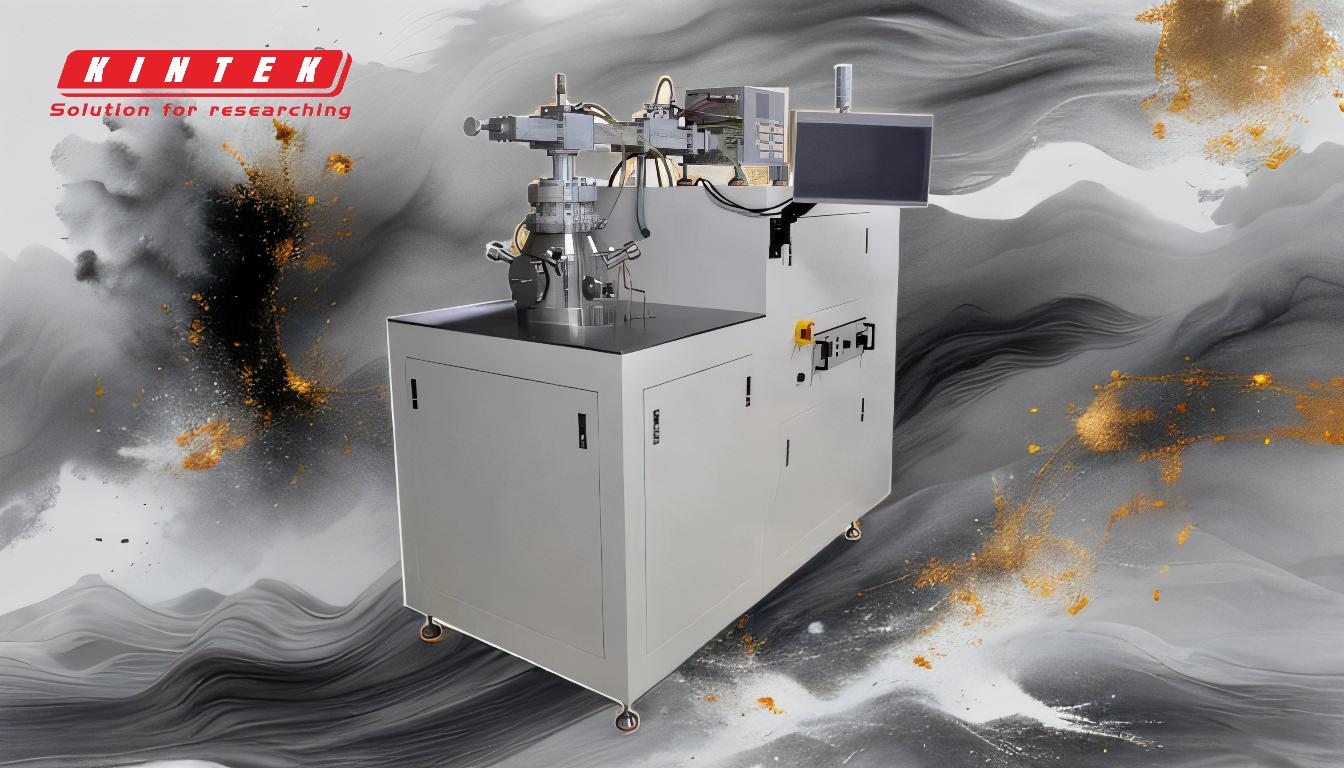
-
Atmospheric Pressure CVD (APCVD):
- Operates at atmospheric pressure, making it simpler and more cost-effective.
- Ideal for large-scale production due to its high deposition rates.
- Commonly used for depositing oxides, nitrides, and polysilicon in semiconductor manufacturing.
- The reaction rate is mass-transfer-limited, meaning the process is influenced by the flow of reactants to the substrate.
-
Low-Pressure CVD (LPCVD):
- Operates at reduced pressures, typically between 0.1 to 10 Torr.
- Provides better film uniformity and step coverage compared to APCVD.
- The reaction rate is surface-reaction-limited, allowing precise control over film properties.
- Widely used for depositing silicon nitride, silicon dioxide, and polysilicon in microelectronics.
-
High-Vacuum CVD (UHVCVD):
- Operates under ultra-high vacuum conditions, reducing contamination and improving film purity.
- Suitable for depositing high-quality epitaxial layers and complex materials.
- Often used in advanced semiconductor and optoelectronic applications.
-
Subatmospheric Pressure CVD (SACVD):
- Operates at pressures between atmospheric and low-pressure CVD.
- Combines the advantages of APCVD and LPCVD, offering good film quality and moderate deposition rates.
- Used for depositing dielectric layers in integrated circuits.
-
Aerosol-Assisted CVD (AACVD):
- Uses aerosolized precursors, making it easier to handle and deliver solid or liquid precursors.
- Suitable for depositing complex materials and coatings on irregular surfaces.
- Commonly used in research and development for novel materials.
-
Direct Liquid Injection CVD (DLI-CVD):
- Involves injecting a liquid precursor into a heated chamber, where it vaporizes and reacts to form the film.
- Offers precise control over precursor delivery and composition.
- Ideal for depositing metal oxides, nitrides, and other complex materials.
-
Plasma-Enhanced CVD (PECVD):
- Uses plasma to activate the chemical reactions, allowing deposition at lower temperatures.
- Suitable for temperature-sensitive substrates and materials.
- Widely used for depositing silicon nitride, silicon dioxide, and amorphous silicon in microelectronics and solar cells.
-
Advantages of CVD:
- High purity and uniformity of deposited films.
- Ability to deposit a wide range of materials, including single-crystal, polycrystalline, and amorphous films.
- Scalability for industrial production.
- Tunable film properties by controlling parameters like temperature, pressure, and gas flow rates.
-
Limitations of CVD:
- High equipment and operational costs.
- Limited to certain material sizes and shapes (e.g., synthetic diamonds up to 3.2 carats).
- Requires careful control of process parameters to avoid defects.
-
Applications of CVD:
- Semiconductor manufacturing (e.g., transistors, interconnects).
- Optical coatings (e.g., anti-reflective, protective layers).
- Protective and functional coatings (e.g., wear-resistant, corrosion-resistant layers).
- Synthesis of advanced materials (e.g., graphene, carbon nanotubes).
For more details on the equipment used in these processes, you can explore the chemical vapor deposition system.
Summary Table:
Type of CVD | Key Features | Applications |
---|---|---|
Atmospheric Pressure CVD (APCVD) | Operates at atmospheric pressure, high deposition rates, mass-transfer-limited. | Semiconductor manufacturing (oxides, nitrides, polysilicon). |
Low-Pressure CVD (LPCVD) | Reduced pressure (0.1-10 Torr), surface-reaction-limited, better uniformity. | Microelectronics (silicon nitride, silicon dioxide, polysilicon). |
High-Vacuum CVD (UHVCVD) | Ultra-high vacuum, high film purity, suitable for epitaxial layers. | Advanced semiconductors and optoelectronics. |
Subatmospheric Pressure CVD (SACVD) | Moderate pressure, combines APCVD and LPCVD advantages. | Dielectric layers in integrated circuits. |
Aerosol-Assisted CVD (AACVD) | Uses aerosolized precursors, suitable for irregular surfaces. | Research and development for novel materials. |
Direct Liquid Injection CVD (DLI-CVD) | Precise precursor delivery, ideal for complex materials. | Metal oxides, nitrides, and other complex materials. |
Plasma-Enhanced CVD (PECVD) | Uses plasma for low-temperature deposition. | Microelectronics and solar cells (silicon nitride, silicon dioxide). |
Discover the right CVD method for your needs—contact our experts today for personalized advice!