Deposition techniques are essential in various industries for creating thin films and coatings on substrates. The two primary categories are Physical Vapor Deposition (PVD) and Chemical Vapor Deposition (CVD). PVD involves physically transferring materials to a substrate in a vacuum, while CVD uses chemical reactions of gases to form films. Each technique has unique processes and applications, with trade-offs between film properties and process conditions. Understanding these methods helps in selecting the right technique for specific applications, ensuring optimal film characteristics such as durability, uniformity, and adhesion.
Key Points Explained:
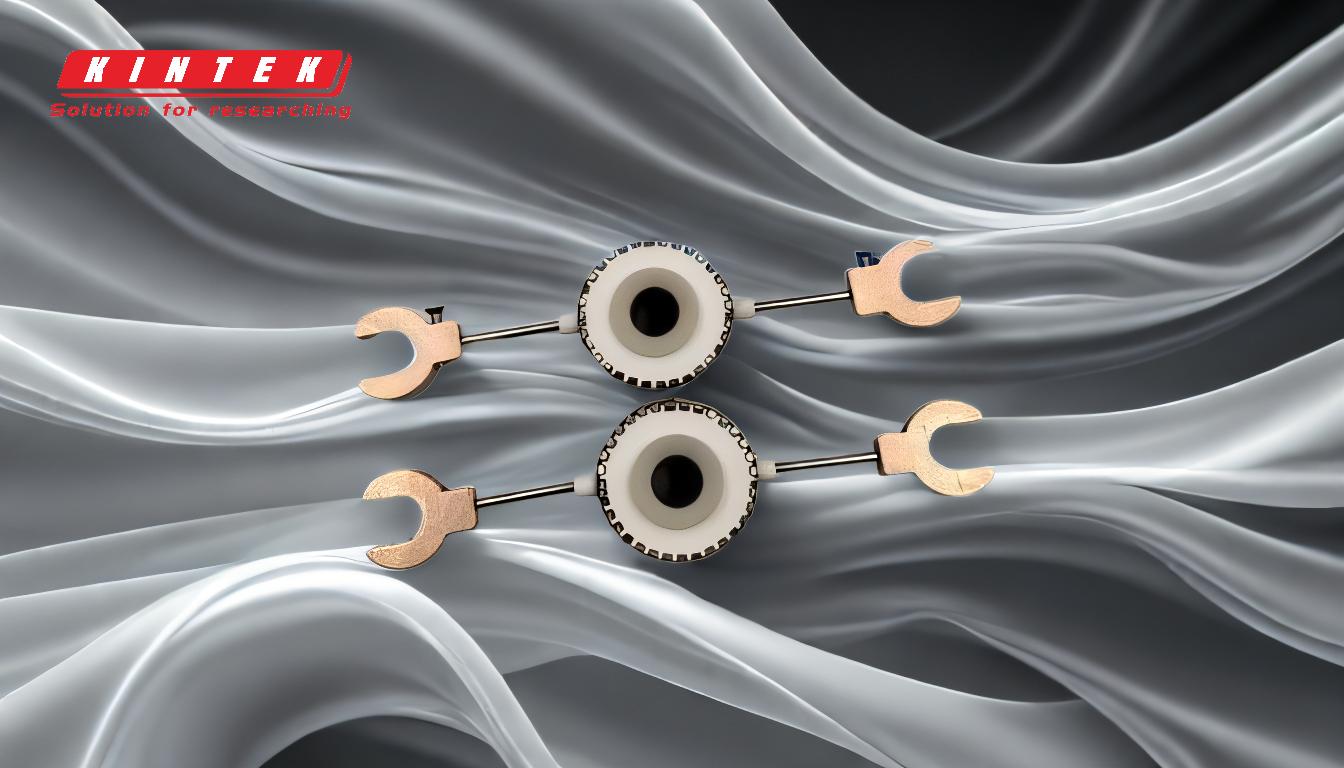
-
Physical Vapor Deposition (PVD):
- Process: PVD involves vaporizing materials in a low-pressure chamber and depositing them onto a substrate. Techniques include heating, sputtering, and electron beam deposition.
- Applications: PVD is used to create highly durable, corrosion-resistant coatings that can withstand high temperatures. It is commonly used in the semiconductor, optical, and tool coating industries.
- Advantages: PVD provides excellent control over film thickness and uniformity, resulting in high-quality coatings with strong adhesion and minimal stress.
-
Chemical Vapor Deposition (CVD):
- Process: CVD uses chemical reactions of gaseous precursors to form a solid film on the substrate. The process occurs in a controlled environment with specific temperatures and pressures.
- Applications: CVD is widely used in the production of semiconductors, thin-film solar cells, and protective coatings. It is also used to create high-purity materials like diamond films.
- Advantages: CVD allows for the deposition of complex and uniform films over large areas. It can produce films with excellent conformality and high purity.
-
Electron Beam Deposition (E-Beam):
- Process: In E-Beam deposition, source materials are vaporized using electron-beam bombardment. The vapor condenses onto the substrate, forming a thin film. The process is enhanced with ion beams to improve adhesion and film density.
- Applications: E-Beam deposition is used in optical coatings, semiconductor devices, and precision engineering.
- Advantages: This technique offers precise control over film thickness and uniformity, producing dense and robust coatings with minimal stress.
-
Sputtering Deposition:
- Process: Sputtering involves bombarding a target material with high-energy ions (usually argon gas), causing atoms to be ejected and deposited onto the substrate.
- Applications: Sputtering is used in the production of thin films for electronics, optics, and decorative coatings.
- Advantages: Sputtering provides excellent film uniformity and can deposit a wide range of materials, including metals, alloys, and compounds.
-
Trade-offs in Deposition Techniques:
- Process Conditions vs. Film Properties: Faster deposition rates often require higher power, temperatures, or gas flows, which can impact film characteristics such as uniformity, stress, and density. Balancing these factors is crucial for achieving the desired film properties.
- Selection Criteria: The choice of deposition technique depends on the specific requirements of the application, including the desired film properties, substrate material, and production scale.
By understanding the different types of deposition techniques and their respective advantages, industries can make informed decisions to achieve optimal results in their applications.
Summary Table:
Technique | Process | Applications | Advantages |
---|---|---|---|
Physical Vapor Deposition (PVD) | Vaporizes materials in a vacuum, depositing them onto a substrate. | Semiconductor, optical, and tool coating industries. | Excellent control over thickness, strong adhesion, minimal stress. |
Chemical Vapor Deposition (CVD) | Uses chemical reactions of gases to form films on a substrate. | Semiconductors, thin-film solar cells, protective coatings, high-purity materials. | Uniform films, excellent conformality, high purity. |
Electron Beam Deposition (E-Beam) | Vaporizes materials using electron-beam bombardment. | Optical coatings, semiconductor devices, precision engineering. | Precise thickness control, dense and robust coatings. |
Sputtering Deposition | Bombards target material with high-energy ions, depositing atoms on a substrate. | Electronics, optics, decorative coatings. | Excellent uniformity, versatile material deposition. |
Need help choosing the right deposition technique for your application? Contact our experts today!